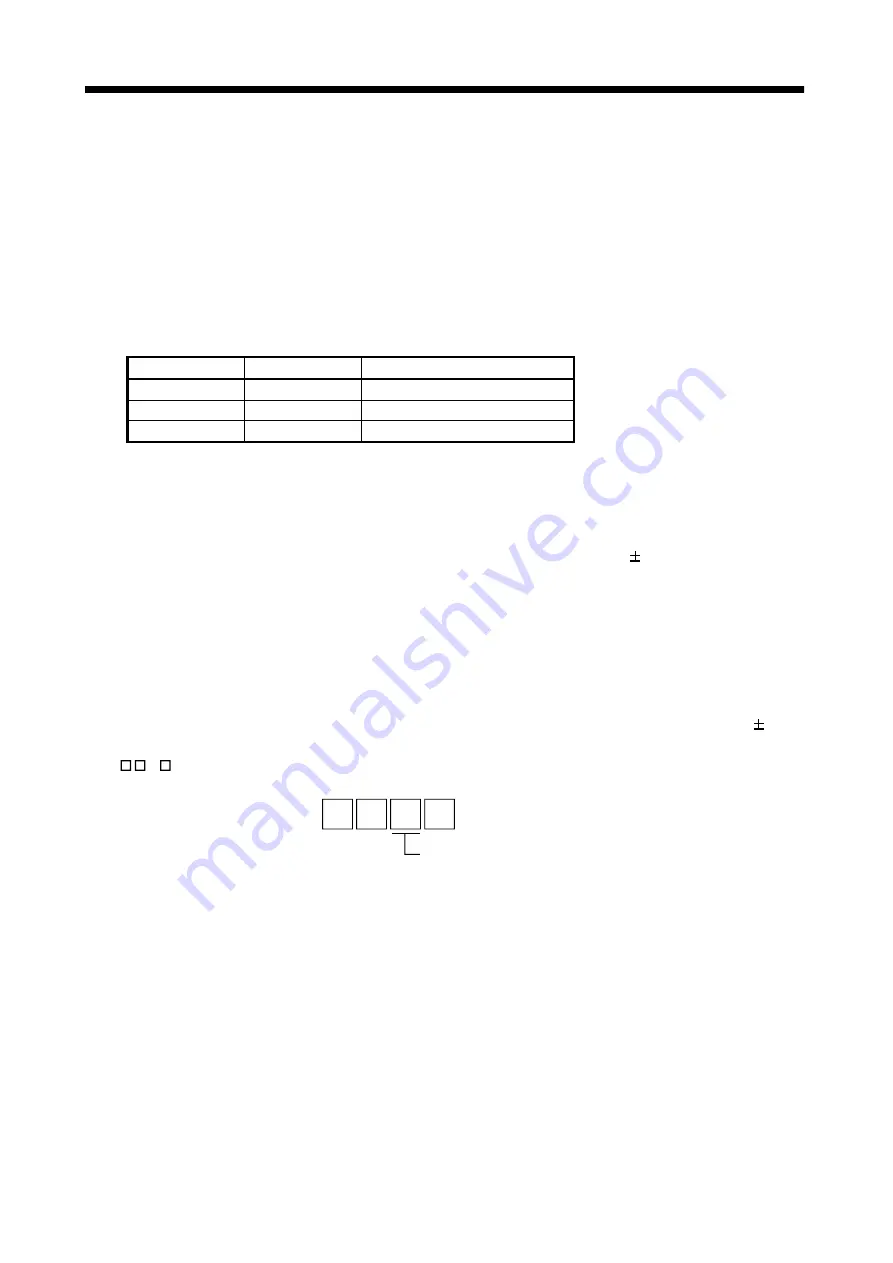
6 - 10
6. ADJUSTMENT
6.4.5 When the same gain is used for two or more axes
(1) Machine condition
To perform interpolation operation with two or more axes of servo amplifiers, the position loop gains of
the axes are set to the same value.
(2) Adjustment procedure
1) To adjust the gains of each axis, adjust the gains of all axes in the adjustment procedures in
Sections 6.4.1 to 6.4.4.
2) Set "0000" or "0002" in parameter No. 8.
"0000": Interpolation control ............ The following parameter values change at the next start/stop.
Parameter No.
Symbol
Name
15
PG2
Position loop gain 2
16
VG2
Speed loop gain 2
17
VIC
Speed integral compensation
"0002": No auto tuning...................... Make auto tuning invalid and set each gain manually.
3) Match position loop gain 1 to the minimum value of each axis to make the gains of all axes equal.
6.5 Slight vibration suppression control
The slight vibration suppression control mode is used to reduce servo-specific 1 pulse vibration at the
time of a stop. This mode produces an effect especially when the ratio of load inertia moment to servo
motor inertia moment is small (2 to 5 times). Note that when vibration is attributable to looseness (such
as gear backlash) or machine resonance, use the notch filter (parameter No. 18).
The slight vibration suppression control mode should be used after real-time auto tuning or manual gain
adjustment.
Usage
First, perform real-time auto tuning or manual gain adjustment so that vibration falls within 2 to 3
pulses.
Set " 1 " in parameter No. 24 to enter the slight vibration suppression mode at the time of a stop.
Slight vibration suppression
control execution
Parameter No. 24
1
Содержание MR-J2-03B5
Страница 11: ...A 10 MEMO ...
Страница 15: ...4 MEMO ...
Страница 21: ...1 6 1 FUNCTIONS AND CONFIGURATION MEMO ...
Страница 27: ...2 6 2 INSTALLATION MEMO ...
Страница 61: ...5 8 5 PARAMETERS MEMO ...
Страница 73: ...7 2 7 INSPECTION MEMO ...
Страница 81: ...8 8 8 TROUBLESHOOTING MEMO ...
Страница 87: ...9 6 9 OUTLINE DIMENSION DRAWINGS MEMO ...
Страница 91: ...10 4 10 CHARACTERISTICS MEMO ...
Страница 111: ...11 20 11 OPTIONS AND AUXILIARY EQUIPMENT MEMO ...