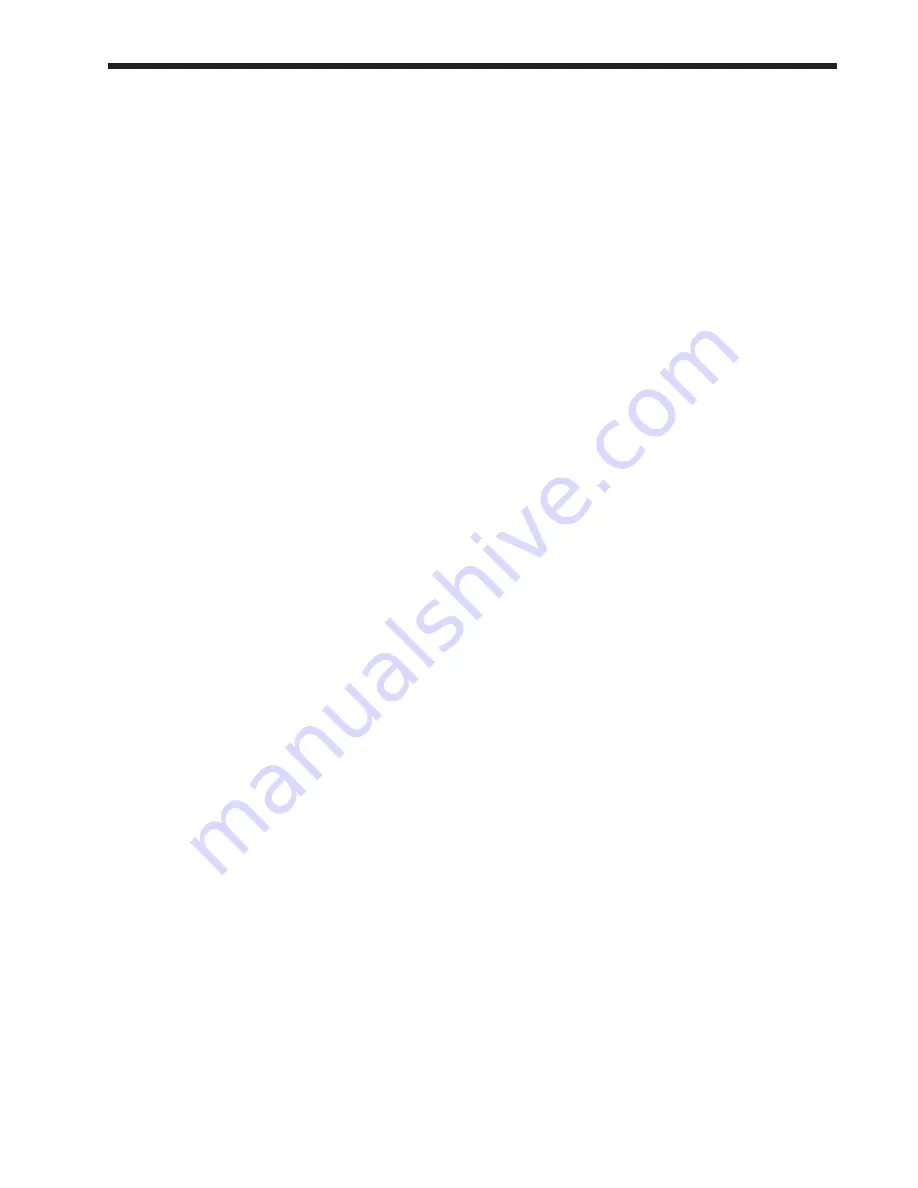
NeoTherm LC Boilers and Water Heaters
Page 75
turn the High Fire adjustment screw counter-
clockwise. To lower the high fire CO
2
level,
turn the screw clockwise.
(Make the adjustment in small steps of 1/8
turn to avoid “overshooting” the correct
setting. The valve is built with a bit of
“backlash.” This makes it appear that
changing the adjustment does not change
the CO
2
level when you first stop turning the
control in one direction, and start turning it the
other way. Once the backlash has been taken
up, the control will be quite sensitive.)
14. Repeat step 13, except this time set the fan
speed RPM to 1200rpm. (Again, the actual
RPM will not go this low – the control will
limit the fan speed to the minimum set at the
factory.) This will force the boiler to operate
in low fire. Adjust the Low Fire screw so the
CO
2
is 0.5% lower than the high fire CO
2
.
To raise the low fire CO
2
, turn the Low Fire
adjustment screw clockwise. To lower the low
fire CO
2
, turn the screw counter-clockwise.
15. The adjustment you made for the Low Fire
setting could affect the High Fire setting, so
you need to re-check the High Fire setting.
Go back to the Operations screen and set the
Firing Rate back to 8000 RPM. The CO
2
should still be about at the level listed in Table
17. If the CO
2
is not correct, repeat the steps
listed above.
16. Set the Firing Rate back to 1200 RPM, and re-
check the CO
2
during Low Fire.
17. Once the CO
2
values are correct for both High
Fire and Low Fire, go back to the Operation
screen and select Automatic operation. At this
point, you have set up the Primary burner for
this boiler.
18. Now you can do the same setup for the
Secondary burner on this boiler. To do this,
you need to shut off the Primary burner. On
the Secondary control, you set the High and
Low Fire RPM and check the CO
2
output for
each condition. We will review the process
quickly here:
• On the ‘home’ screen, press the icon for the
Primary controller.
• On the Status Summary screen, press the
Operation button.
• On the Operation screen, turn off the
Primary burner by pressing the Operation
Enable button.
• On the ‘home’ screen, press the icon for the
Secondary controller.
• On the Status Summary screen, press the
Operation button.
• On the Operation screen for the Secondary
burner, press the yellow box for the Firing
Rate. Login using the installer-level password,
then press OK.
• Now you can change the Firing Rate entry
for the Secondary burner. Enter 8000 RPM
for the High Fire value. Adjust the High Fire
screw to get the CO
2
level listed in Table 17.
• Set the Firing Rate to 1200rpm. Adjust the
Low Fire screw so the CO
2
level reaches the
CO
2
level listed in Table 17.
• Re-check the High Fire setting at 8000
RPM. The CO
2
should still be about 8.5% or
9.0%, depending on the model size.
• Re-check the CO
2
during Low Fire at 1200
RPM.
• Once the CO
2
values are correct for both
High Fire and Low Fire, go back to the
Operation screen for the Secondary burner
and select Automatic operation. At this point,
you have set up the Secondary burner for this
boiler.
• Go back to the ‘home’ screen and press the
icon for the Primary control. On the Status
Summary screen, press the Operation button.
On the Operation screen, press the Burner
button to turn on the Primary burner.
19. Once both burners are set up properly, operate
both burners together as described below, and
check the CO
2
levels with the unit operating at
high fire and at low fire. The final CO
2
values
at high fire should be as listed in Table 17
±0.2%. At low fire, the CO
2
should be about
0.5% lower than the high fire CO
2
reading.
(The offset is more important than the actual
CO
2
value)
Monitor the CO
2
and CO levels for one
complete operating cycle. The CO should
never be more than 150 ppm. The CO
2
level
should also track between the high and low
limits listed in the table.
Setting the fan speed RPMs for both burners
operating together -
• It is important that both burners operate at
the same fan speed. Before changing the fan
speeds, turn off the call for heat.
• Set the fan speed for each burner separately,
using the procedure we described earlier -
steps 6 though 11 for the Primary burner, and
step 18 for the Secondary burner. On each
burner, enter a value of 8000 RPM for the high
fire test.
• Once you have set both burners to run at
8000 RPM, turn on the call for heat, and check
the results as described above.
Содержание NTH1000
Страница 4: ...LAARS Heating Systems ...
Страница 11: ...NeoTherm LC Boilers and Water Heaters Page 7 Fig 6 Dimensions NT 1700 ...
Страница 37: ...NeoTherm LC Boilers and Water Heaters Page 33 Fig 21 Ladder Diagram ...
Страница 38: ...LAARS Heating Systems Page 34 Fig 22 Wiring Diagram ...
Страница 39: ...NeoTherm LC Boilers and Water Heaters Page 35 ...
Страница 51: ...NeoTherm LC Boilers and Water Heaters Page 47 Fig 51 Connection Terminals ...
Страница 128: ...LAARS Heating Systems Page 124 Fig 140 Machine Frame NT1000 13 3 Parts Illustrations ...
Страница 129: ...NeoTherm LC Boilers and Water Heaters Page 125 Fig 141 Rear Panel NT1000 Fig 142 Rear Panel NT1700 ...
Страница 130: ...LAARS Heating Systems Page 126 Fig 143 Machine Frame NT1700 ...
Страница 131: ...NeoTherm LC Boilers and Water Heaters Page 127 Fig 144 Front Panels and Covers NT1000 and NT1700 ...
Страница 132: ...LAARS Heating Systems Page 128 Fig 145 Burners and Combustion Chamber NT1000 ...
Страница 133: ...NeoTherm LC Boilers and Water Heaters Page 129 Fig 146 Burners and Combustion Chamber NT1700 ...
Страница 134: ...LAARS Heating Systems Page 130 Fig 147 Heat Exchanger Components NT1000 and NT1700 Fig 148 Burner Detail NT1000 ...
Страница 135: ...NeoTherm LC Boilers and Water Heaters Page 131 Fig 149 Burner Detail NT1700 ...
Страница 136: ...LAARS Heating Systems Page 132 Fig 150 Electronic Components Fig 151 Condensate Trap NT1000 ...
Страница 137: ...NeoTherm LC Boilers and Water Heaters Page 133 Fig 152 Condensate Trap NT1700 Fig 153 Flow Switch NT1000 and NT1700 ...
Страница 138: ...LAARS Heating Systems Page 134 This page intentionally left blank ...
Страница 139: ...NeoTherm LC Boilers and Water Heaters Page 135 This page intentionally left blank ...