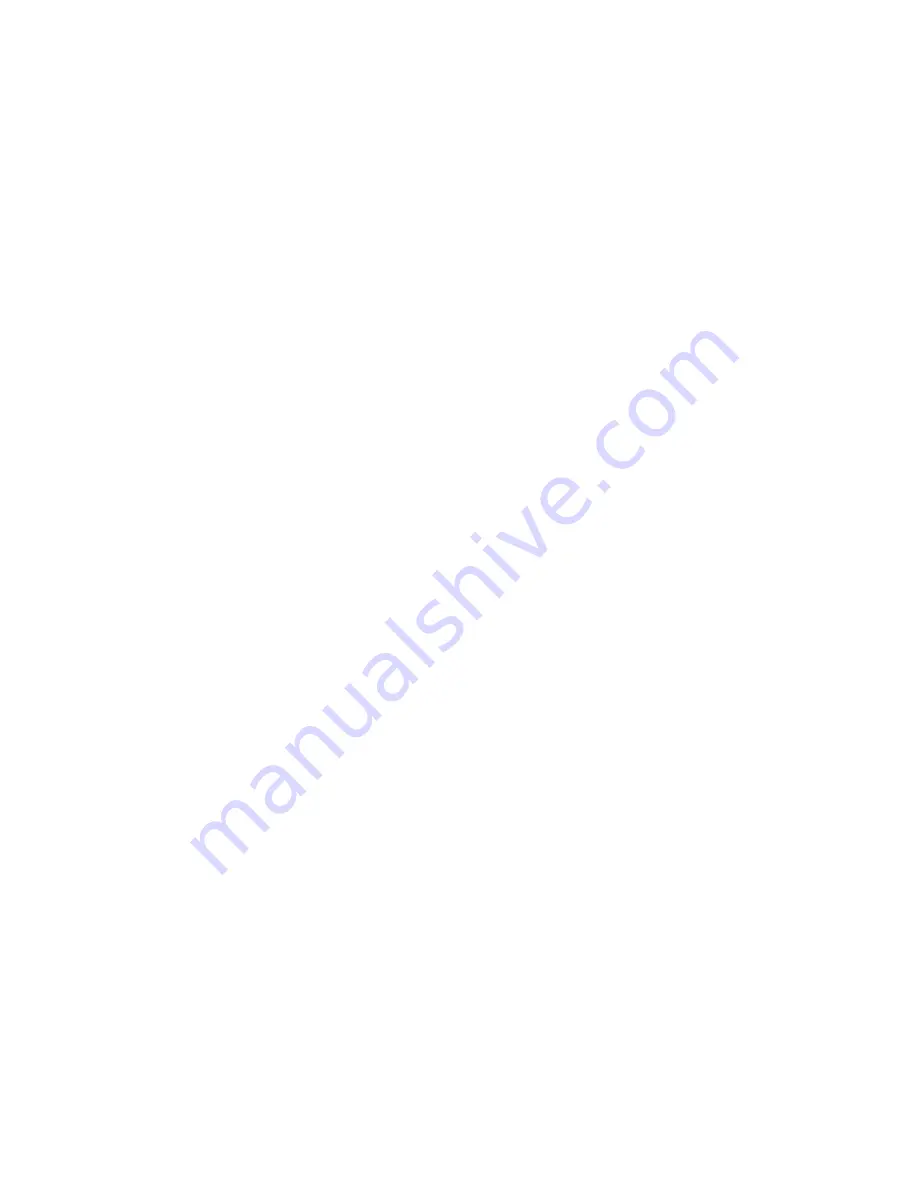
52
TQ10X User Guide
➄
Adjust Tuning Parameters
Vary the tuning parameters to improve motor performance and to achieve
satisfactory motion—only tune for absolute maximum performance if the application
requires it. Typical responses and suggested adjustments are:
Sluggish Motion – Increase proportional gain (CPG) or decrease derivative gain
(CDG) to make the motor respond more quickly. Use caution when you increase
CPG—too much will cause the system to oscillate and become unstable. If you
increase CPG and your system becomes unstable, disable the drive immediately.
Oscillatory or Erratic Motion – Increase derivative gain (CDG) or decrease
proportional gain (CPG) to help damp out oscillatory motion. Too much CDG
will cause a sluggish or overdamped response; excessive CDG may cause the
system to become unstable. If you increase CDG and your system becomes
unstable, disable the drive immediately. You can try increasing the derivative
sampling period (CTG) to control instability. For most applications, CTG will
not need to be higher than 4.
Steady State Errors – See Step 9 for information about controlling steady state
errors by adjusting integral gain and integral limit parameters. Because integral
gain reduces stability, it should only be adjusted after you determine settings for
CPG, CDG, and CTG.
If you still need to improve performance after you adjust CPG, CDG, and CTG,
proceed to Step 6.
➅
Increase Peak Current
Using the DIP switches, increase peak current to the next level. Do not exceed three
times the motor’s continuous current rating. Closely monitor the motor immediately
after you increase peak current. Be prepared to disable the drive if the system shows
any signs of instability.
You can change the DIP switches with power applied—the drive will immediately
sense the new current setting. For safety reasons, however, we recommend removing
power from the drive before changing DIP switches.
➆
Repeat Steps 4 – 6
With higher peak current, you can evaluate system performance and readjust tuning
parameters if necessary. Continue repeating Steps 4 – 6 until you achieve satisfactory
performance.
➇
Choose Final Tuning Values
Program your applications’s actual move, and select final tuning values based upon
the performance you observe.
➈
Determine Integral Gain (CIG) and Integral Limit (CIL) Values
Increasing integral gain (CIG) will reduce position errors at the end of the move and
velocity errors during the constant velocity portion of the move. However, high
values for CIG can cause the system to become unstable. If you increase CIG and
your system becomes unstable, disable the drive immediately. In general, you should
set CIG to the lowest value that will correct following errors and static position
errors, but not increase overshoot or settling time. In a system without static torque
loading, a CIG of zero may be appropriate.
Artisan Technology Group - Quality Instrumentation ... Guaranteed | (888) 88-SOURCE | www.artisantg.com
Содержание TQ10X
Страница 13: ...4 TQ10X User Guide Artisan Technology Group Quality Instrumentation Guaranteed 888 88 SOURCE www artisantg com...
Страница 55: ...46 TQ10X User Guide Artisan Technology Group Quality Instrumentation Guaranteed 888 88 SOURCE www artisantg com...
Страница 63: ...54 TQ10X User Guide Artisan Technology Group Quality Instrumentation Guaranteed 888 88 SOURCE www artisantg com...
Страница 113: ...104 TQ10X User Guide Artisan Technology Group Quality Instrumentation Guaranteed 888 88 SOURCE www artisantg com...
Страница 137: ...128 TQ10X User Guide Artisan Technology Group Quality Instrumentation Guaranteed 888 88 SOURCE www artisantg com...