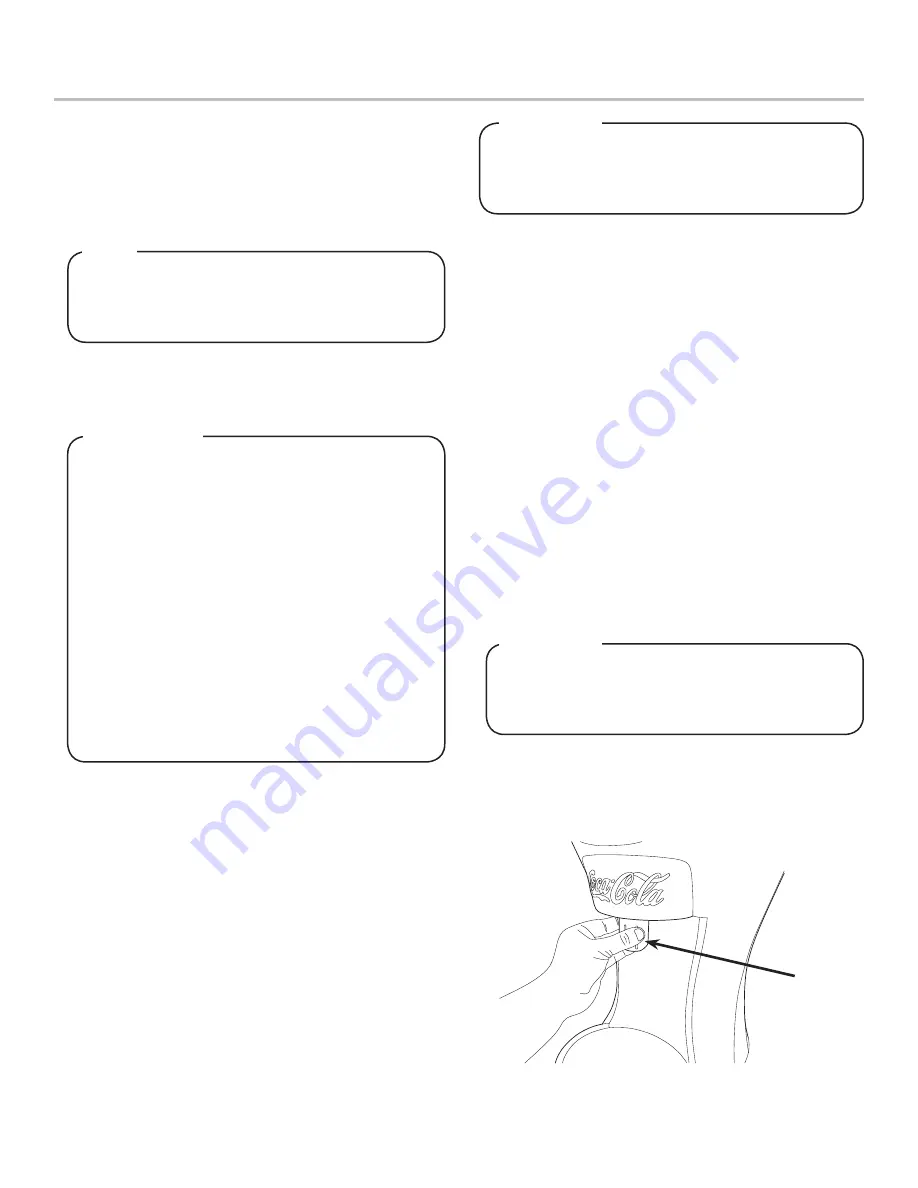
14
Cleaning Solution
Mix a mild, non-abrasive detergent (e.g. Sodium Laureth
Sulfate, dish soap) with clean, potable water at a temperature
of 90°F to 110°F (32°C to 43°C). The mixture ratio is one
ounce of cleaner to two gallons of water. Prepare a minimum of
five gallons of cleaning solution. Do not use abrasive
cleaners or solvents because they can cause permanent
damage to the unit. Ensure rinsing is thorough, using clean,
potable water at a temperature of 90°F to 110°F. Extended
lengths of product lines may require additional cleaning solution.
Sanitizing Solution
Prepare the sanitizing solution in accordance with the
manufacturer’s written recommendations and safety guidelines.
The type and concentration of sanitizing agent recommended in
the instructions by the manufacturer shall comply with 40 CFR
§180.940. The solution must provide 100 parts per million (PPM)
chlorine (e.g. Sodium Hypochlorite or bleach) and a minimum of
five gallons of sanitizing solution should be prepared.
If a powder sanitizer is used, dissolve it thoroughly
with hot water prior to adding to the syrup system.
Ensure sanitizing solution is removed from the
dispenser as instructed.
!
CAUTION
CLEANING AND SANITIZING
General Information
•
Lancer equipment (new or reconditioned) is shipped from
the factory cleaned and sanitized in accordance with NSF
guidelines. The operator of the equipment must provide
continuous maintenance as required by this manual and/or
state and local health department guidelines to ensure prop
-
er operation and sanitation requirements are maintained.
•
Cleaning should be accomplished only by trained personnel.
Sanitary gloves are to be used during cleaning operations.
Applicable safety precautions must be observed. Instruction
warnings on the product being used must be followed.
The cleaning procedures provided herein pertain to the
Lancer equipment identified by this manual. If other
equipment is being cleaned, follow the guidelines
established by the manufacturer for that equipment.
NOTE
• Use sanitary gloves when cleaning the unit and
observe all applicable safety precautions.
• DO NOT
use a water jet to clean or sanitize the
unit.
• DO NOT
disconnect water lines when cleaning
and sanitizing syrup lines, to avoid contamination.
• DO NOT
use strong bleaches or detergents; These
can discolor and corrode various materials.
• DO NOT
use metal scrapers, sharp objects, steel
wool, scouring pads, abrasives, or solvents on the
dispenser.
• DO NOT
use hot water above 140° F (60° C). This
can damage the dispenser.
• DO NOT
spill sanitizing solution on any circuit
boards. Insure all sanitizing solution is removed
from the system.
!
ATTENTION
Cleaning and Sanitizing Product Lines
1. Disconnect product lines from BIB’s or other product supply.
2. Place product lines, with BIB connectors, in a bucket of
warm water.
3.
Activate each valve to fill the lines with warm water and flush
out product remaining in the lines.
4. Prepare Cleaning Solution described above.
5. Place product lines, with BIB connectors, into cleaning
solution.
6.
Activate each valve until lines are filled with cleaning
solution then let stand for ten (10) minutes.
7. Flush out cleaning solution from the syrup lines using clean,
warm water.
8. Prepare Sanitizing Solution described above.
9. Place product lines into sanitizing solution and activate each
valve to fill lines with sanitizer. Let sit for ten (10) minutes.
10.
Reconnect product lines to BIB’s and draw drinks to flush
solution from the dispenser.
11.
Taste the drink to verify that there is no off-taste. If off-taste
is found, flush product system again.
Following sanitization, rinse with end-use product
until there is no aftertaste. Do not use a fresh water
rinse. This is a NSF requirement. Residual sanitizing
solution left in the system creates a health hazard.
!
CAUTION
Cleaning and Sanitizing Nozzle
1. Disconnect power, so as to not activate valve while cleaning.
2. Remove outer nozzle by twisting counter clockwise and
pulling down.
A. Nozzle
A
3. Rinse nozzle with warm water.