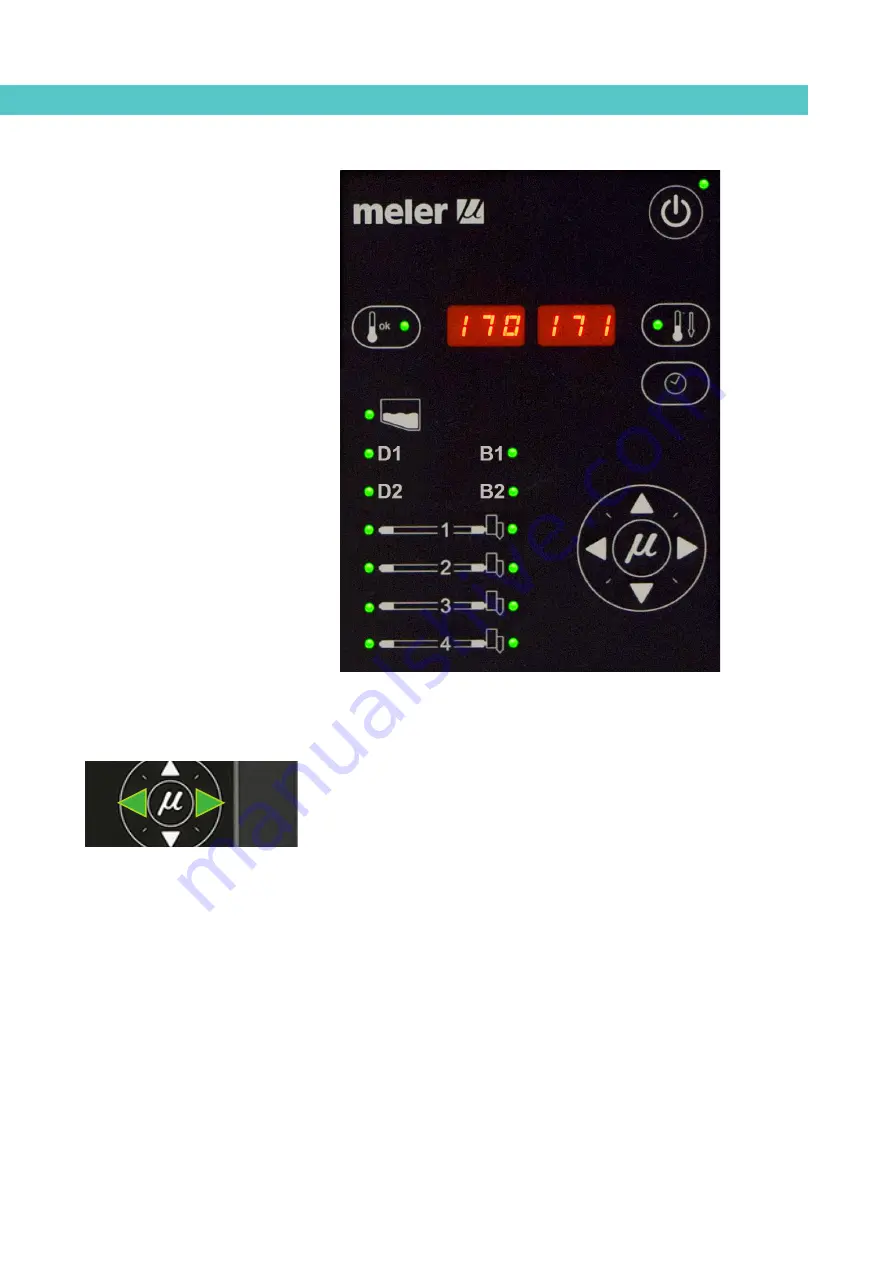
FOCKE MELER GLUING SOLUTIONS, S.A.
4-4
MELTER OPERATION
Displaying the temperature for each component
The temperature may be displayed for each component (premelter, tank,
distributor and each hose and applicator) by selecting the component with the
cursor.
Press the left-right arrow until the desired component is displayed.
After 10 seconds, the display will return to the default component (the tank).
If you wish to keep the component displayed permanently, press and hold the
left-right arrow for 2 seconds while selecting the chosen element.
For units that have one pump installed, the display sequence is the following:
premelter<—tank<—distributor 1<—pump 1<—distributor 2<—pump 2<—
hose 1<—applicator 1<—...<—hose 4<—applicator 4
premelter—>tank—>distributor 1—>pump 1—>distributor 2—>pump 2—>
hose 1—>applicator 1—>...—>hose 4—>applicator 4
To remove a component from permanent display, simply press either of the
left-right arrows.
Содержание MACRO FOAM Series
Страница 1: ...MA 5127 ENG 231220 GLUING SOLUTIONS ADHESIVE MELTER MACRO FOAM SERIES INSTRUCTIONS MANUAL ...
Страница 8: ...FOCKE MELER GLUING SOLUTIONS TABLE OF CONTENTS This page is intentionally left blank ...
Страница 34: ...FOCKE MELER GLUING SOLUTIONS S A 3 14 INSTALLATION This page is intentionally left blank ...
Страница 75: ...ELECTRICAL DRAWINGS 7 1 MA 5127 ENG MACRO FOAM SERIES MELTER MANUAL 7 ELECTRICAL DRAWINGS ...
Страница 76: ...FOCKE MELER GLUING SOLUTIONS S A 7 2 ELECTRICAL DRAWINGS This page is intentionally left blank ...
Страница 78: ...FOCKE MELER GLUING SOLUTIONS S A 8 2 PNEUMATIC DIAGRAMS This page is intentionally left blank ...