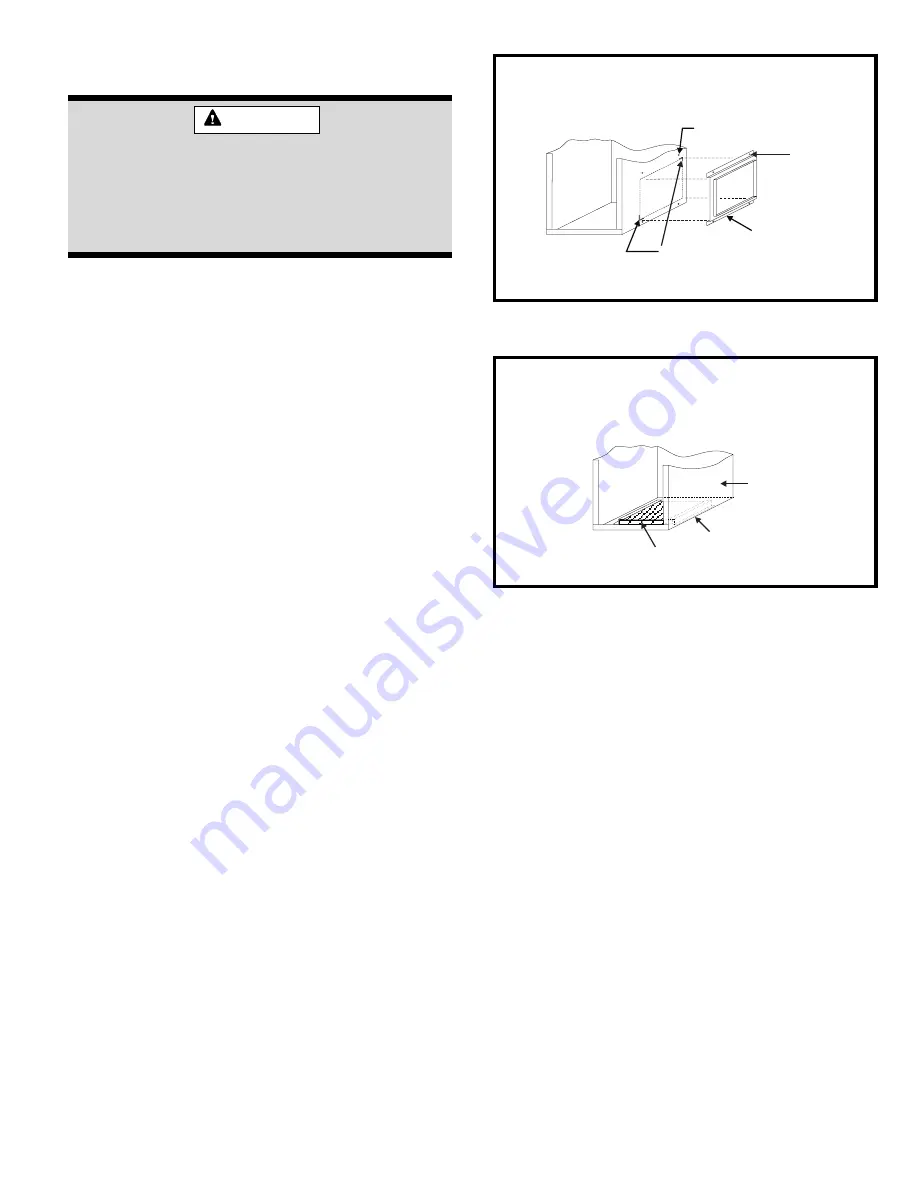
# 45466K003
Page 17
Filter Rack Mounting Hole
Screw
Filter Rack
Corner Embossments
Front of Cabinet
Filter Rack Installation
Figure 18
Electrical Wiring
The furnace must be grounded and wired in accordance
with local codes or, in the absence of local codes, with the
National Electrical Code ANSI/NFPA No. 70 (latest edition)
and/or CSA C22.1 Electrical Code (latest edition) if an
external electrical source is utilized.
In all instances, other than wiring for the thermostat, the
wiring to be done and any replacement of wire shall
conform with the temperature limitation for Type T wire
–
63
°
F (35
°
C) rise.
Connect a sufficiently sized wire with ground to the furnace
’
s
line voltage connections and ground lug. Refer to the
furnace rating plate for electrical characteristics to be used
in sizing field supply wiring and over-current protection.
The line voltage supply should be routed through a
readily accessible disconnect located within sight of the
furnace. A junction box on the furnace side panel is
provided for line voltage connections. Refer to the furnace
wiring diagram for specific connection information.
Proper polarity of the supply connections (“HOT”
and “NEUTRAL”) must be observed to ensure that
safety controls provide the protection intended.
A connection to the ground lug and actual earth ground
(typically a ground stake or buried steel pipe) must be
maintained for proper operation.
Filters
Filters are not supplied with CG90CB or CG90UB
series furnaces.
G1D91BU and G1D93BU Models
A filter rack and cleanable 16" x 25" x 1/2" filter are
supplied with the furnace. (Models designed for more than
1600 CFM nominal air delivery include two of each.) The
filter rack is to be installed between the return air duct and
the side of the furnace. Refer to Figure 18 and the follow-
ing instructions to install the filter rack:
1. Using the corner embossments as a guide, mark and
cut a full-size opening in the side panel(s).
2. Using the filter rack as a template, mark and drill four
7/64" diameter screw holes in the side panel(s).
3. With the filter access opening toward the front of the
furnace, use sheet metal screws to fasten the rack(s)
to the side panel(s).
The filter slides in the rack from the front of the unit. Install
the filter(s) with the mesh side towards furnace.
For units that do not include a side return filter rack, kit
AFILT524 can be used. Single side filter frame kit
AFILTHA7 is available for single side return air connection
in installations requiring more than 1600 CFM nominal air
delivery. Bottom return filter kit AFILT529 is also available
from the manufacturer.
Counterflow Models:
Filters are not supplied with these furnaces; however, filters
must be used. It is the installerís responsibility to install
properly sized filters in accordance with Table 3 on page 18.
Other filter accessories are also available from the manufac-
turer including a full line of indoor air quality products. For
information on these products, contact the local distributor.
Risk of electrical shock. Disconnect electrical
power at the circuit breaker or service panel
before making electrical connections. Failure
to disconnect power supplies can result in
property damage, personal injury, or death.
WARNING
Bottom Filter Location
Upflow Models
Figure 19
Filter
Base
Side