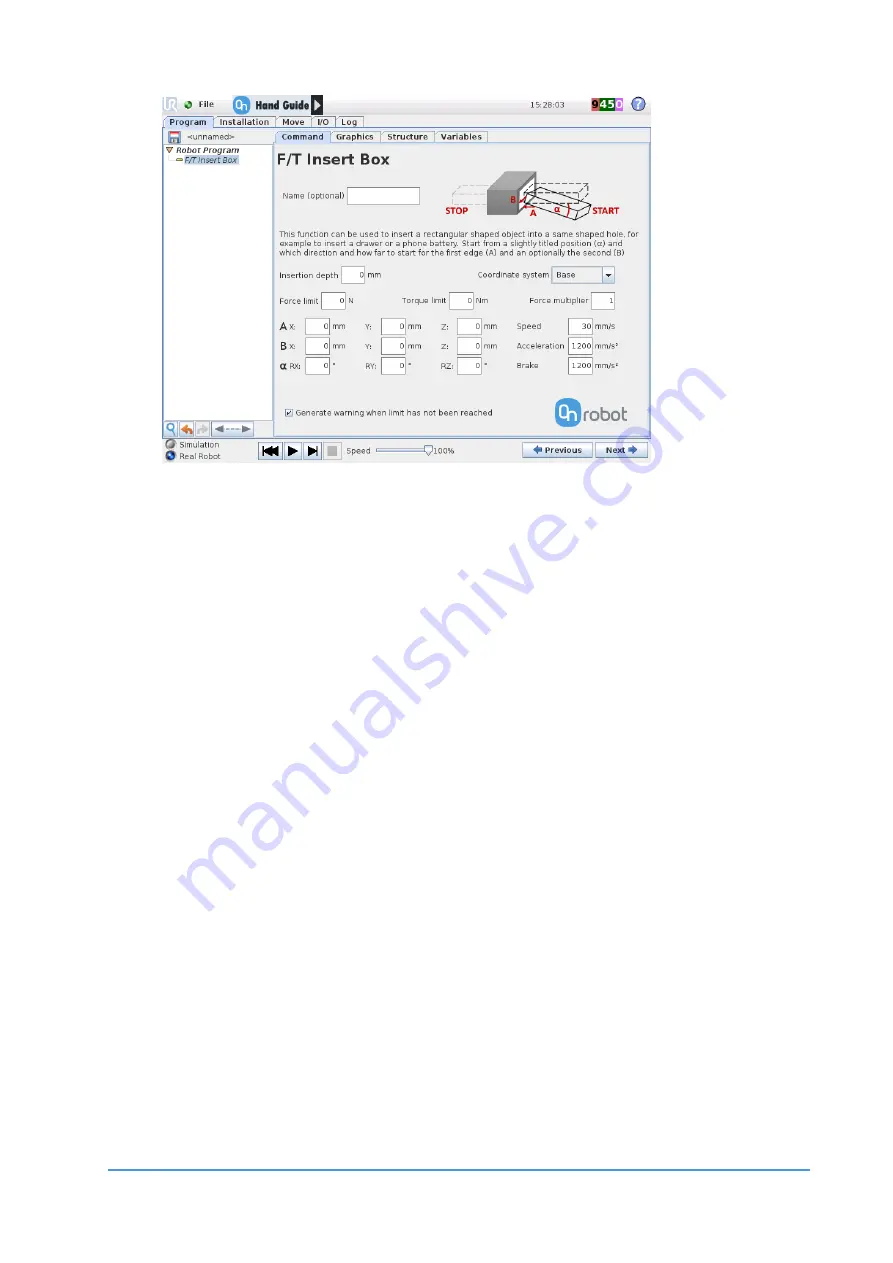
Using the URCap Plugin
35
OnRobot © 2018
www.onrobot.com
Insertion depth (D)
: The distance from the Starting point along the defined axis in
phase A.
Coordinate system:
The coordinate system used both for the movement and for
the sensor reading. It can be set to
Base
or
Tool
(according to the UR’s reference
frames).
Force limit (N):
The force limit for the edge detection.
Torque limit (Nm):
The torque limit for the orientation adjustment.
Force multiplier:
The force limit for the edge detection is multiplied by this value,
to calculate the force limit for the final insertion.
Generate warning (…):
If enabled then a pop-up message (blocking) appears if
the insertion was not successful.
If disabled then no pop-up message is shown but the user can handle any possible
errors by the return value of the command. The command updates the
of_return
variable once the command exit. This global variable can be used with the UR’s built
in
If
conditional expressions (for example:
if of_return == 1
then do
something).
F/T Insert Box Command Return Values