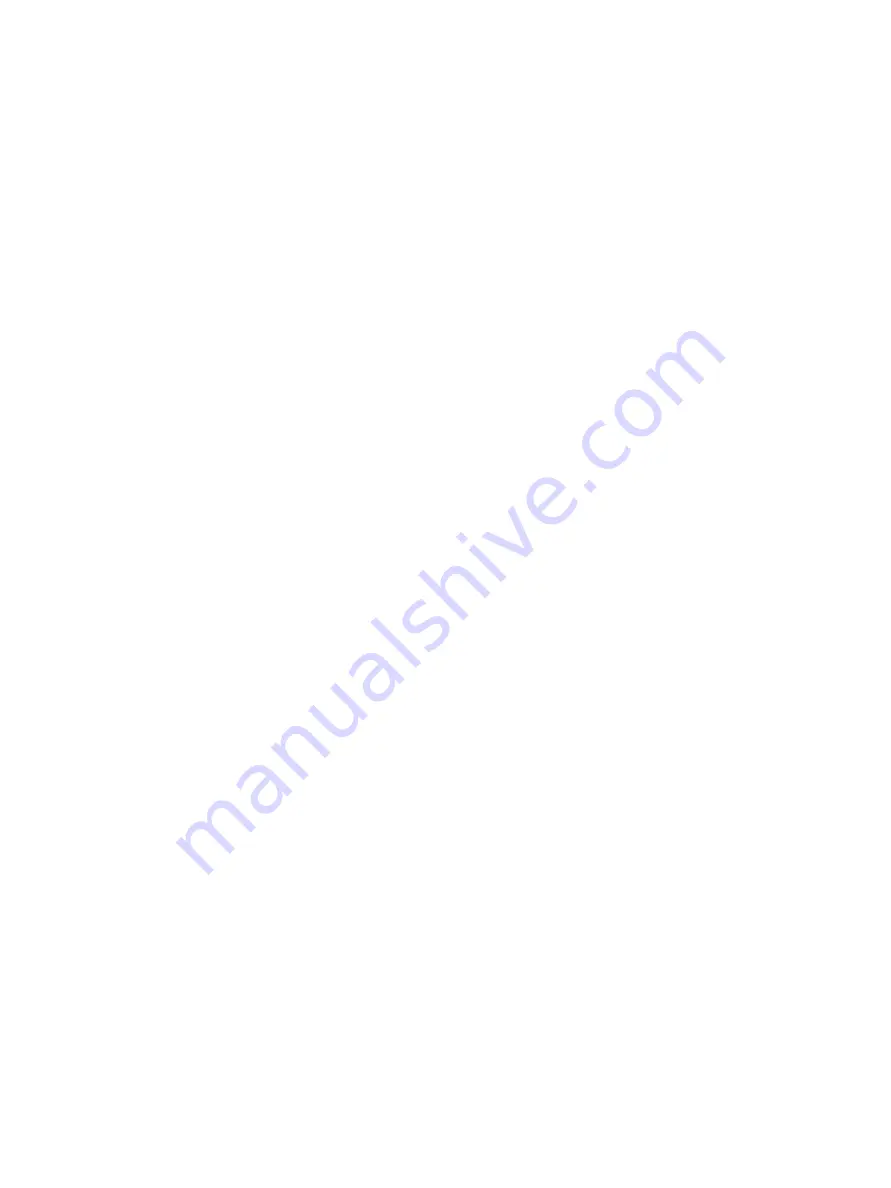
© 2017 Baker Hughes, a GE company, LLC. All rights reserved.
Masoneilan SVI II ESD Installation and Maintenance Manual
=
|
205
Appendix F. Air Supply Requirements
A high quality air supply greatly improves the quality of control and reduces maintenance costs
of pneumatic equipment. See
ANSISA-7.0.01-1996 - Quality Standard for Instrument Air
. Air
supply failure requires special attention to minimize process effects. All process equipment
should be designed and applied to fail to a safe condition. This includes failure of the air supply.
SVI II ESD is designed to fail to a condition of low or no air pressure. Choose control valve
actuators to move the valve to a safe condition when air pressure is low or absent. For example,
a valve supplying fuel to a combustion process is normally equipped with an Air to Open valve. In
other words, the fuel flow is shut off if air fails.
Additional process precautions can be taken. When the air supply recovers, the setpoint to the
valve must be at a value that continues to hold the valve in its safe condition, or to move it to a
known safe condition. To do so, the control system sending the control valve position setpoint is
put into Manual mode and set to 0%. After the air supply has stabilized at its correct pressure,
the setpoint is moved to its operation point in accordance with the plant’s safe start-up
procedures. An additional precaution required on critical processes with an ATO control valve is
to install a shut-off valve that supplements the control valve by moving to a safe condition on air
failure, and remains in that condition until all necessary requirements for safe start-up have
been met.
Содержание SVI II ESD
Страница 4: ...This page intentionally left blank ...
Страница 10: ...This page intentionally left blank ...
Страница 14: ...This page intentionally left blank ...
Страница 100: ...This page intentionally left blank ...
Страница 120: ...This page intentionally left blank ...
Страница 126: ...This page intentionally left blank ...
Страница 160: ...This page intentionally left blank ...
Страница 194: ...This page intentionally left blank ...
Страница 200: ...This page intentionally left blank ...
Страница 204: ...This page intentionally left blank ...
Страница 206: ...This page intentionally left blank ...
Страница 208: ...This page intentionally left blank ...
Страница 216: ...This page intentionally left blank ...