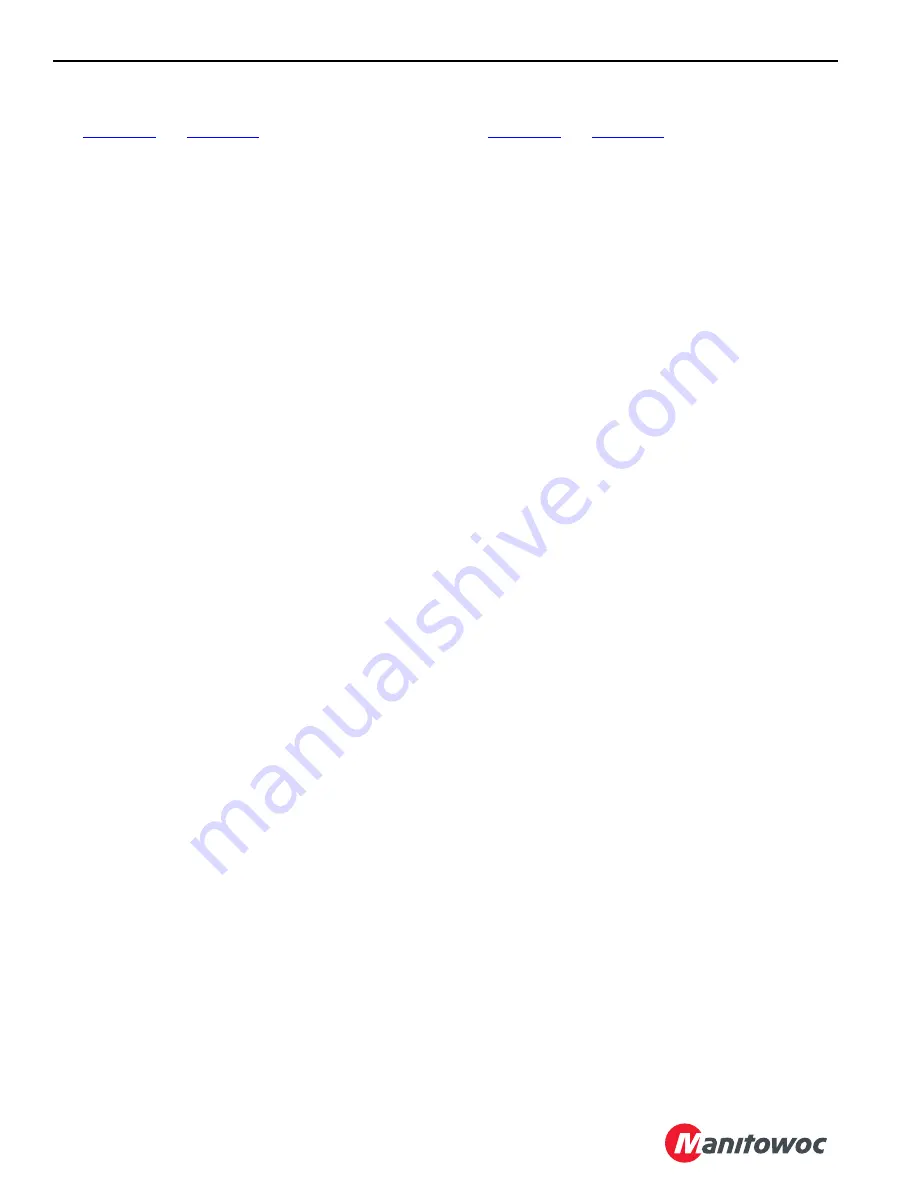
Reference
Only
HOISTS
MLC650 SERVICE/MAINTENANCE MANUAL
5-20
Published 09-09-16, Control # 229-09
Drum 3 Hoisting Operation
for the following.
To enable the control system to drive the drum 3 pump and
motor, the switches listed below must be in the stated
positions:
•
Seat safety switch closed
•
Drum 3 park switch in the OFF position
NOTE:
For the following operation, the drum 2 park switch
and/or right travel park switch are in the ON
position.
During the drum 3 operation, the CCM-10 energizes the
drum 2/drum 3 selector solenoid valve (14), located in the
accessory valve manifold (1). When energized, the solenoid
valve routes hydraulic fluid to the pilot control of the drum 2/
drum 3 diverter valve (4). The diverter valve shifts position,
allowing main hydraulic fluid from pump 2 to flow to the drum
3 hydraulic motor (7).
Hydraulic fluid from the drum 2/drum 3 selector solenoid
valve also flows to the pilot control of the pump 2 charge
pressure diverter valve (2), causing the valve to shift. When
in this position, charge pressure from pump 2 is present at
the charge pressure check valve (5).
If the main pump pressure drops to less than 0,35 bar (5 psi)
of the charge pressure, the check valve opens, allowing
charge pressure fluid from pump 2 to flow to the drum 3
hydraulic motor.
When the designated drum 3 joystick is moved to the
hoisting position, the CCM-10 control module sends a signal
to the IOLC32 control module via the controller area network
bus (CAN Bus) to ramp up the pulse-width modulation
(PWM) duty cycle to the A-side solenoid of pump 2 electronic
displacement control (EDC). The PWM signal is in proportion
to the speed commanded by the joystick. Increasing the
PWM duty cycle increases the pump swashplate angle,
which increases the hydraulic flow from the A-side of the
pump. From the pump, the hydraulic flow is routed through
the drum 2/drum 3 diverter valve (4), and then into the A-side
of the drum 3 hydraulic motor (7).
The CCM-10 control module sends a signal to the IOLC30
control module via the CAN Bus to ramp up the PWM duty
cycle to the drum 3 motor control solenoid. Increasing the
PWM duty cycle decreases the swashplate angle in each
motor, which increases the motor speed until the rotational
speed is maximized based on the pump flow
The drum 3 motor speed sensor and pump 2 pressure
transducer (drum 3 psi) (3) provide closed loop feedback to
the control modules. The control algorithm uses this
feedback to adjust the pump and motor flows while ramping
up to, and maintaining, the speed commanded by the
joystick input.
Drum 3 Lowering Operation
for the following.
To enable the control system to drive the drum 3 pump and
motor, the switches listed below must be in the stated
positions:
•
Seat safety switch closed
•
Drum 3 park switch in the OFF position
NOTE:
For the following operation, the drum 2 park switch
and/or right travel park switch are in the ON
position.
During the drum 3 operation, the CCM-10 energizes the
drum 2/drum 3 selector solenoid valve (14), located in the
accessory valve manifold (1). When energized, the solenoid
valve routes hydraulic fluid to the pilot control of the drum 2/
drum 3 diverter valve (4). The diverter valve shifts position,
allowing main hydraulic fluid from pump 2 to flow to the drum
3 hydraulic motor (7).
Hydraulic fluid from the drum 2/drum 3 selector solenoid
valve also flows to the pilot control of the pump 2 charge
pressure diverter valve (2), causing the valve to shift. When
in this position, charge pressure from pump 2 is present at
the charge pressure check valve (5).
If the main pump pressure drops to less than 0,35 bar (5 psi)
of the charge pressure, the check valve opens, allowing
charge pressure fluid from pump 2 to flow to the drum 3
hydraulic motor.
When the designated drum 3 joystick is moved to the
lowering position, the CCM-10 control module sends a signal
to the IOLC32 control module via the CAN Bus to ramp up
the PWM duty cycle to the B-side solenoid of pump 2 EDC.
The PWM signal is in proportion to the speed commanded by
the joystick. Increasing the PWM duty cycle increases the
pump swashplate angle, which increases the hydraulic flow
from the B-side of the pump. From the pump, the hydraulic
flow is routed through the drum 2/drum 3 diverter valve (4),
and then into the B-side of the drum 3 hydraulic motor (7).
The CCM-10 control module sends a signal to the IOLC30
control module via the CAN Bus to ramp up the PWM duty
cycle to the drum 3 motor control solenoid. Increasing the
PWM duty cycle decreases the swashplate angle in each
motor, which increases the motor speed until the rotational
speed is maximized based on the pump flow.
The drum 3 motor speed sensor and pump 2 pressure
transducer (drum 3 psi) (3) provide closed loop feedback to
the control modules. The control algorithm uses this
feedback to adjust the pump and motor flows while ramping
up to, and maintaining, the speed commanded by the
joystick input.
Содержание MLC650
Страница 1: ...R e f e r e n c e O n l y Service Maintenance Manual Manitowoc MLC650 ...
Страница 2: ...R e f e r e n c e O n l y ...
Страница 4: ...R e f e r e n c e O n l y THE ORIGINAL LANGUAGE OF THIS PUBLICATION IS ENGLISH ...
Страница 375: ...R e f e r e n c e O n l y ...
Страница 376: ...R e f e r e n c e O n l y ...