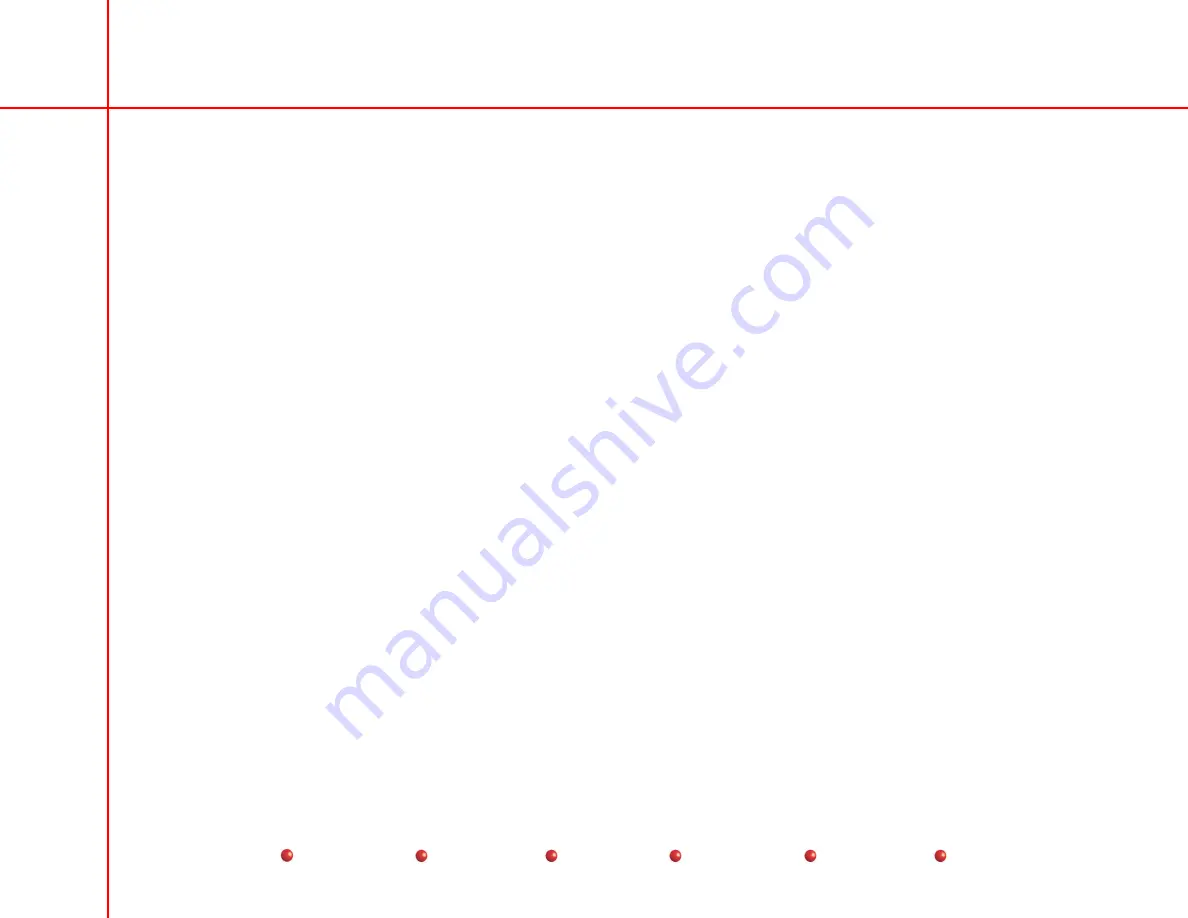
OEC 9800 Periodic Maintenance Procedure
52
18. Repeat the previous step for the remaining Iris Positions and when you have filled in all of the Dose Rate fields,
click on the Calculate Constants command button.
19. After the constants have been calculated click on the File pulldown menu and click on Download DAP data.
20. Archive the DAP calibration data to disk by selecting the File pulldown menu and clicking on Save DAP Calibration
File As. Specify the drive letter and path.
Battery Replacement
PCB Batteries
1.
Replace the X-ray Controller PCB Battery (Coin type CR2032, 3.0 Volt, Lithium, P/N 74-122905-00).
2.
Replace the Workstation Motherboard PCB Battery or PC Card battery (Coin type CR2032, 3.0 Volt, Lithium, P/N
74-122905-00).
Note
:
Replace the battery in the Motherboard / PC Card every two years.
a.
Locate the sticker (P/N 88-359989-00) on the Electronic Card Rack Cover. The sticker will indicate when the
battery was last replaced. If a sticker is not present, determine the systems date of manufacture by locating
the System Regulatory Label.
b.
If two years has elapsed or will have elapsed before the next scheduled service date, replace the battery and
replace the current sticker with a new sticker. Indicate the date that you replaced the battery on the sticker.