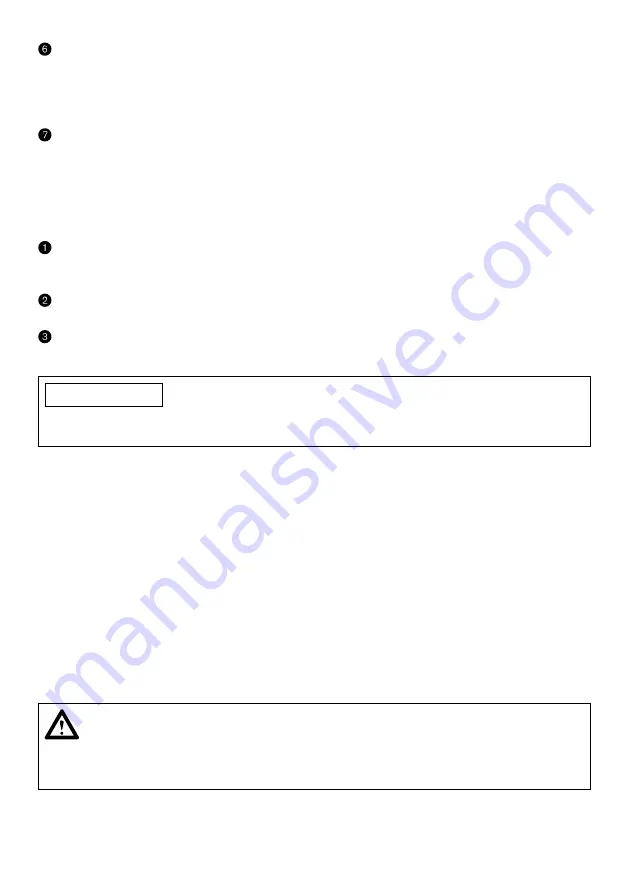
Ottobock | 13
Now position the socket such that the alignment reference line passes through the proximal
centre mark of the socket. Set the socket flexion to somewhere between 3° and 5°; however,
the individual situation (e.g. hip joint contractures) must be taken into account and, if neces-
sary, more flexion should be provided. Also pay attention to the ischial tuberosity to ground
distance.
Connect the socket and modular knee joint using a corresponding lamination anchor (see
Section 4.3.1.2).
4.1.2 Static alignment optimization using L.A.S.A.R. Posture 743L100
(the following steps refer to Fig. 7)
The bench alignment can be substantially improved using L.A.S.A.R. Posture. In order to ensure
appropriate stability combined with easy swing phase initiation, please proceed as follows:
To make the load line visible, the transfemoral amputee stands on the L.A.S.A.R. Posture with
the prosthetic side on the force plate and with the other leg on the height compensation panel.
The prosthesis side should be sufficiently loaded (> 35 % of the body weight).
Now adapt the alignment by only adjusting the plantar flexion of the foot. The load line (laser
line) should be approx. 35 mm anterior to the front knee axis (see Fig. 7).
After step 2, dynamic optimisation can take place between parallel bars.
4.2 Combination possibilities
INFORMATION
In a prosthesis, all prosthetic components have to meet the patient's requirements regarding the
amputation level, body weight, activity level, environmental conditions and field of application.
4.3 Adjustments and final assembly
4.3.1 Socket fabrication
4.3.1.1 Lamination prior to trial fitting
Take a piece of 623T3 Perlon Stockinette twice the length of the plaster model and pull half of it
over the isolated socket. Twist the other half of the stockinette at the distal end and pull it over the
socket as well. To strengthen the modular knee joint, the socket must be incrementally reinforced
with a 616G13 Fiberglass Stockinette. To do so, pull a first layer of fiberglass stockinette two-
thirds over the socket length. Tie off and pull remaining stockinette halfway back over the socket.
Place 2 layers of 616G12 Carbon Fiber Cloth on the distal area such that the to-be-mounted
4G70 Adapter will have a carbon fiber basis with a 3 cm rim. Pull over two layers of 623T3 Perlon
Stockinette. The socket will be laminated twice with two different resins. For the first casting, the
socket is laminated up to two-thirds of its length with 617H19 Orthocryl Lamination Resin. Once the
casting has hardened, apply 2 more layers of 623T3 Perlon Stockinette. For the second casting,
the proximal part of the socket is laminated with 617H17 Orthocryl Flexible Resin.
The lamination anchor serves to restrict flexion by stopping at the axle bushing of the
lower joint section (2) (Fig. 2). This stop function must also be taken into consideration
after the final lamination. To ensure a proper flexion stop and to prevent damage, the set
screw (12), which may be too long for certain adjustment positions, should be replaced
by a shorter one (12a).
4.3.1.2 Applying the lamination anchor
The correctly fitted lamination anchor must be prepared before it is glued to the socket. To do so,
Содержание 3R23 INOX
Страница 3: ...Ottobock 3 2 4 5 3...
Страница 96: ...96 Ottobock 6 A Ottobock Ottobock 7 CE 93 42 VII...
Страница 98: ...98 Ottobock 2 3 3 2 4 5 6 1 4 5 26 22 19 3R21 3R30 3 3R23 3R32 110 880 655 99 17 82 125 1 4 4 1...
Страница 102: ...102 Ottobock 5 3R30 3R21 6R6 3R6 3S106 519L5 6 Ottobock 7 7 1...
Страница 113: ...Ottobock 113 Ottobock 7 7 1 7 2 CE 93 42 EWG IX I VII...