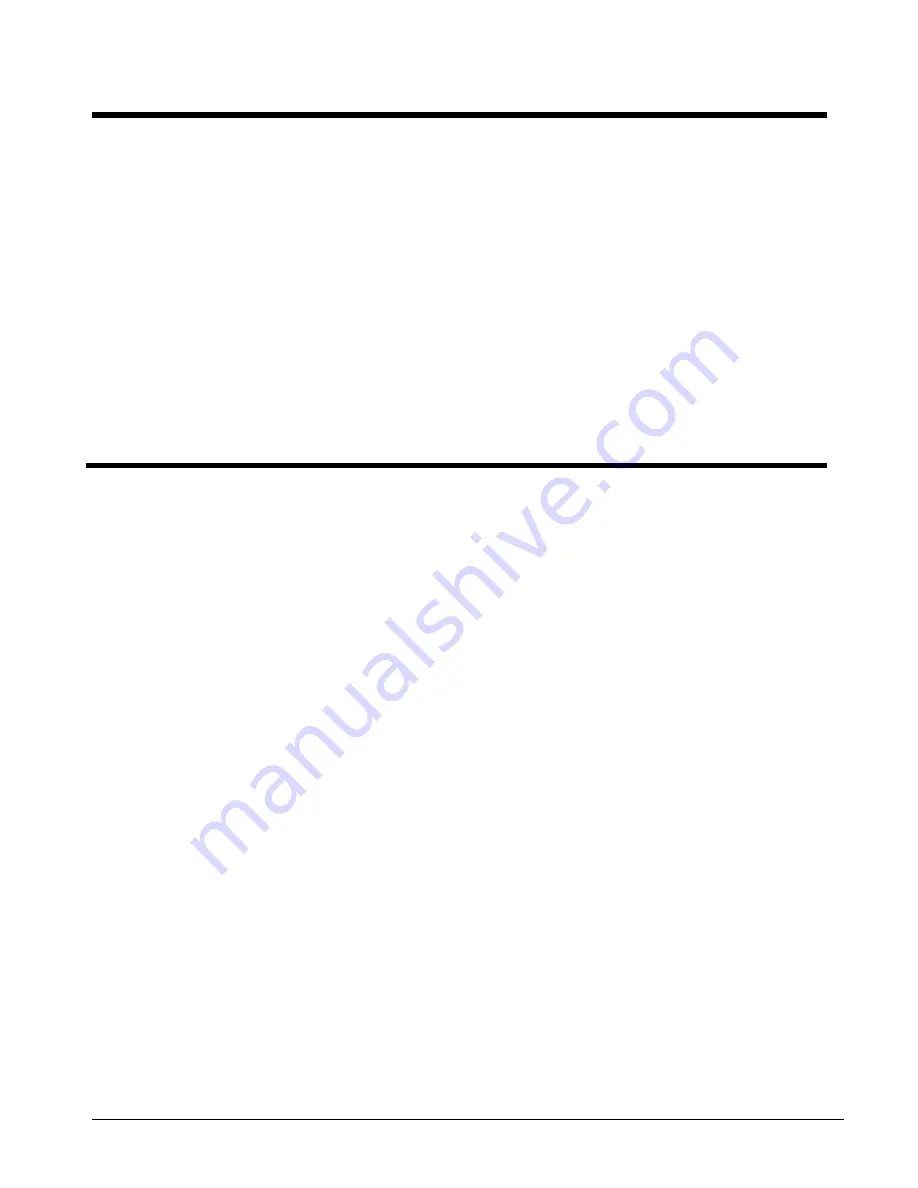
74
OMM 1008-1
BAS Interface
The MicroTech II controller is available with the optional Open Choices
feature, an exclusive McQuay
feature that provides easy integration with a building automation system (BAS). If the unit will be tied into a
BAS, the controller should have been purchased with the correct factory-installed communication module.
The modules can also be added in the field during or after installation.
If an interface module was ordered, one of the following BAS interface installation manuals was shipped with
the unit. Contact your local McQuay sales office for a replacement, if necessary.
•
IM 735, L
ON
W
ORKS
Communication Module Installation
•
IM 736, BACnet
Communication Module Installation
•
IM 743, Modbus
Communication Module Installation
Connection to Chiller
Connection to the chiller for all BAS protocols will be at the unit controller. An interface card will have to
be installed in the unit controller depending on the protocol being used.
Sequence of Operation
Start-up Sequence
“Next On” Status
If none of the “OFF” conditions are true, then all the MicroTech II compressor controls in a network of up to 2
units (four compressors) will pole the status of each to determine the one having “Next On” status, which is
usually the compressor with the least starts. This takes about one minute.
Evap (Evaporator) Pump Start
Once this is determined, the unit controller of the chiller with the “Next On” compressor (when there are two
chillers) will start the evaporator pump and determine if there is load based on the water temperature. This is
determined if the leaving evaporator water is above the “LWT Setpoint” plus “Startup Delta T”. If there is no
load, based on the temperature, the unit is in the state of ‘Awaiting Load’.
Interlock On
If there is load, the unit waits for the Evaporator Recirculation Timer period (default value of 30 seconds) and
starts the Interlock Timer for 10 seconds.
Cond (Condenser) Pump Start
After Interlock is confirmed, the controller starts the Condenser Pump and checks for condenser flow before
starting the first compressor.
Lead Compressor Start
When the Lead compressor starts, the 02S code will instruct the compressor to position the Internal Guide
Vanes (IGV) at 45% and the start speed will be set to 50% of the Minimum and Maximum RPM settings for
the lead compressor, or 11,000 RPMs which ever is greater. The Min and Max RPMs come from the actual
compressor, and are influenced
by the water temperatures at the chiller.
As the lead compressor achieves the Start Speed minus one thousand RPM, the compressor will attempt to
hold this speed until the IGVs have opened completely. As the RLA exceeds 14% (indicating that the check
value has opened), the Start Speed is reduced to the minimum speed set by the compressor. Achieving start
speed allows the DTC compressor to switch from its internal start control to follow the Modbus Demand
value sent from the MicroTech II controller.