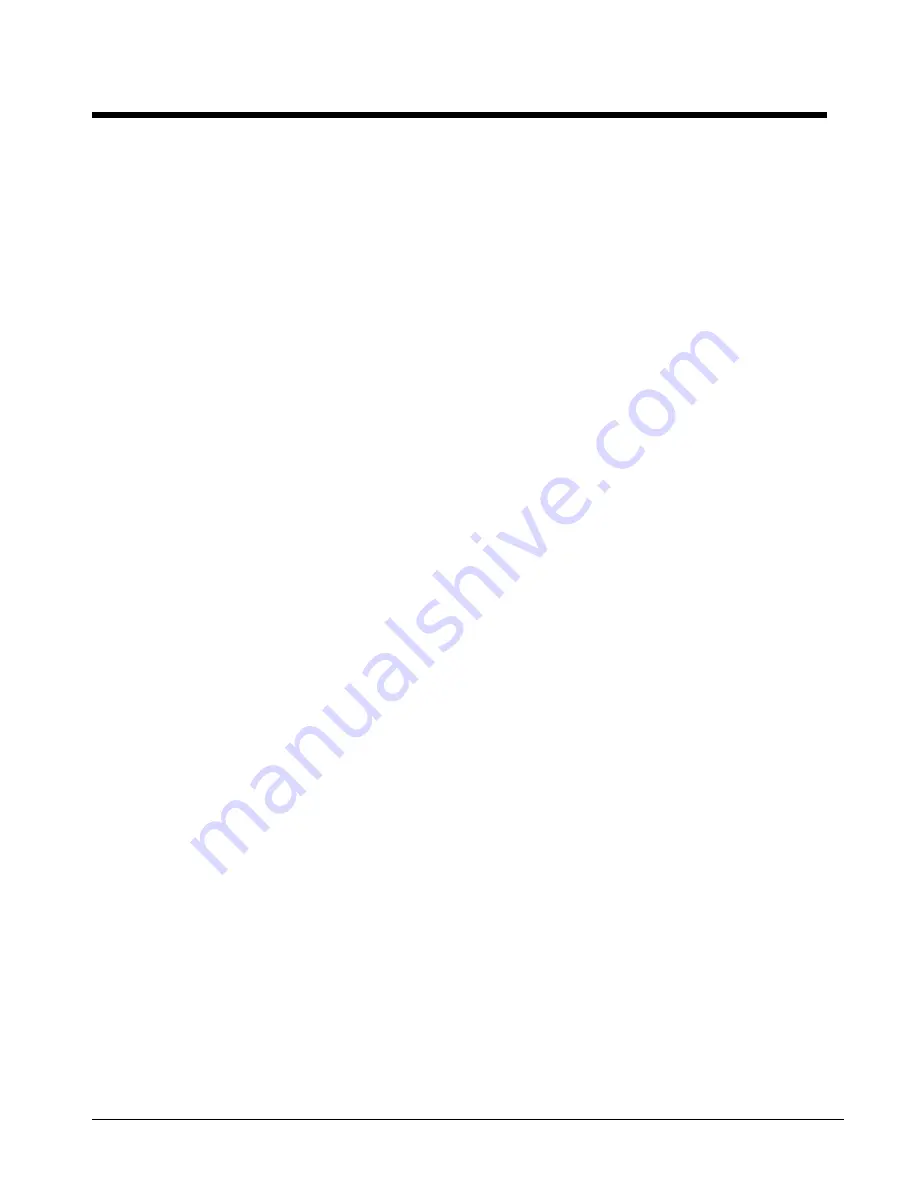
4
OMM 1008-1
Features of the Control Panel
•
Control of leaving chilled water within a
±
0.2°F (
±
0.1°C) tolerance.
•
Display of the following temperatures and pressures on a 15-inch Super VGA touch-screen operator
interface
•
Entering and leaving chilled water temperature
•
Enter and leaving condenser water temperature
•
Saturated evaporator refrigerant temperature and pressure
•
Saturated condenser temperature and pressure
•
Outside air temperature (optional)
•
Suction line, liquid line and discharge line temperatures, calculated superheat for discharge and
suction lines, and calculated sub-cooling for liquid line
•
Automatic control of primary and standby evaporator and condenser pumps.
•
Control of up to 4 stages of cooling tower fans plus modulating bypass valve and/or tower fan VFD.
Although fan staging is available, continuous, modulated control of tower capacity is preferred and
recommended.
•
History trend feature that will constantly log chiller functions and setpoints. The controller will store and
display all accumulated data for recall in a graphic format on the screen. Data can be downloaded for
archival purposes.
•
Three levels of security protection against unauthorized changing of setpoints and other control
parameters.
•
Plain language warning and fault diagnostics to inform operators of most warning or fault conditions.
Warnings, problems and faults are time and date stamped for identification of when the fault condition
occurred. In addition, the operating conditions that existed just prior to shutdown can be recalled to aid
in resolving the cause of the problem.
•
Twenty-five previous faults and related operating conditions are available from the display. Data can be
exported for archival purposes via a 3.5-inch floppy drive or other device (depending on date of
manufacture).
•
Soft loading feature reduces electrical consumption and peak demand charges during system loop pull-
down.
•
Remote input signals for chilled water reset, demand limiting and unit enable.
•
Manual control mode allows the service technician to command the unit to different operating states.
Useful for system checkout.
•
BAS communication capability via L
ON
T
ALK
, Modbus
or BACnet
standard open protocols for most
BAS manufacturers.
•
Service Test mode for troubleshooting controller outputs.
•
Pressure transducers for direct reading of system pressures.
•
Preemptive control of low evaporator and high discharge pressure conditions to take corrective action
prior to a fault trip.