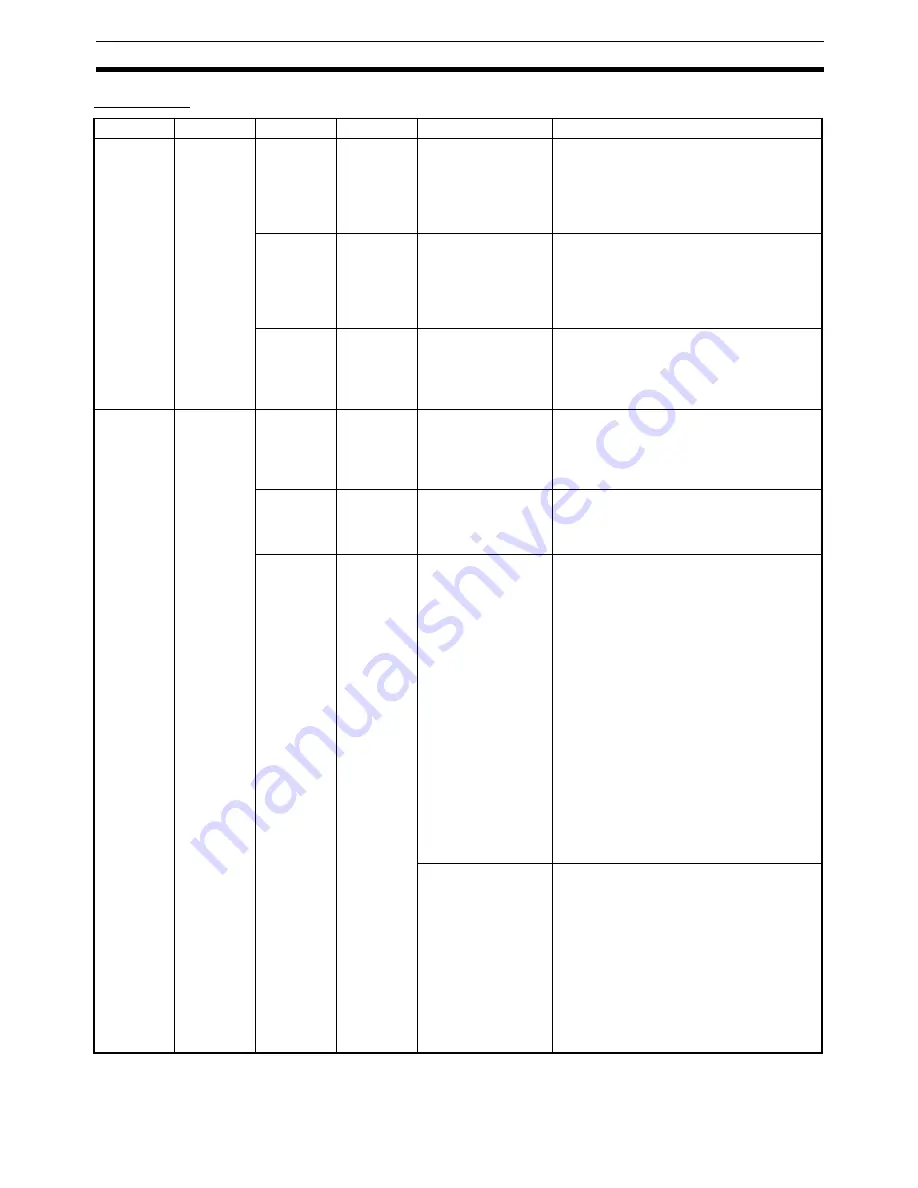
95
Error Codes
Section 11-2
Axis Errors
Category
Error name Error code
Probable cause
Clearing method
MECHA-
TROLINK
communi-
cations
errors
Communi-
cations
error
Synchro-
nous com-
munications
alarm
3010
MECHATROLINK
communications
cannot be per-
formed correctly with
the corresponding
axis.
Check the connection of the MECHA-
TROLINK communications cable. Remove
the cause preventing communications, such
as breaks or noise in the connection, and
then execute CONNECT again.
Communi-
cations
alarm
3011
MECHATROLINK
communications
cannot be per-
formed correctly with
the corresponding
axis.
Check the connection of the MECHA-
TROLINK communications cable. Remove
the cause preventing communications, such
as breaks or noise in the connection, and
then execute CONNECT again.
Command
time-out
3012
No MECHATROLINK
communications
response has been
received from the
corresponding axis.
Check that no error has occurred in the
MECHATROLINK device connected to the
corresponding axis, and then execute CON-
NECT again.
Position
Control Unit
settings
and opera-
tions errors
Illegal oper-
ations
Present
position
unknown
error
3030
ABSOLUTE MOVE-
MENT or ORIGIN
RETURN was exe-
cuted before the ori-
gin was established.
Execute ORIGIN SEARCH or PRESENT
POSITION PRESET to define the origin,
and then execute the previously unsuccess-
ful command again.
Servo
unlock error
3040
A command to start
the axis was exe-
cuted while in Servo
unlock status.
Execute the SERVO LOCK and then exe-
cute the previously unsuccessful command
again.
Multistart
error
3050
An attempt was
made to execute two
or more of the follow-
ing commands at the
same time for the
same axis.
ABSOLUTE
MOVEMENT, REL-
ATIVE MOVE-
MENT, ORIGIN
SEARCH, ORIGIN
RETURN,
PRESENT POSI-
TION PRESET,
JOG, SPEED
CONTROL,
TORQUE CON-
TROL, DEVICE
SETUP, or ERROR
RESET
Edit the ladder program so that multiple
command bits do not turn ON at the same
time for the same axis, and then execute the
previously unsuccessful command again.
An attempt was
made to execute one
of the following com-
mands for a busy
axis.
ORIGIN SEARCH,
ORIGIN RETURN,
PRESENT POSI-
TION PRESET,
JOG, DEVICE
SETUP, or ERROR
RESET
Edit the ladder program so that command
bits do not turn ON for a busy axis, and then
execute the previously unsuccessful com-
mand again.
Содержание CX-MOTION-NCF - V1.9
Страница 1: ...Cat No W436 E1 09 CX Motion NCF Ver 1 9 SYSMAC CXONE AL_C V3 CXONE AL_D V3 OPERATION MANUAL...
Страница 2: ......
Страница 3: ...CXONE AL C V3 CXONE AL D V3 CX Motion NCF Ver 1 9 Operation Manual Revised September 2009...
Страница 4: ...iv...
Страница 6: ...vi...
Страница 20: ...xx...
Страница 24: ...xxiv Application Precautions 5...
Страница 36: ...12 Connecting to PLC Section 2 2...
Страница 39: ...15 Screen Name Section 3 1 Edit Parameter Windows Edit Unit Parameters Window Edit Servo Parameters Window...
Страница 40: ...16 Screen Name Section 3 1 Monitor Windows Axis Monitor Window Unit Monitor Window...
Страница 66: ...42 Editing Servo Parameters Section 5 2...
Страница 71: ...47 Print Section 6 5 Print Samples An example of printed Unit Parameters is shown below...
Страница 92: ...68 Writing to Flash Memory Section 7 6...
Страница 98: ...74 Axis Monitor Section 8 2 2 Click the OK Button to start communications i e establish connection...
Страница 106: ...82 Axis Monitor Section 8 2...
Страница 107: ...83 SECTION 9 Test Run Operation This section describes the test run operations for each axis 9 1 Test Run 84...
Страница 112: ...88 Test Run Section 9 1...
Страница 138: ...114 Troubleshooting Section 11 3...
Страница 142: ...118 Index...
Страница 146: ...122 Revision History...