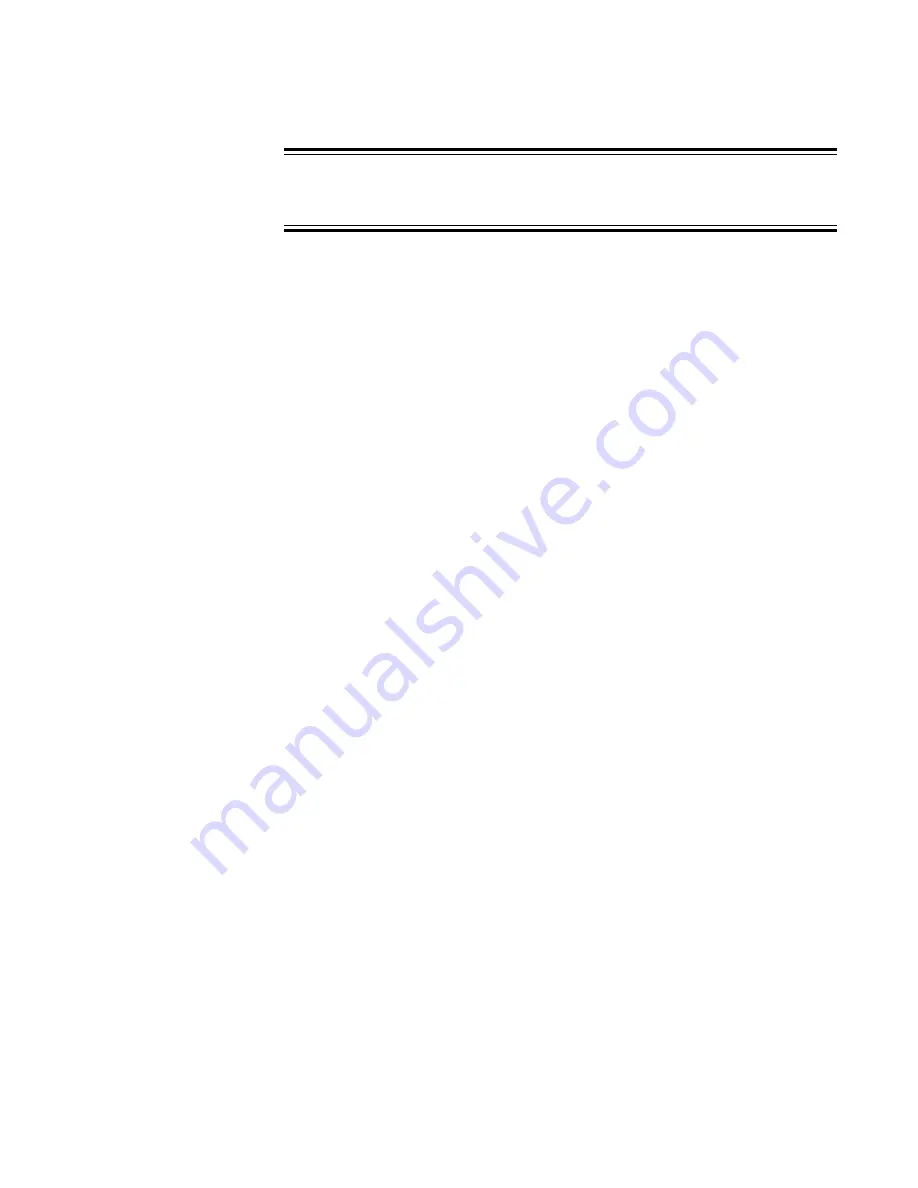
➃
Tuning
49
load new parameters by using buffered versions of the five tuning commands
(BCPG, BCDG, BCTG, BCIG, BCIL).
WARNING
During servo tuning, the system can undergo accidental and violent movement due to
improper gain settings and programming errors. Please use extreme caution while
prototyping.
Each tuning parameter is described in the following sections.
CPG – Proportional Gain
Proportional gain provides a torque that is directly proportional to the magnitude of
the error signal. Proportional gain is similar to a spring—the larger the error, the
larger the restoring force. It determines the stiffness of the system and affects the
following error. High proportional gain gives a stiff, responsive system, but can
result in overshoot and oscillation. Damping—provided by derivative gain—can
reduce this overshoot and oscillation.
CDG – Derivative Gain; CTG – Derivative Sampling Period
Derivative gain provides a torque that is directly proportional to the rate of change
of the error signal. The previous error is subtracted from the present error each
sampling period. The difference represents the error’s instantaneous rate of change,
or derivative. The difference is multiplied by the value set by the CDG command,
and the product contributes to the motor control output.
Derivative gain opposes rapid changes in velocity. It will dampen the resonance
effects of proportional gain. With higher derivative gain, you can use higher
proportional gain.
You can use the CTG command to make the derivative sampling period longer
than the system’s sampling period. The system sampling period—266 µsec—is the
period between updates of position error, and cannot be changed. The derivative
sampling period is an integer multiple of the system sampling period. It can range
from 266 µsec to 68 msec, in increments of 266µsec (for example: CTG0 = 266 µs,
CTG1 = 532 µs, CTG2 = 798 µs, etc.).
With a longer derivative sampling period, more time elapses between derivative
error measurements. The difference between previous and present error is still
multiplied by the CDG value. The product contributes to the motor control output
every system sampling period, but is only updated every derivative sampling
period. This gives a more constant derivative term and improves stability. Low
velocity systems in particular can benefit from a longer sampling period.
Because of stability considerations, however, the derivative sampling period should
be no longer than one tenth of the system mechanical time constant. This means
many systems must have low values of CTG.
CIG – Integral Gain; CIL – Integral Limit
Integral gain provides a torque that is directly proportional to the sum, over time, of
the error values—the integral of the error. The controller reads the error value
every sampling period, and adds it to the sum of all previous error values. The sum
is multiplied by the value set by the CIG command (Integral * CIG), resulting in
the integral term which contributes to the motor control output every system
sampling period.
Artisan Technology Group - Quality Instrumentation ... Guaranteed | (888) 88-SOURCE | www.artisantg.com
Содержание TQ10X
Страница 13: ...4 TQ10X User Guide Artisan Technology Group Quality Instrumentation Guaranteed 888 88 SOURCE www artisantg com...
Страница 55: ...46 TQ10X User Guide Artisan Technology Group Quality Instrumentation Guaranteed 888 88 SOURCE www artisantg com...
Страница 63: ...54 TQ10X User Guide Artisan Technology Group Quality Instrumentation Guaranteed 888 88 SOURCE www artisantg com...
Страница 113: ...104 TQ10X User Guide Artisan Technology Group Quality Instrumentation Guaranteed 888 88 SOURCE www artisantg com...
Страница 137: ...128 TQ10X User Guide Artisan Technology Group Quality Instrumentation Guaranteed 888 88 SOURCE www artisantg com...