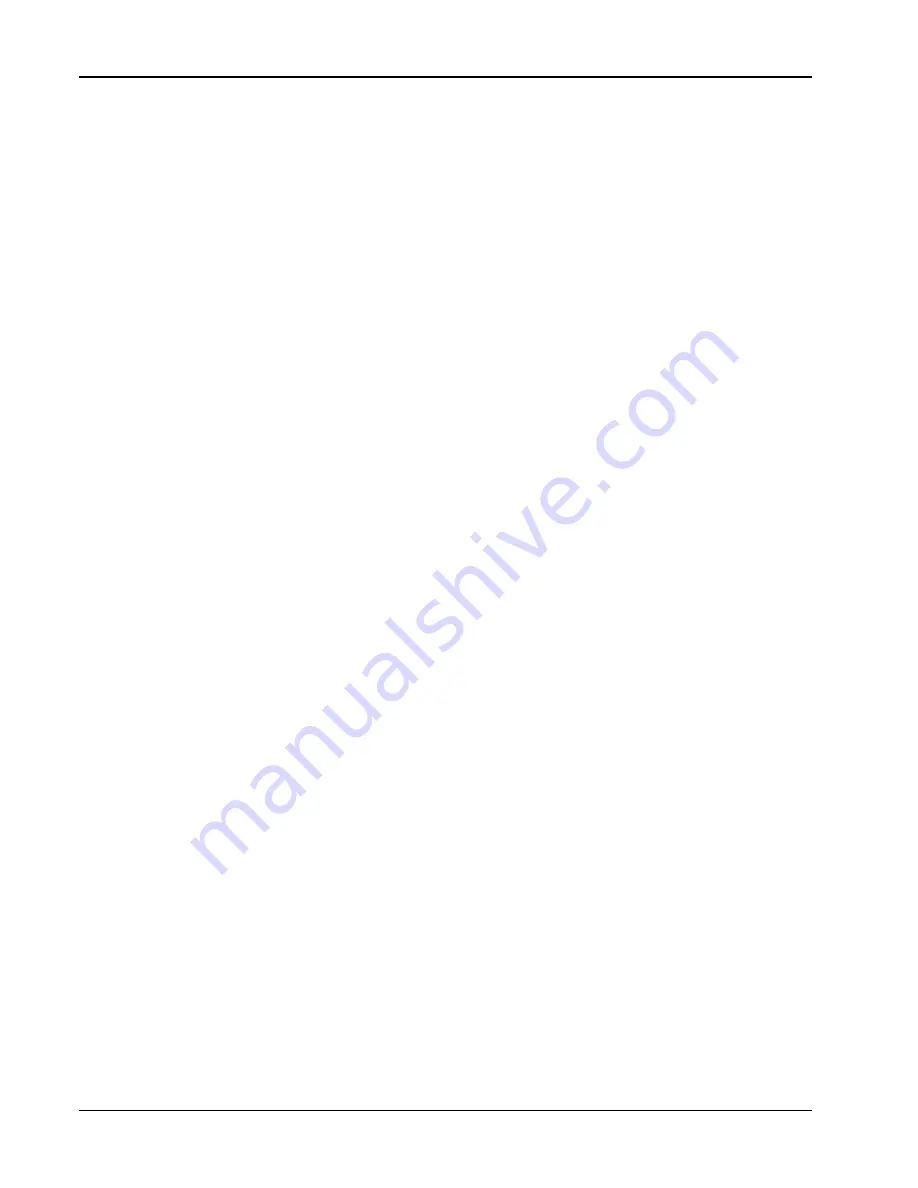
Lake Shore Model 475 Gaussmeter User’s Manual
2-10
Background
2.4.2
Tuning a Closed Loop PI Controller
There has been a lot written about tuning closed loop control systems and specifically PI control loops. This section does
not attempt to compete with control theory experts. It describes a few basic rules of thumb to help less experienced users
get started. This technique will not solve every problem, but it has worked for many others in the field. This section
assumes the user has worked through the operation sections of this manual.
Be sure to setup the Control Slope Limit and the Analog Output Voltage Limit before attempting to tune the field control
system. This will assure that the magnet power supply will not be damaged if the field control system is improperly
tuned or begins to oscillate. Refer to Paragraph 5.3 to setup field control. Also, begin control with the DC filter set to
3 or 4 digits of resolution. Since the field control works on the filtered readings, it becomes difficult to control the system
with the added time constant from the slow filtering on the 5 digit setting.
2.4.2.1
Tuning Proportional
The proportional setting is tied to the overall gain of the system. The gain of the power supply should be fairly constant
over its entire range of operation but the gain of the magnet changes with field. As the magnet approaches saturation, the
amount of current needed to change the field a given amount increases substantially. No single value of P will be
sufficient to maintain acceptable control over the entire range of magnet operation.
To find the correct proportional setting for a system, turn off the I setting and start with a low value for P, approximately
5 or 10. Set the control setpoint to some low, non-zero field, 1 kG for example. If the field is oscillating, then P is too
high and needs to be reduced. If the field is not oscillating, increase P by a factor of two until the system begins to
oscillate. See Figure 2-8(a). Do not set the proportional setting so high that it causes violent oscillations. The appropriate
value for P is one half of the value required for sustained oscillation. An even lower setting of one quarter may be
desired for minimal overshoot. See Figure 2-8(b).
2.4.2.2
Tuning Integral
When the proportional setting is chosen and the integral is turned off, the Model 475 will control the field to some value
below the setpoint. Setting the integral allows the Model 475 control algorithm to gradually eliminate the difference in
field by integrating the error over time. See Figure 2-8(d). An integral setting that is too low causes the field to take too
long to reach the setpoint. An integral setting that is too high can create overshoot, which cannot be tolerated in many
magnetic systems. An integral setting that is very high will eventually cause the field to oscillate.
Begin this part of the tuning process using the proportional setting found above. Enter an I setting of 100 to start with. If
the field begins to oscillate, increase the I setting by a factor of two. Remember, in the Model 475, the integral term is set
in seconds and a
smaller setting creates a more active integrator
. If the field is stable but never reaches the setpoint, the
integral setting is too high and should be reduced by one half.
To verify the integral setting, make a few small (1 kG) changes in setpoint and watch the field react. Trial and error can
help improve the integral setting by optimizing for experimental needs. Faster integrals, for example, get to the setpoint
more quickly at the expense of greater overshoot.
Содержание 475
Страница 16: ...Lake Shore Model 475 Gaussmeter User s Manual 1 6 Introduction 1 4 SAFETY SYMBOLS ...
Страница 25: ...Lake Shore Model 475 Gaussmeter User s Manual Background 2 9 Figure 2 8 Examples of PI Control ...
Страница 36: ...Lake Shore Model 475 Gaussmeter User s Manual 3 10 Installation This Page Intentionally Left Blank ...
Страница 68: ...Lake Shore Model 475 Gaussmeter User s Manual 4 32 Operation This Page Intentionally Left Blank ...
Страница 82: ...Lake Shore Model 475 Gaussmeter User s Manual 6 6 Remote Operation Figure 6 2 Model 475 Status System ...