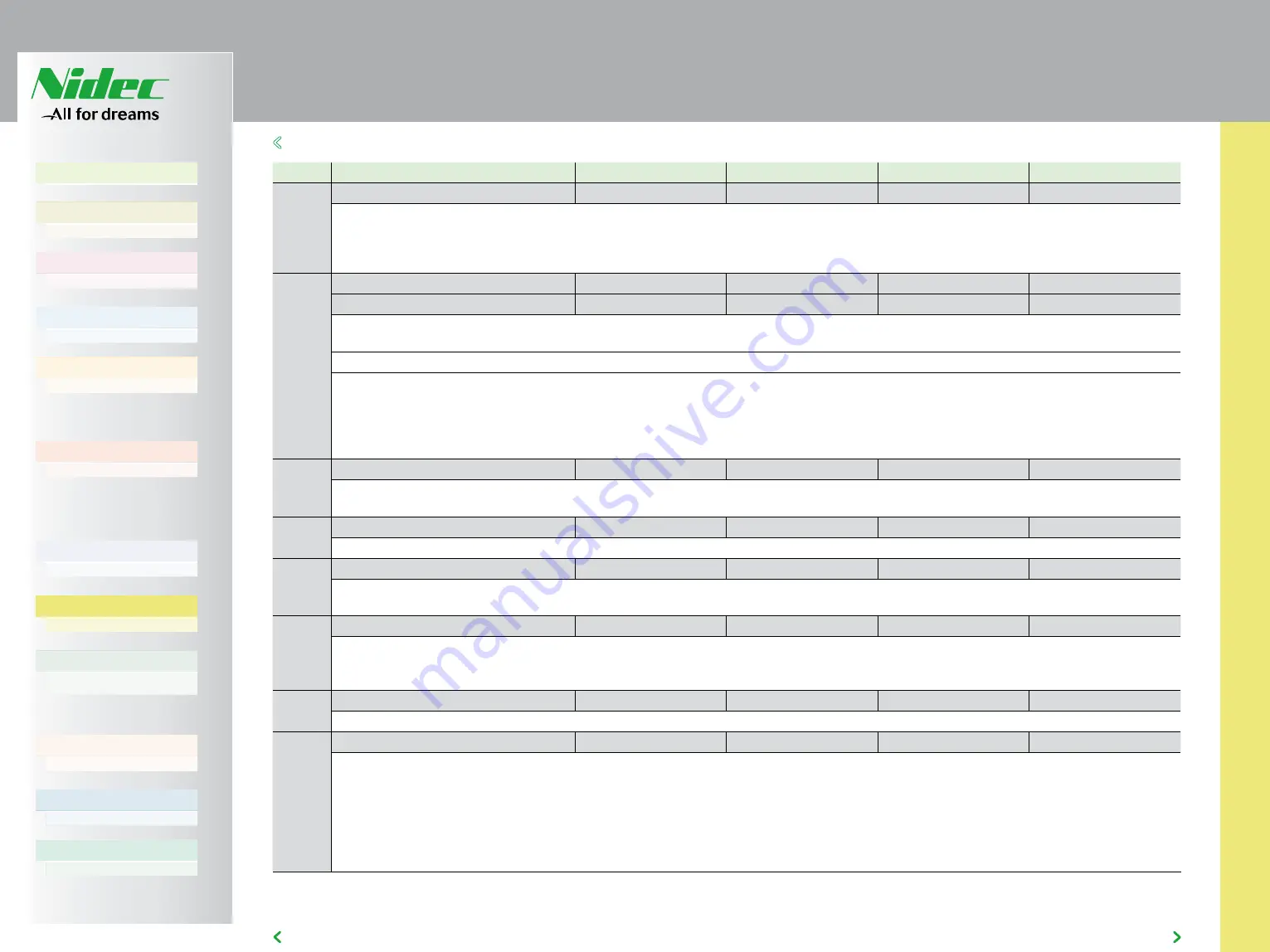
Summary
Chapter 1
P. 5
Chapter 2
P. 7
Chapter 3
P. 12
Chapter 4
P. 15
Chapter 5
P. 21
Chapter 6
P. 29
Chapter 7
P. 31
Chapter 8
P. 42
AD700E
37
General information
Important safety information
General Information and Ratings
Mechanical Installation
Operation
Parameters
Analog and Digital Input Macro
Configurations
Power Wiring
Chapter 9
P. 48
Chapter 10
P. 50
Modbus RTU Communications
Technical Data
Trouble Shooting
Chapter 11
P. 54
PREVIOUS VIEW
5/6
7
7.2 EXTENDED P
ARAMETERS
Par
Description
Minimum
Maximum
Default
Units
P-39
Analog Input 1 Offset
-500.0
500.0
0.0
%
Sets an offset, as a percentage of the full scale range of the input, which is applied to the analog input signal. This parameter operates in
conjunction with P-35, and the resultant value can be displayed in P00-01.
The resultant value is defined as a percentage, according to the following :
P00-01 = (Applied Signal Level(%) x P-35) - P-39
P-40
Index 1 : Display Scaling Factor
0
3
0
-
Index 2 : Display Scaling Source
0.000
16.000
0.000
-
Allows the user to program the AD700E to display an alternative output unit scaled from either output frequency (Hz), Motor Speed (RPM) or
the signal level of PI feedback when operating in PI Mode.
Index 1 :
Used to set the scaling multiplier. The chosen source value is multiplied by this factor.
Index 2 :
Defines the scaling source as follows :
0 : Motor Speed.
Scaling is applied to the output frequency if P-10 = 0, or motor RPM if P-10 > 0.
1 : Motor Current.
Scaling is applied to the motor current value (Amps)
2 : Analog Input 2 Signal Level.
Scaling is applied to analog input 2 signal level, internally represented as 0 – 100.0%
3 : PI Feedback.
Scaling is applied to the PI feedback selected by P-46, internally represented as 0 – 100.0%
P-41
PI Controller Proportional Gain
0.0
30.0
1.0
-
PI Controller Proportional Gain. Higher values provide a greater change in the drive output frequency in response to small changes in the
feedback signal. Too high a value can cause instability
P-42
PI Controller Integral Time
0.0
30.0
1.0
s
PI Controller Integral Time. Larger values provide a more damped response for systems where the overall process responds slowly
P-43
PI Controller Operating Mode
0
1
0
-
0 : Direct Operation.
Use this mode if when the feedback signal drops, the motor speed should increase.
1 : Inverse Operation.
Use this mode if when the feedback signal drops, the motor speed should decrease.
P-44
PI Reference (Setpoint) Source Select
0
1
0
-
Selects the source for the PID Reference / Setpoint
0 : Digital Preset Setpoint.
P-45 is used
1 : Analog Input 1 Setpoint.
Analog input 1 signal level, readable in P00-01 is used for the setpoint.
P-45
PI Digital Setpoint
0.0
100.0
0.0
%
When P-44 = 0, this parameter sets the preset digital reference (setpoint) used for the PI Controller as a % of the feedback signal range.
P-46
PI Feedback Source Select
0
5
0
-
Selects the source of the feedback signal to be used by the PI controller.
0 : Analog Input 2
(Terminal 4) Signal level readable in P00-02.
1 : Analog Input 1
(Terminal 6) Signal level readable in P00-01
2 : Motor Current.
Scaled as % of P-08.
3 : DC Bus Voltage
Scaled 0 – 1000 Volts = 0 – 100%
4 : Analog 1 – Analog 2.
The value of Analog Input 2 is subtracted from Analog 1 to give a differential signal. The value is limited to 0.
5 : Largest (Analog 1, Analog 2).
The largest of the two analog input values is always used for PI feedback.
Содержание AD07-E-1-1-023-1-0002
Страница 1: ...INSTALLATION OPERATING INSTRUCTIONS IMAD700E1EN REV 1 01 31 07 2015...
Страница 56: ...www nidec industrial com...