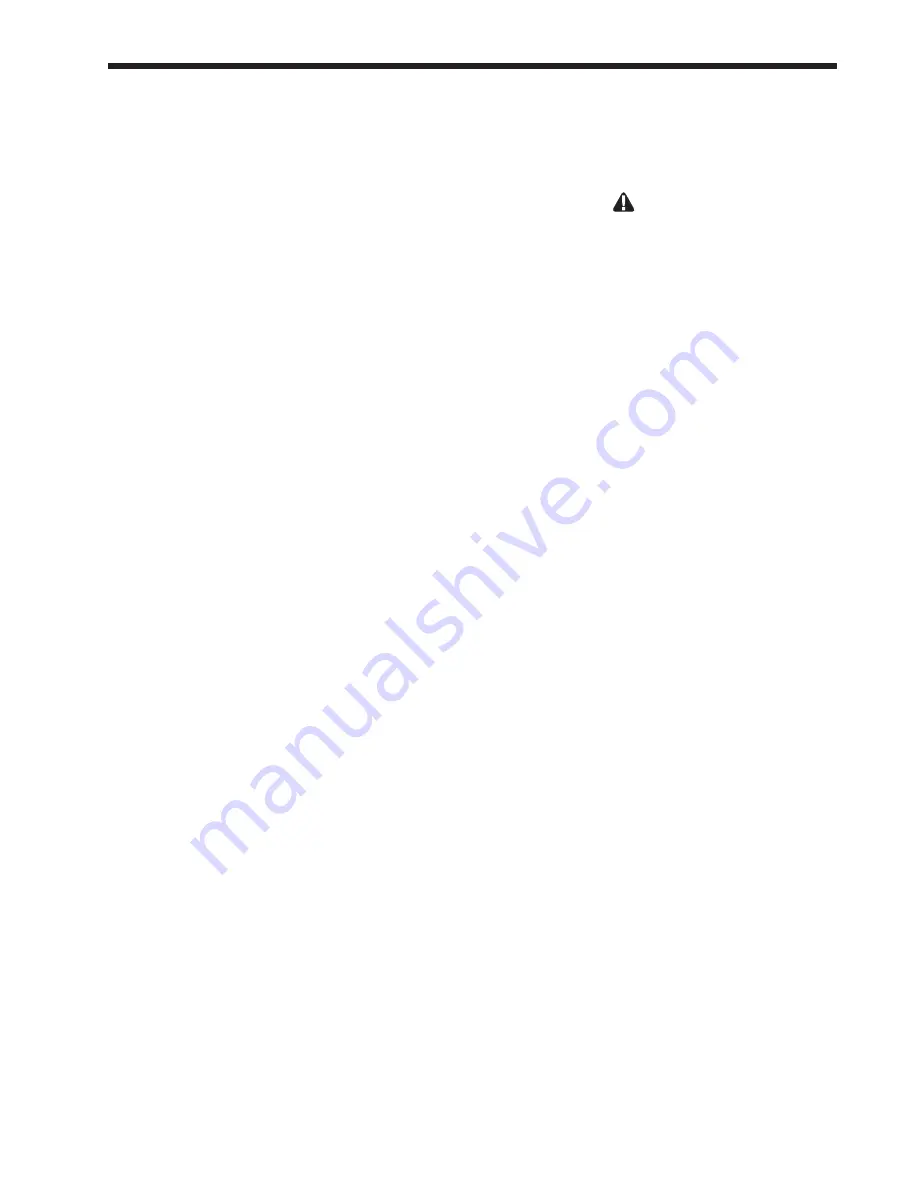
NeoTherm LC Boilers and Water Heaters
Page 17
Section 4
GAS SUPPLY AND PIPING
4.1
Gas Supply and Piping
Gas piping should be supported by suitable hangers
or floor stands, not the appliance.
Installers should refer to local building and safety
codes or, in the absence of such requirements, follow
the National Fuel Gas Code, ANSI Z223.1 NFPA 54
and/or CSA B149.1, Installation Codes.
Review the following instructions before proceeding
with the installation.
1. Verify that the appliance is fitted for the
proper type of gas by checking the rating
plate. NeoTherm LC will function properly
without the use of high altitude modification at
elevations up to 10,000 feet (3050 m).
2. The maximum inlet gas pressure must not
exceed 13” W.C. (3.2 kPa). The minimum inlet
gas pressure is 4” W.C. (1.0 kPa).
3. Refer to Tables 6A, 6B, 6C and 6D to size the
piping.
4. Run the gas supply line in accordance with all
applicable codes.
5. Locate and install manual shutoff valves in
accordance with state and local requirements.
6. A sediment trap must be provided upstream of
the gas controls.
7. All threaded joints should be coated with
piping compound resistant to the action of
liquefied petroleum gas.
8. The appliance and its individual shutoff valve
must be disconnected from the gas supply
piping during any pressure testing of that
system at test pressures in excess of 1/2 PSIG
(3.45 kPa).
9. The unit must be isolated from the gas supply
system by closing its individual manual shutoff
valve during any pressure testing of the gas
supply piping system at test pressures equal to
or less than 1/2 PSIG (3.45 kPa).
10. The appliance and its gas connection must be
leak tested before placing it in operation.
11. Purge all air from gas lines.
WARNING
Open flame can cause gas to ignite and result in
property damage, severe injury, or loss of life.
Note -
The NeoTherm LC appliance and all other
gas appliances sharing the gas supply line must
be firing at maximum capacity to properly measure
the inlet supply pressure. The pressure can be
measured at the supply pressure port on the gas
valve. Low gas pressure could be an indication of
an undersized gas meter, undersized gas supply
lines and/or an obstructed gas supply line. Some
NeoTherm LC’s are equipped with low and high gas
pressure switches that are integrally vent limited.
These types of devices do not require venting to
atmosphere.
Содержание NTH1000
Страница 4: ...LAARS Heating Systems ...
Страница 11: ...NeoTherm LC Boilers and Water Heaters Page 7 Fig 6 Dimensions NT 1700 ...
Страница 37: ...NeoTherm LC Boilers and Water Heaters Page 33 Fig 21 Ladder Diagram ...
Страница 38: ...LAARS Heating Systems Page 34 Fig 22 Wiring Diagram ...
Страница 39: ...NeoTherm LC Boilers and Water Heaters Page 35 ...
Страница 51: ...NeoTherm LC Boilers and Water Heaters Page 47 Fig 51 Connection Terminals ...
Страница 128: ...LAARS Heating Systems Page 124 Fig 140 Machine Frame NT1000 13 3 Parts Illustrations ...
Страница 129: ...NeoTherm LC Boilers and Water Heaters Page 125 Fig 141 Rear Panel NT1000 Fig 142 Rear Panel NT1700 ...
Страница 130: ...LAARS Heating Systems Page 126 Fig 143 Machine Frame NT1700 ...
Страница 131: ...NeoTherm LC Boilers and Water Heaters Page 127 Fig 144 Front Panels and Covers NT1000 and NT1700 ...
Страница 132: ...LAARS Heating Systems Page 128 Fig 145 Burners and Combustion Chamber NT1000 ...
Страница 133: ...NeoTherm LC Boilers and Water Heaters Page 129 Fig 146 Burners and Combustion Chamber NT1700 ...
Страница 134: ...LAARS Heating Systems Page 130 Fig 147 Heat Exchanger Components NT1000 and NT1700 Fig 148 Burner Detail NT1000 ...
Страница 135: ...NeoTherm LC Boilers and Water Heaters Page 131 Fig 149 Burner Detail NT1700 ...
Страница 136: ...LAARS Heating Systems Page 132 Fig 150 Electronic Components Fig 151 Condensate Trap NT1000 ...
Страница 137: ...NeoTherm LC Boilers and Water Heaters Page 133 Fig 152 Condensate Trap NT1700 Fig 153 Flow Switch NT1000 and NT1700 ...
Страница 138: ...LAARS Heating Systems Page 134 This page intentionally left blank ...
Страница 139: ...NeoTherm LC Boilers and Water Heaters Page 135 This page intentionally left blank ...