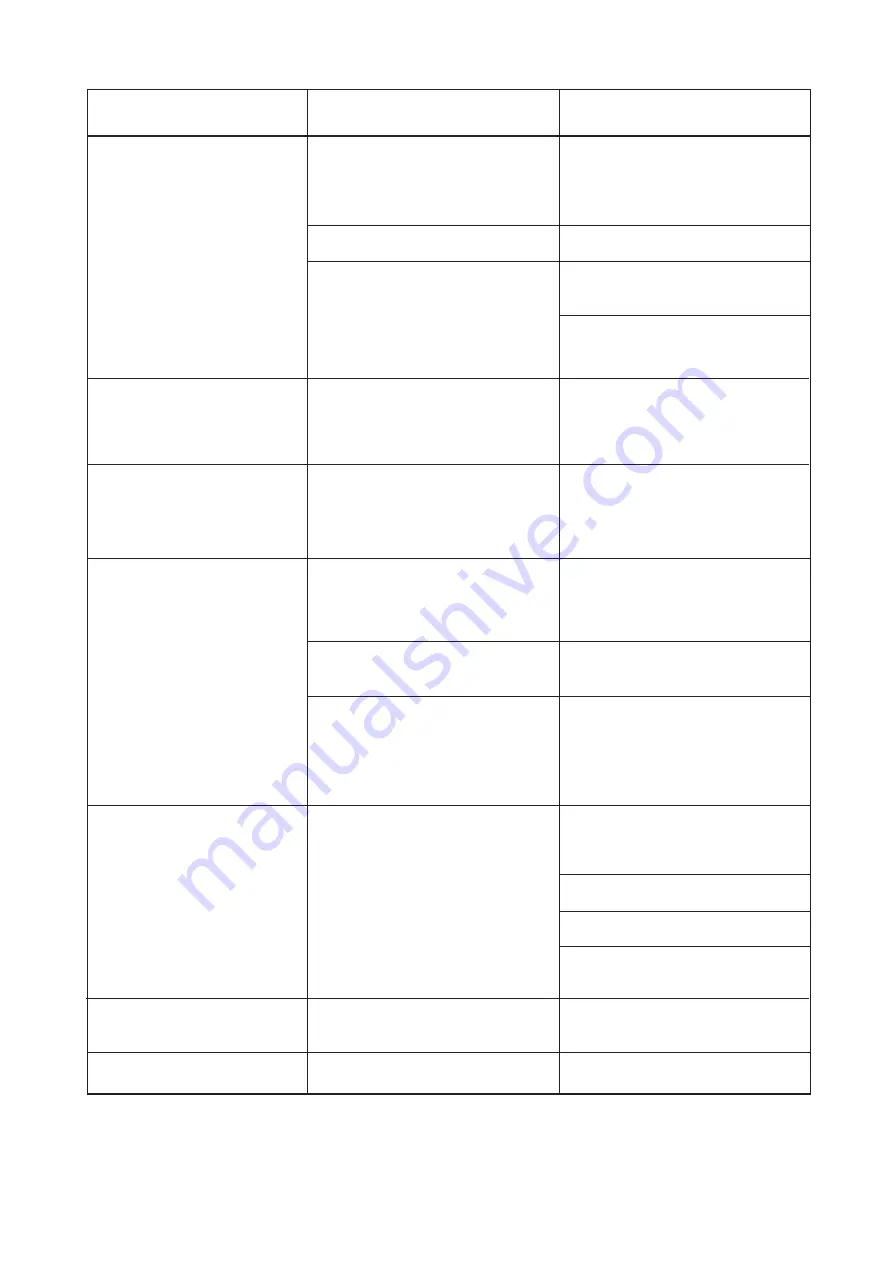
- 38 -
PROBLEM
CAUSE
REMEDY
Tilth produced is too fine
Rotor speed (rotational frequency)
Reduce the speed (rotational
too high
frequency) at the gearbox (see
optional sets of matching gears on
page 16)
Forward speed is too slow
Increase the forward speed
Rear levelling bars are too low
Raise, remove the rear levelling
bars (page 27)
Fit the levelling bars to the front
(page 27)
Ridging at the side of the
Anti-ridging plate incorrectly
Position each anti-ridging plate
machine
positioned on the side deflectors
closer to the ground and to the
corresponding roller (see page 21)
Excessive blade wear
Rotor speed (rotational frequency)
Reduce the rotor speed (rotational
is too high
frequency) and fit the rear leveling
bars (pages 16 and 27)
Erratic packer rollers
Worn or incorrectly adjusted
Position each scraper plate closely
function
scraper plates
to the corresponding roller (see
page 18)
Scrapers jammed by trash
Clean the scrapers by pivoting
them to the rear (see page 18)
Scraper bars incorrectly
Make sure that the scraper bars
positioned
are in its furthest forward posi-
tion.
Plates must only be slid forward
one at a time (page 18)
Plugging from ground build
Sandy soil
Mount the levelling bars to the
up in front of the packer
rear (page 27)
rollers
Slightly lenghten the top link
Reduce forward speed
Use maxipacker rollers
(for HR 6002 DR / 6002 DR - S)
Ridging at the center of the
Incorrect levelling share setting
Refine levelling share setting
machine
(see page 22)
Maxicrumbler roller clogging
Humid conditions
Use a packer roller