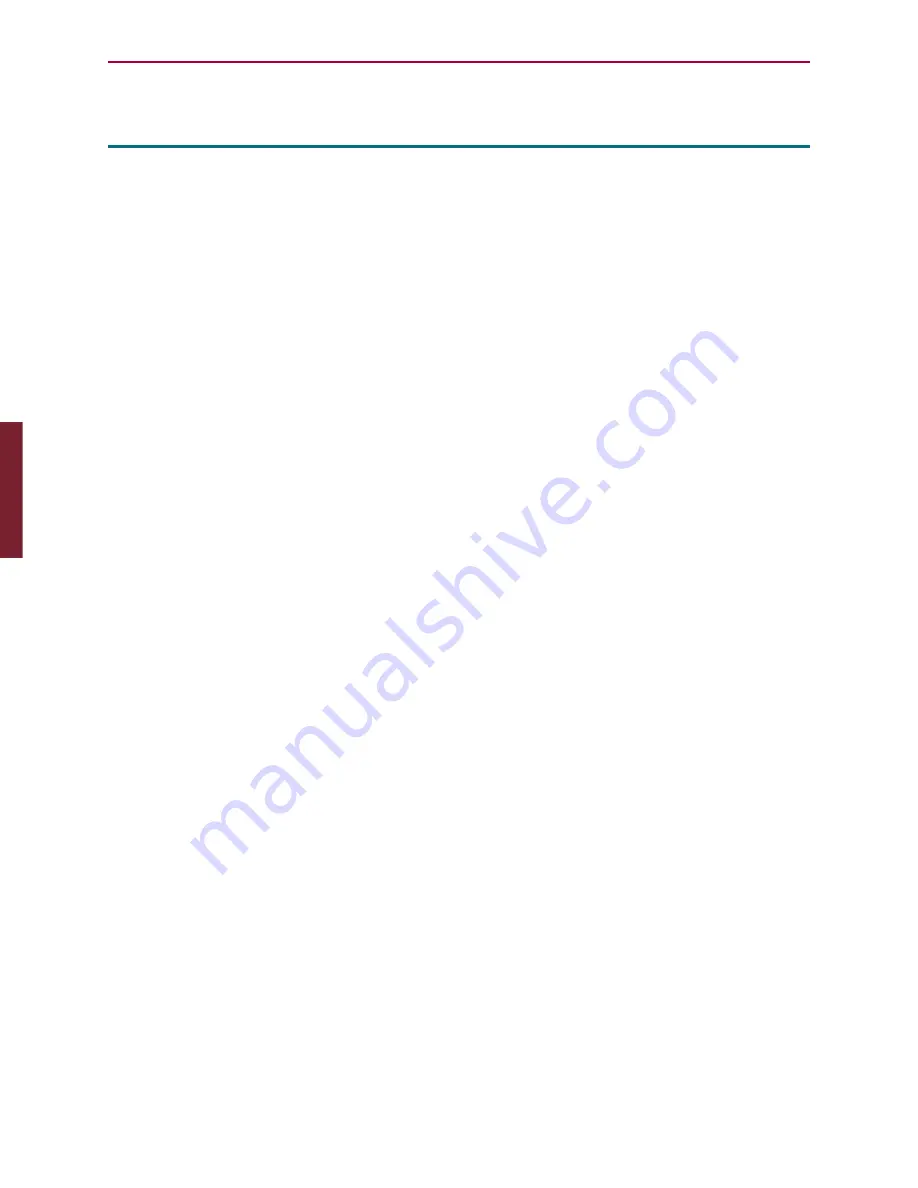
P
ar
t
2: C
omman
d
s
Moog Animatics SmartMotor™ Developer's Guide, Rev. L
Page 623 of 909
PID#
Proportional-Integral-Differential Filter Rate
APPLICATION:
Motion control
DESCRIPTION:
Set PID sample rate to basic rate
EXECUTION:
Next PID update
CONDITIONAL TO:
N/A
LIMITATIONS:
Motor will turn off (freewheel) when this command is issued
READ/REPORT:
N/A
WRITE:
N/A
LANGUAGE ACCESS:
N/A
UNITS:
PID Modulo samples
RANGE OF VALUES:
Valid values: 1, 2 (default), 4 and 8
TYPICAL VALUES:
N/A
DEFAULT VALUE:
PID2
FIRMWARE VERSION:
5.x series only
COMBITRONIC:
N/A
DETAILED DESCRIPTION:
The PID parameter sets the PID sample rate. Valid values are PID1, PID2, PID4 and PID8.
PID2 (8000 samples per second) is the default value. For details on determining the actual
sample rate of your SmartMotor™, see the RSP on page 678.
During each PID sample period, the motor firmware scans and updates the encoder position,
trajectory generator and serial communications ports. It uses position error to perform the
PID calculation to control the servo drive stage. The user program code, if any, is executed
when the microprocessor is not involved in these activities.
Both velocity and acceleration, SRC(2) and SRC(-2), are impacted by the PID setting.
However, there are no effects from the PID setting on CLK and WAIT.
The values of 1, 2, 4 and 8 mean the PID filter will react and update on position error to
correct drive power at different rates (refer to the following table). This does not change how
code is executed, but it does change how much time is given to that execution. As a result, a
program run at PID8 will typically run faster than one run at PID1. However, because the
frequency of PID updates to the drive stage are changed and samples of position error are
done at different intervals, PID8 will result in a more coarse or abrasive motion than PID1.
Therefore, special care should be taken when using the PID command, as improper usage
could result in very sporadic motion.
The current PID rate can be reported through the SAMP command.
Part 2: Commands: PID#
Содержание SmartMotor
Страница 1: ...Developer s Guide Class 5 Later SmartMotor Technology with TM ...
Страница 909: ...PN SC80100003 002 Rev L ...