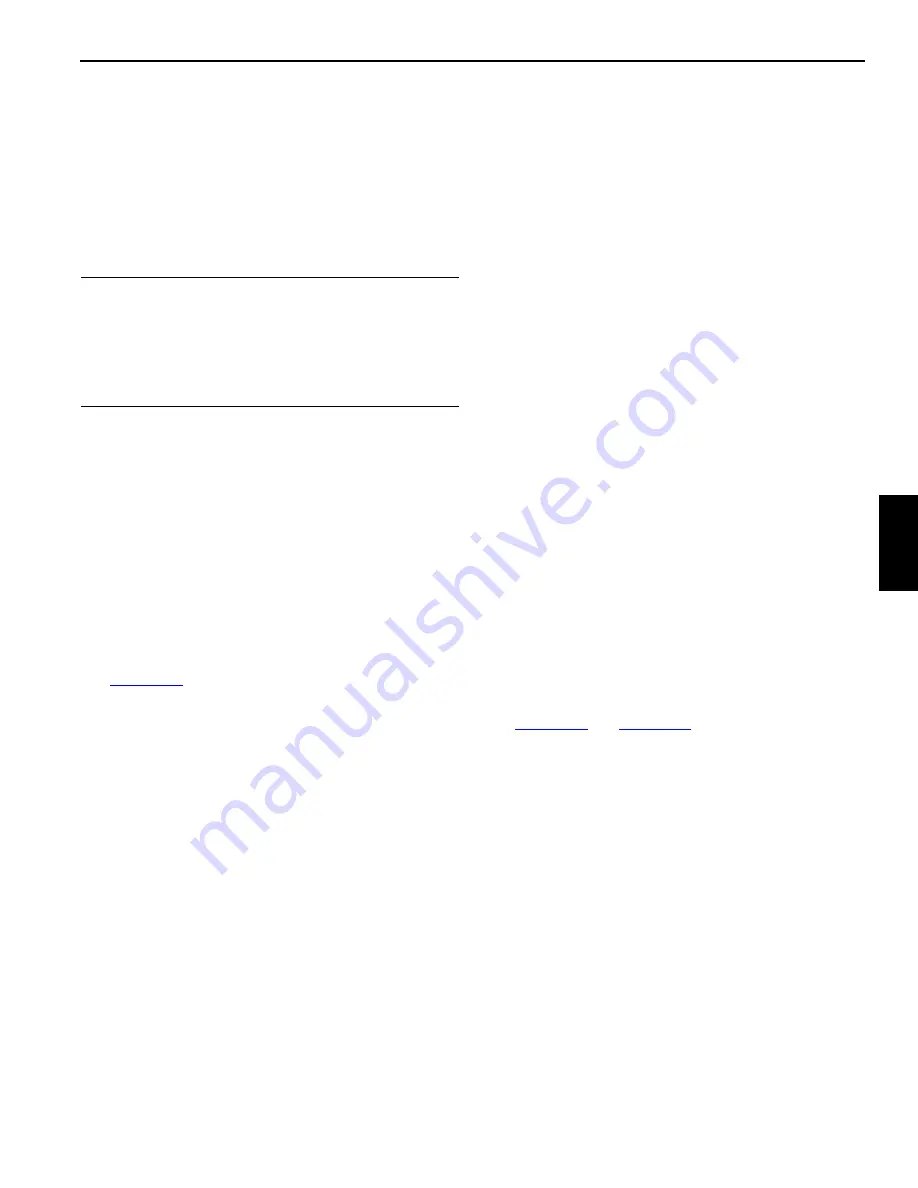
Reference
Only
Manitowoc
Published 09-09-16, Control # 229-09
5-19
MLC650 SERVICE/MAINTENANCE MANUAL
HOISTS
5
55
DRUM 3 WHIP HOIST
Drum 3 Brake Overview
A brake is attached to the drum motors, with the brake discs
attached to the drum shaft. The brakes are controlled by
joystick movement and the drum park brake switch. The
brakes are applied by spring force and released by hydraulic
pressure.
The brakes must be fully released to allow the drum to rotate
for hoisting and lowering operations. To accomplish this, the
brake pressure must be above 10,5 bar (153 psi). Any
pressure below this could cause the brakes to remain
partially applied, which could damage the drum brake
system.
If brake hydraulic pressure or electrical control is lost, the
brake is applied by spring force.
Hydraulic flow to the drum 3 brake release solenoid valve is
provided by the main and charge pressure hydraulic flow
from pump 2.
Drum 3 Brake Operation
for the following.
The J2 joystick sends a 24 V
DC
output to the drum 3 park
switch. The park switch is closed in the UN-PARK position,
causing the switch to send a 24 V
DC
signal back to the J2
joystick. The J2 joystick communicates the un-park brake
command to the IOLC30 control module via the controller
area network bus (CAN Bus).
During drum 3 operation, the CCM-10 control module
energizes the drum 2/drum 3 selector solenoid valve (14),
located in the accessory valve manifold (1).
When energized, the solenoid valve routes hydraulic fluid to
the pilot controls of the drum 2/drum 3 diverter valve (4) and
the pump 2 charge pressure diverter valve (2). The diverter
valves shift position, allowing the pump 2 main hydraulic
pressure to be present at the brake release solenoid valve
(12) and the pump 2 charge pressure present at the charge
pressure check valve (5).
If the main pump pressure drops to less than 0,35 bar (5 psi)
of the charge pressure, the check valve opens, allowing the
pump 2 charge pressure fluid to flow to the brake release
solenoid valve.
When the IOLC30 control module receives the un-park
command from the J2 joystick, the IOLC30 control module
sends a 24 V
DC
output to the drum brake release solenoid
valve, energizing the solenoid. The solenoid valve shifts
position, routing hydraulic fluid to the drum brake piston,
releasing the brake.
When the drum brake switch is moved to the ON-PARK
position, the drum park switch is open, sending a 0 V
DC
signal back to the J2 joystick. The J2 joystick communicates
the on-park brake command to the IOLC30 control module
via the CAN Bus.
When the IOLC30 control module receives the on-park
command from the J2 joystick, the IOLC30 control module
sends a 0 V
DC
output voltage to the drum brake release
solenoid valve, de-energizing the solenoid. This causes the
solenoid valve to return to the default position, allowing the
fluid in the brake piston to flow through the drum brake
release solenoid valve, and back to the tank. The reduced
hydraulic pressure allows spring force to apply the drum
brake.
Drum 3 Motor Loop Flushing
for the following.
Loop flushing of the drum 3 hydraulic motor (7) occurs
whenever the drum 2/drum 3 diverter valve (4) is energized.
The loop flush circuit receives flow from two sources:
•
Main pump flow when the motor is being driven
•
Charge pump flow when the main pump pressure is
reduced
The charge pressure check valve (5) only allows flow from
the charge pump when the main pump pressure is more than
0,35 bar (5 psi) lower than the charge pressure.
CAUTION
Possible Machine Damage!
When raising or lowering a load, do not use the drum park
switch to stop the load movement, since this could cause
damage to the boom. Use the joystick for a controlled
smooth stop.
Содержание MLC650
Страница 1: ...R e f e r e n c e O n l y Service Maintenance Manual Manitowoc MLC650 ...
Страница 2: ...R e f e r e n c e O n l y ...
Страница 4: ...R e f e r e n c e O n l y THE ORIGINAL LANGUAGE OF THIS PUBLICATION IS ENGLISH ...
Страница 375: ...R e f e r e n c e O n l y ...
Страница 376: ...R e f e r e n c e O n l y ...