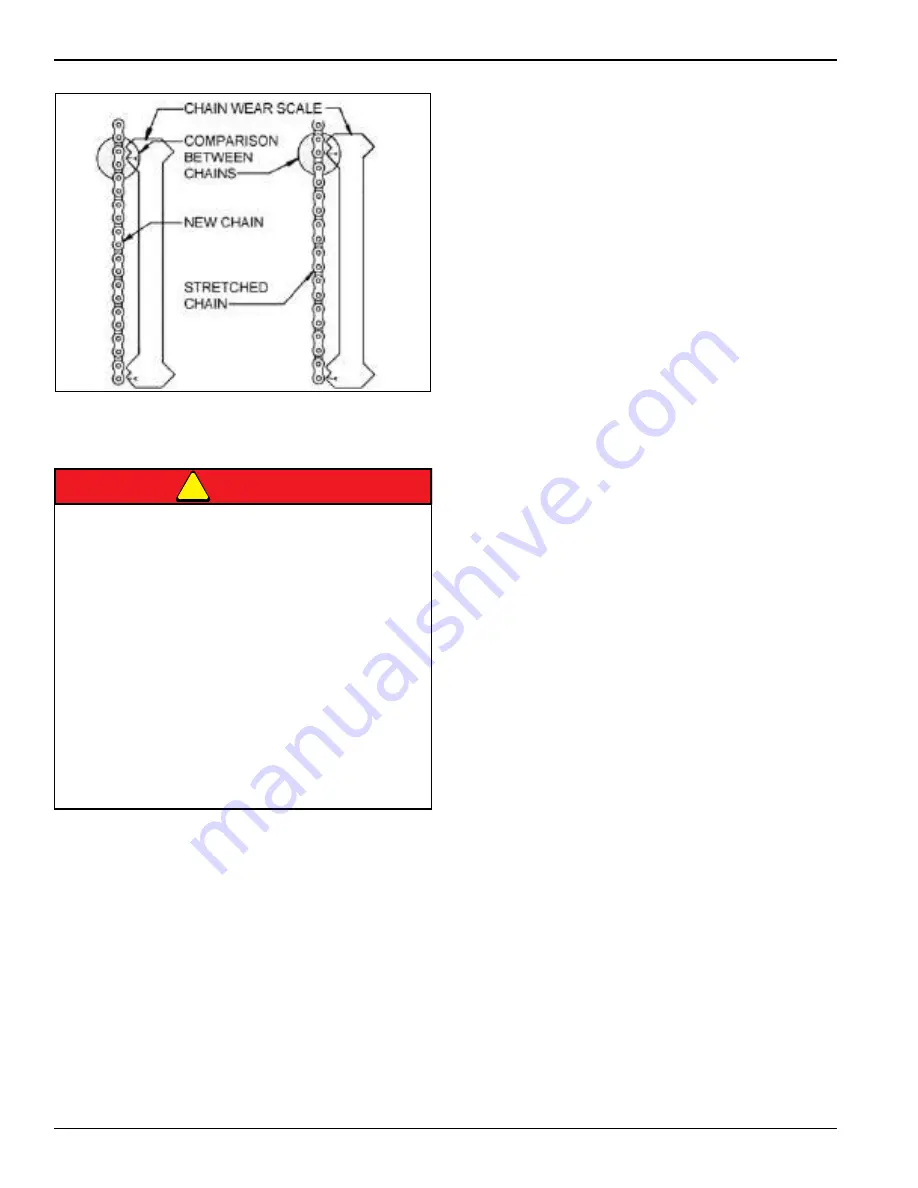
2-20
F-581-R1
PLANNED MAINTENANCE
Figure 2-28: Chain Stretch Gauge
Fork Inspection
DANGER
Check the top clip retaining pin and fork heel for signs of
cracks and wear. Report any
signs of cracks and wear to
your supervisor immediately.
The following provides detailed procedures necessary to
provide a complete fork and associated components
inspection.
Rated Capacity and Load Center
1. The rated capacity of each fork must be at least half
of the rated capacity stated on the identification plate.
2. The load center of each fork must match the load
center stated on the identification plate.
3.
If the values do not match, replace the fork with one
that has the correct characteristics.
Cracks
Visually examine the forks for cracks and, if considered
necessary, perform a non-destructive crack detection
test. Pay special attention to:
1.
Fork heel
2. Welds that attach mounting components to the fork
blank
3. Top clip retaining pin
Straightness of Blade and Shank
Check the straightness of the upper face of each
blade and the front face of each shank. If the deviation
from straightness exceeds 0.5% of the length of the blade
and/or the height of the shank, respectively, repair or
replace the fork set.
Fork Angle
Check the angle between the upper face of each fork
blade and the load face of each shank. If the deviation
exceeds 3º from the original specification, repair or
replace the fork.
Difference in Height Between Fork Tips
Check the difference in height between each fork blade,
measured at the tip with the fork mounted on the fork
carrier. If the difference in tip heights exceeds 3% of the
length of the blade, repair or replace the fork.
Positioning Lock
Check the positioning lock on each fork to make sure it
functions properly. If any problems are noted, repair or
replace the fork.
Wear
Two different areas of the fork and fork attachment should
be checked for wear: Blade and Hooks.
Fork Blade and Shank
Check each fork blade and shank for wear, pay special
attention to the area surrounding the heel of the fork. If
the thickness is reduced to 90% of the original thickness,
repair or replace the fork.
Fork Hooks
Check the support face of the top hook and the retaining
faces of both hooks for wear, crushing, and other local
deformations. If any of these deficiencies cause
excessive clearance between the fork and the fork
carrier, repair or replace the fork.
•
NEVERoperate your Bendi B40i4 forklift if you
suspect the forks are
damaged. Report fork
damage to your supervisor immediately.
• It is recommended to use only Landoll
Corporation replacement parts.
• NEVER use forks repaired by welding.
• Always replace both forks. Switching forks
from one forklift to another can be dangerous
if the capacity of the forks is not known.
•
If you find any defect in the forks or mounting
components, take the
forklift out of service
until the fork is repaired or replaced.
• Failure to follow these recommendations can
cause the load to fall resulting in serious
injury
or death.
Содержание Bendi B40i4
Страница 2: ......
Страница 26: ...1 20 F 581 R1 INTRODUCTION SAFETY AND INSPECTION...
Страница 100: ...3 52 F 581 R1 TROUBLESHOOTING AND CORRECTIVE MAINTENANCE...
Страница 120: ...4 20 F 581 R1 CALIBRATION AND PROGRAMMING...
Страница 129: ...ENGINE WITH FUEL SYSTEM 5 9 Figure 5 10 Fuel System Troubleshooting...
Страница 133: ...ENGINE WITH FUEL SYSTEM 5 13...
Страница 134: ...5 14 F 581 R1 ENGINE WITH FUEL SYSTEM...
Страница 140: ...6 2 F 581 R1 GM ENGINE SUPPLIER PROVIDED DOCUMENTATION...