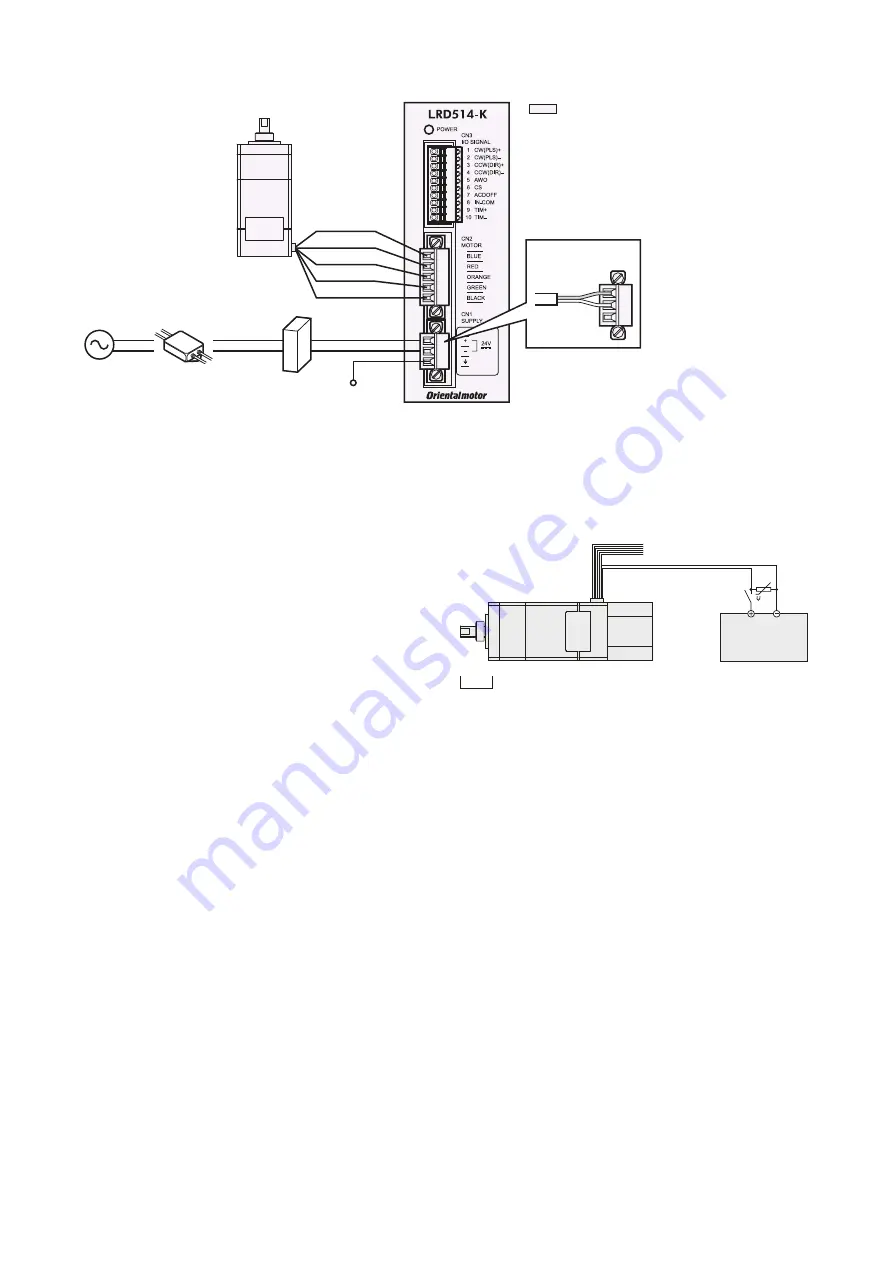
48
●
Connection Diagram
◇
Connections with Peripheral Equipment
GND
+24 VDC
FG
AWG22(0.3 mm
2
)
5
4
3
2
1
GND
+
24 V
Included with product.
DC Power Supply
24 VDC±10%
Blue
Red
Orange
Green
Black
Pay attention to the power
supply polarity.
Noise Filter
Use as protection against
noise.
This is effective for reducing
noise generated from the
power supply and driver.
AC
Power Supply
●
Keep the wiring distance between the actuator and driver to 10 m max..
◇
Power Supply Connection
Use the included connector for CN1 to connect the power cable
(AWG22: 0.3 mm
2
) to the driver's power connector (CN1).
Connecting the DC power-supply input with the polarity reversed
would damage the driver (circuits). Make sure that the polarity is
correct before turning power on.
Provide a power supply that can supply adequate input current.
If the power supply capacity is inadequate, abnormalities such as
the following occur.
●
The actuator does not operate normally in high-speed operation.
●
The actuator does not accelerate or decelerate as set.
◇
Extension of Motor Lead
Use a wire of AWG22 (0.3 mm
2
) min.
◇
Connecting the Electromagnetic Brake
Use power supplies of 24 VDC±5%
✽
, 0.25 A min. (for the
DRL42
,
0.08 A min.)
Surge
Suppressor
(Included)
Switch
Black/White
Red/White
24 VDC
±
5%
✽
0.25 A
min.
(
DRL42
:
0.08 A
min.)
Motor Leads
Electromagnetic
Brake Leads
✽
If the wiring distance is extended by 20 m or more, the specification becomes 24 VDC
±
4%.
Notes
●
Applying voltage exceeding the specifications causes actuator failure.
●
To protect the switch contacts and prevent noise, always connect a surge suppressor.
(The surge suppressor is included with electromagnetic brake motors.)