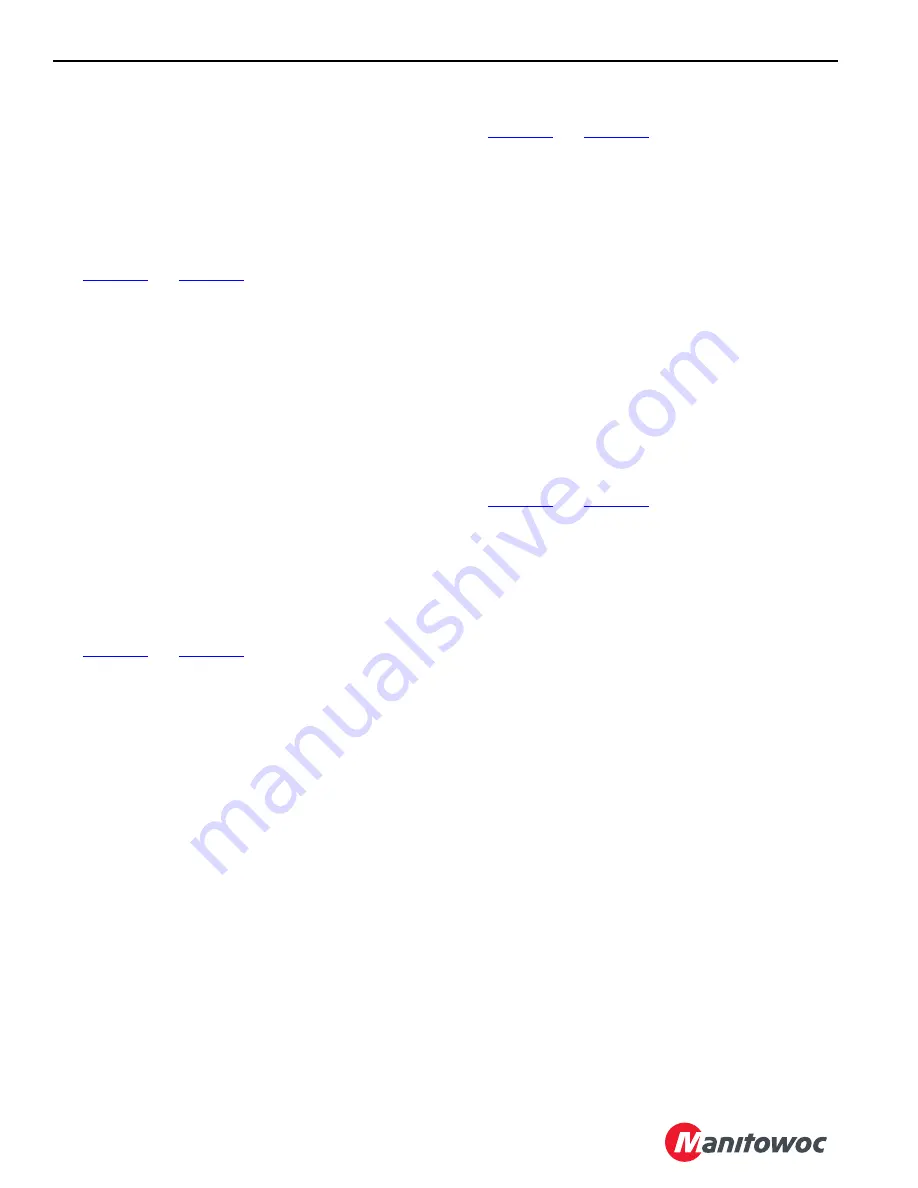
Reference
Only
UNDERCARRIAGE
MLC650 SERVICE/MAINTENANCE MANUAL
8-2
Published 09-09-16, Control # 229-09
Travel Speed Selection
The travel speed switch, located on the right console,
provides low-speed and high-speed travel selections. Travel
speed is dependent on the position of the travel speed switch
and the position of the crawler control handle. The control
algorithm determines the pump and motor flows needed to
achieve either a high or low travel speed.
Low Travel Speed
for the following information.
The SCM-00 control module sends a 24 VDC output to the
travel speed switch. When the switch is in the LOW speed
position, the switch is open, sending a 0 VDC signal back to
the SCM-00 control module. The SCM-00 control module
communicates the low-speed command to the CCM-10
control module via the CAN Bus.
The CCM-10 control module then sends a corresponding
signal to the IOSB22 control module via the CAN Bus. The
IOSB22 control module then decreases the pulse width
modulation (PWM) duty cycle to the travel motor control
solenoids. The decreased PWM duty cycle increases the
angle of the motor swashplate, causing the motor speed to
decrease. Motor displacement goes to maximum.
When in low-speed travel mode, the travel motors are kept at
maximum displacement and any variation in travel speed is
done by varying the PWM duty cycle to the pump control
solenoids.
High Travel Speed
for the following information.
When the travel speed switch is in the HIGH speed position,
the switch is closed, sending a 24 VDC signal back to the
SCM-00 control module. The SCM-00 control module
communicates the high-speed command to the CCM-10
control module via the CAN Bus.
The CCM-10 control module then sends a corresponding
signal to the IOLC32 and IOSB22 control modules via the
CAN Bus. The control algorithm commands the IOLC32 and
IOSB22 control modules to drive the travel pumps and
motors at a higher rate of speed relative to the movement of
the travel control handles.
When in high-speed travel mode, the IOSB22 control module
varies the PWM duty cycle to the travel motor control
solenoids as commanded by the control algorithm.
Increasing the PWM duty cycle decreases the angle of the
motor swashplate, causing the motor speed to increase.
NOTE:
When the load on the travel circuit increases, the
control algorithm decreases the PWM signal to the
motors. This causes the angle of each motor’s
swashplate to increase, which increases motor
displacement. The motors rotate at a slower speed,
but with more torque.
Travel Operation
for the following information.
To enable the control system, the switches listed below must
be in the stated positions:
•
Seat safety switch closed
•
Travel park switch in the UN-PARK position
In the default state, the left travel / drum 1 diverter solenoid
valve and the right travel / drum 2 diverter solenoid valve,
located in the accessory valve manifold, are de-energized.
With the left travel / drum 1 diverter solenoid valve de-
energized, the left travel/ drum 1 diverter pilot valve is kept in
the default position and hydraulic fluid from pump 3 is routed
to the left travel motors.
With the right travel / drum 2 diverter solenoid valve de-
energized, the right travel/ drum 2 diverter pilot valve is kept
in the default position and hydraulic fluid from pump 4 is
routed to the right travel motors.
Left Forward Travel Control
for the following information.
When the left travel control handle (J2 joystick) is moved to
the forward position, the J2 joystick communicates the travel
command to the CCM-10 control module via the CAN Bus.
If equipped with the optional travel pedals, moving the left
pedal to the forward travel position sends a corresponding
analog signal to the SCM-00 control module. The SCM-00
control module then communicates the travel command to
the CCM-10 control module via the CAN Bus.
When the CCM-10 control module receives the left forward
travel command, it sends a corresponding signal to the
IOLC32 and IOSB22 control modules via the CAN Bus.
The IOLC32 then begins to ramp up the PWM duty cycle to
the B-side solenoid of the pump 3 electronic displacement
control (EDC). The PWM signal is in proportion to the speed
commanded by the travel control handle. Increasing the
PWM duty cycle increases the pump swashplate angle,
which increases the hydraulic flow from the B-side of the
pump.
From the pump, the flow is routed through the left travel/
drum 1 diverter pilot valve and then into the B-side of the left
travel motors. If high-speed travel mode is selected, the
IOSB22 control module ramps up the PWM duty cycle to the
left travel motors control solenoids to increase the motor
speed until the commanded travel speed is achieved.
The left motor speed sensor and pump 3 pressure
transducer (left track psi) provide the closed loop feedback to
the control modules. The control algorithm uses this
feedback to adjust pump and motor flows to maintain the
commanded travel speed.
Содержание MLC650
Страница 1: ...R e f e r e n c e O n l y Service Maintenance Manual Manitowoc MLC650 ...
Страница 2: ...R e f e r e n c e O n l y ...
Страница 4: ...R e f e r e n c e O n l y THE ORIGINAL LANGUAGE OF THIS PUBLICATION IS ENGLISH ...
Страница 375: ...R e f e r e n c e O n l y ...
Страница 376: ...R e f e r e n c e O n l y ...