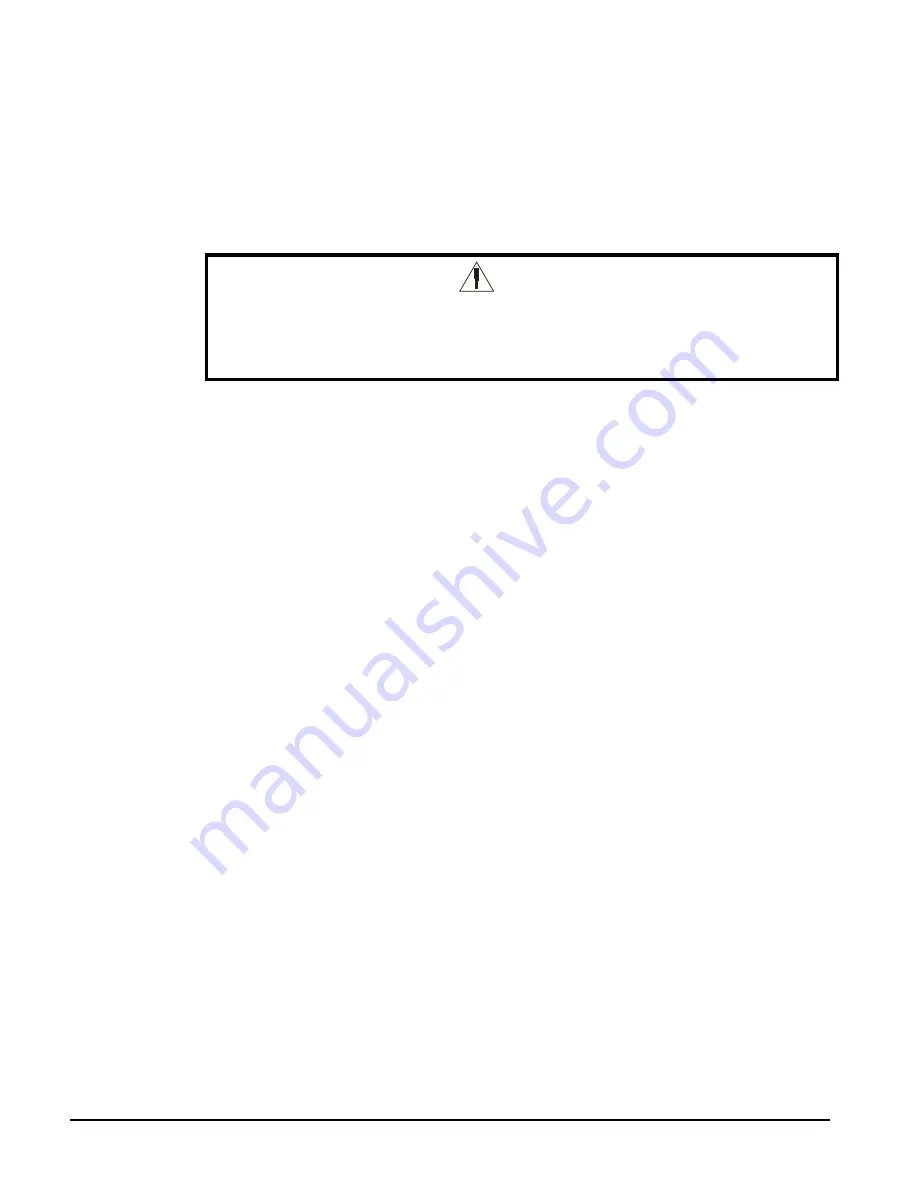
34
AGZ 035A through 065A
IOMM AGZ-3
Filter Driers
Each refrigerant circuit is furnished with a full flow filter drier or an optional replaceable core type
filter-drier. The core assembly of the replaceable core drier consists of a filter core held tightly in the
shell in a manner that allows full flow without bypass.
Pressure drop across the filter drier at full load conditions must not exceed 10 psig at full load. See
Table 53 for pressure drop at other load points. Replace the filter drier if the pressure drop exceeds
maximum.
WARNING
Pump out refrigerant before removing end flange for replacement of core(s)
to remove liquid refrigerant and lower pressure to prevent accidental blow off
of cover.
A condenser liquid line service valve is provided for isolating the charge in the condenser, but also
serves as the point from which the liquid line can be pumped out. With the line free of liquid, the
filter-drier core(s) can be easily replaced.
System Adjustment
To maintain peak performance at full load operation, the system superheat and liquid subcooling may
require adjustment. Read the following subsections closely to determine if adjustment is required.
Liquid Sightglass and Moisture Indicator
The color of the moisture indicator is an indication of the dryness of the system and is extremely
important when the system has been serviced. Immediately after the system has been opened for
service, the element may indicate a wet condition. It is recommended that the equipment operate for
about 12 hours to allow the system to reach equilibrium before deciding if the system requires a
change of drier cores.
Bubbles in the sightglass at constant full load indicates a shortage of refrigerant, a plugged filter-drier,
or a restriction in the liquid line. However, it is not unusual to see bubbles in the sightglass during
changing load conditions.
Refrigerant Charging
Liquid line subcooling at the liquid shut-off valve should be between 15 and 20 degrees F at full load.
If the unit is at steady full load operation and bubbles are visible in the sightglass, then check liquid
subcooling.
Thermostatic Expansion Valve
The expansion valve performs one specific function. It keeps the evaporator supplied with the proper
amount of refrigerant to satisfy the load conditions.
The sensing bulb of the expansion valve is installed in the closest straight run of suction line from the
evaporator. The bulb is held on by clamps around the suction line and is insulated to reduce the effect
of surrounding ambient temperatures. In case the bulb must be removed, simply slit the insulation on
each side of the bulb, remove the clamps and then remove the capillary tubing that runs along the
suction line from the valve.
The power element is removable from the valve body without removing the valve from the line.
Содержание AGZ 035A
Страница 6: ...6 AGZ 035A through 065A IOMM AGZ 3 Figure 3 Clearance Requirements...
Страница 18: ...18 AGZ 035A through 065A IOMM AGZ 3 Electrical Legend Figure 8 Electrical Legend...
Страница 19: ...IOMM AGZ 3 AGZ 035A through 065A 19 Figure 9 Typical Field Wiring with Global UNT Controller...
Страница 20: ...20 AGZ 035A through 065A IOMM AGZ 3 Figure 10 Typical Field Wiring Diagram with MicroTech Controller...
Страница 21: ...IOMM AGZ 3 AGZ 035A through 065A 21 Figure 11 Single point Connection with FanTrol...
Страница 22: ...22 AGZ 035A through 065A IOMM AGZ 3 Figure 12 Single point Connection with SpeedTrol...
Страница 23: ...IOMM AGZ 3 AGZ 035A through 065A 23 Figure 13 Unit Control Schematic UNT...
Страница 24: ...24 AGZ 035A through 065A IOMM AGZ 3 Figure 14 Staging Schematic UNT...
Страница 25: ...IOMM AGZ 3 AGZ 035A through 065A 25 Figure 15 MicroTech Controller Schematic...
Страница 26: ...26 AGZ 035A through 065A IOMM AGZ 3 Figure 16 Unit Control Schematic MicroTech...
Страница 27: ...IOMM AGZ 3 AGZ 035A through 065A 27 Figure 17 Staging Schematic MicroTech...
Страница 94: ...94 AGZ 035A through 065A IOMM AGZ 3 Notes...
Страница 95: ......