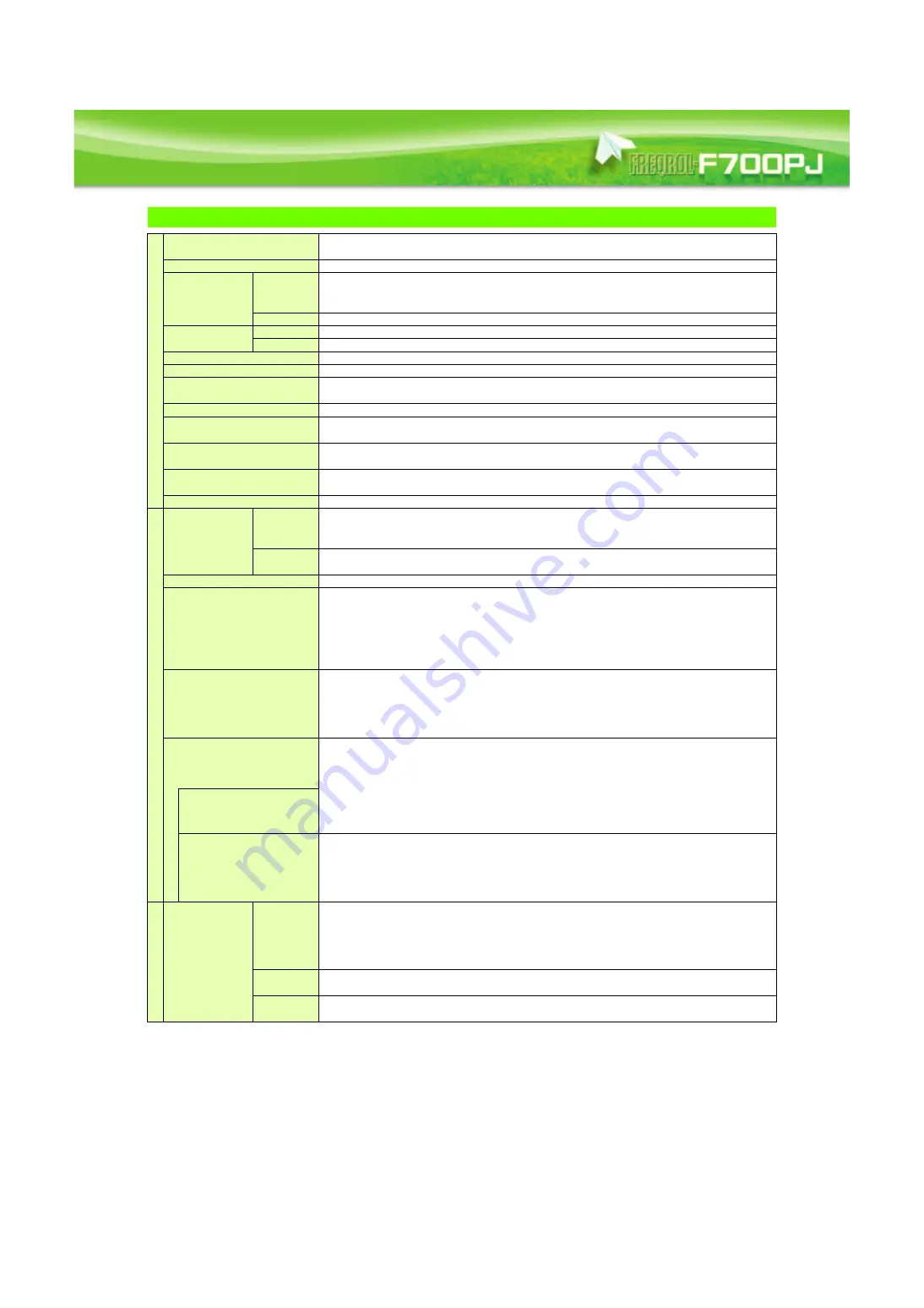
12
Common Specification
Cont
rol s
p
ec
if
ica
ti
o
ns
Control method
High carrier frequency PWM control (V/F control)/Optimum excitation control/General-purpose magnetic flux vector
control/IPM motor control
Output frequency range
0.2 to 400Hz
Frequency setting
resolution
Analog input
0.06Hz/60Hz (terminals 2 and 4: 0 to 10V/10-bit)
0.12Hz/60Hz (terminals 2 and 4: 0 to 5V/9-bit)
0.06Hz/60Hz (terminal 4: 0 to 20mA/10-bit)
Digital input
0.01Hz
Frequency
accuracy
Analog input
Within
1% of the max. output frequency (25°C
10°C)
Digital input
Within 0.01% of the set output frequency
Speed control range
V/F control 1:10, General-purpose magnetic flux vector control (during power driving) 1:60, IPM motor control 1:10
Voltage/frequency characteristics
Base frequency can be set from 0 to 400Hz. Constant-torque/variable-torque pattern can be selected.
Starting torque
General-purpose motor control (General-purpose magnetic flux vector control or slip compensation): 120% (at 1Hz)
IPM motor control: 50%
Torque boost
Manual torque boost
Acceleration/deceleration time
setting
0.1 to 3600s (acceleration and deceleration can be set individually), linear and S-pattern acceleration/deceleration
modes are available.
Regenerative braking torque
General-purpose motor control: 15%
IPM motor control: 5% (10% for 1.5kW or less)
DC injection brake
General-purpose motor control: Operation frequency (0 to 120Hz), operation time (0 to 10s), operation voltage (0 to
30%) can be changed.
Stall prevention operation level
Operation current level can be set (0 to 150% variable). Whether to use the function or not can be set.
O
p
er
at
ion sp
ec
if
icat
ions
Frequency setting
signal
Analog input
Two terminals
Terminal 2: 0 to 10V and 0 to 5V are available
Terminal 4: 0 to 10V, 0 to 5V, and 4 to 20mA are available
Digital input
The signal is entered from the operation panel or parameter unit.
Frequency setting increment can be set.
Start signal
Forward and reverse rotation or start signal automatic self-holding input (3-wire input) can be selected.
Input signal (five terminals)
The following signals can be assigned to
Pr. 178 to Pr.182 (input terminal function selection)
: multi-speed selection,
remote setting, second function selection, terminal 4 input selection, JOG operation selection, PID control valid
terminal, external thermal input, PU-External operation switchover, V/F switchover, output stop, start self-holding
selection, forward rotation, reverse rotation command, inverter reset, PID forward/reverse action switchover, PU-NET
operation switchover, External-NET operation switchover, command source switchover, inverter operation enable
signal, PU operation external interlock, PID integral value reset.
Operational functions
Maximum/minimum frequency setting, frequency jump operation, external thermal relay input selection, automatic
restart after instantaneous power failure operation, forward/reverse rotation prevention, remote setting, second
function, multi-speed operation, regeneration avoidance, slip compensation, operation mode selection, offline auto
tuning function, PID control, computer link operation (RS-485), Optimum excitation control, power failure stop, speed
smoothing control, MODBUS RTU
Output signal
Open collector output (one
terminal)
Relay output (one terminal)
The following signals can be assigned to
Pr.190 and Pr.192 (output terminal function selection)
: inverter operation, up-to-
frequency, overload alarm, output frequency detection, regenerative brake prealarm, electronic thermal relay
function prealarm, inverter operation ready, output current detection, zero current detection, PID lower limit, PID
upper limit, PID forward/reverse rotation output, fan alarm.
, heatsink overheat pre-alarm, deceleration at an
instantaneous power failure, PID control activated, PID deviation limit, IPM motor control
, PID output interruption,
pulse train output of output power, during retry, life alarm, average current value monitor, remote output, alarm
output, fault output, fault output 3, and maintenance timer alarm.
Operating status
For meter
Pulse train output
(MAX 2.4kHz: one terminal)
The following signals can be assigned to
Pr. 54 FM terminal function selection
: output frequency, output current
(steady), output voltage, frequency setting, converter output voltage, regenerative brake duty, electronic thermal
relay function load factor, output current peak value, converter output voltage peak value, reference voltage output,
motor load factor, PID set point, energy saving effect, cumulative energy saving, PID measured value, output power,
PID deviation, motor thermal load factor, and inverter thermal load factor. Pulse train output (1440 pulses/s/full scale)
Indic
at
io
n Operation panel
Parameter unit
(FR-PU07)
Operating
status
The following operating status can be displayed: output frequency, output current (steady), output voltage, frequency
setting, cumulative energization time, actual operation time, converter output voltage, regenerative brake duty,
electronic thermal relay function load factor, output current peak value, converter output voltage peak value, motor
load factor, PID set point, PID measured value, PID deviation, inverter I/O terminal monitor, output power, cumulative
power, motor thermal load factor, inverter thermal load factor, and PTC thermistor resistance.
Fault record
Fault record is displayed when a fault occurs. Past 8 fault definitions (output voltage/current/frequency/
cumulative energization time right before the fault occurs) are stored.
Interactive
guidance
Function (help) for operation guide
Содержание F720PJ-11KF
Страница 88: ...88 MEMO ...