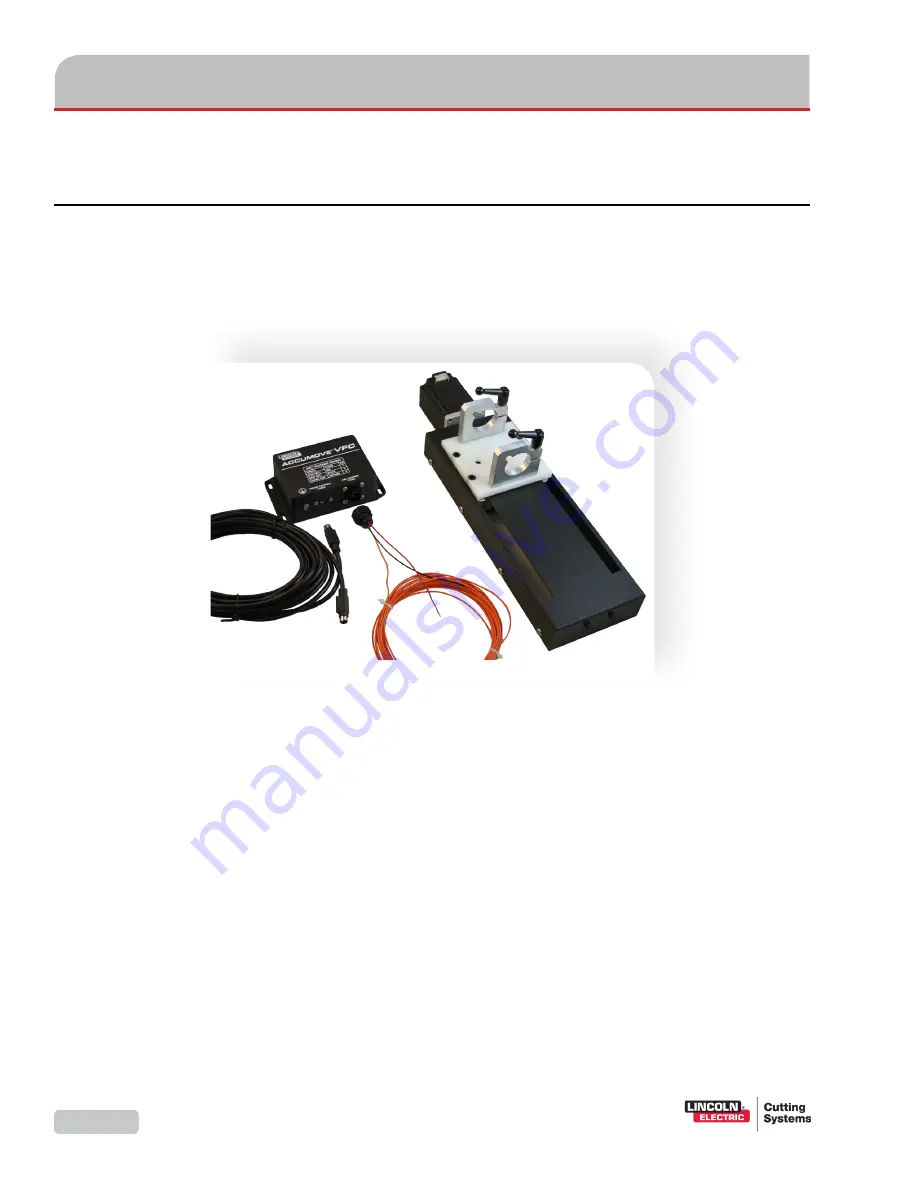
Torchmate 2x2 Growth Series
60
Intelligent AVHC
for plasma
• Approximately 95% of Growth Series customers use their equipment for cutting metal plate
and this number seems to be growing. With this in mind, the Growth Series CNC tables with
Accumove2 Technology come with an advanced system for achieving high quality cutting,
with intelligent Arc Voltage Height Control.
• The details of the Intelligent AVHC will be discussed in the next section.
Other tooling
options
Cutting tools for Growth Series
™
tables
The Growth Series tables with Accumove2 Technology include an AVHC control and Z-axis lifter station for
plasma cutting. The steps that follow illustrate the mounting and wiring for a plasma cutter and AVHC. It is
optional to use a variety of different types of tools to preform other CNC cutting or engraving operations.
For instructions on how to mount and configure other tool options, refer to the manuals supplied with them.
Intelligent AVHC
components
• There are a number of tooling options that can be added to the Growth Series CNC tables,
so that you can increase the versatility of your machine.
• Some of these options can be mounted at the same time as the plasma AVHC, but others
cannot. Consult with your sales representative to review the options that best suit your
needs.
• Each of the other tooling options includes detailed instructions on how to mount and
configure that option for use on your Growth Series table. If you have purchased one of
these options, refer to the included Installation Guide during installation.
• As always, if you have any difficulties, please call Torchmate Technical Support.
Содержание Growth Series
Страница 11: ...Assembly Guide 1 Safety Information ...
Страница 21: ...Assembly Guide 11 Receiving and Preparation ...
Страница 33: ...Assembly Guide 23 Assembling the cutting table ...
Страница 43: ...Assembly Guide 33 Binding the Accumove 2 ...
Страница 56: ...Torchmate Growth Series 46 ...
Страница 57: ...Assembly Guide 47 Coupling the water table optional ...
Страница 69: ...Assembly Guide 59 Deploying the Plasma Cutter ...
Страница 88: ...Torchmate 2x2 Growth Series 78 ...
Страница 89: ...Assembly Guide 79 Maintenance and Parts ...