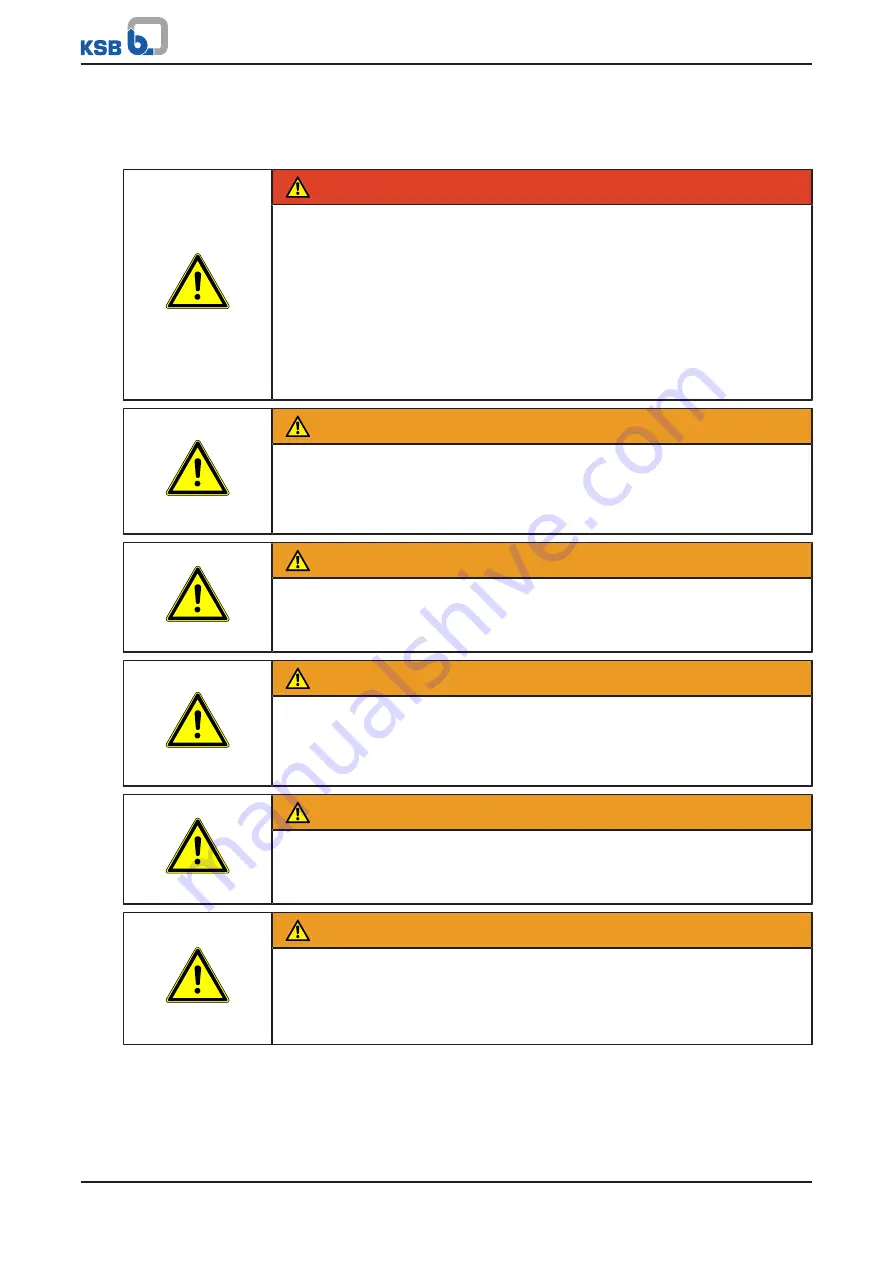
7 Servicing/Maintenance
64 of 126
Amacan K
1579.807/07-EN
7.6 Dismantling the pump set
7.6.1 General information/Safety regulations
DANGER
Improper transport
Danger to life from falling parts!
Damage to the pump set!
▷
Use the attachment point provided (eyebolt, lifting lug or bail) for attaching
lifting accessories.
▷
Never suspend the pump set by its power cable.
▷
Never use the lifting ropes included in KSB's scope of supply for lifting loads
other than the KSB product supplied.
▷
Securely attach the lifting ropes to the pump and crane.
WARNING
Unqualified personnel performing work on the pump (set)
Risk of injury!
▷
Always have repair work and maintenance work performed by specially trained,
qualified personnel.
WARNING
Hot surface
Risk of injury!
▷
Allow the pump set to cool down to ambient temperature.
WARNING
Improper lifting/moving of heavy assemblies or components
Personal injury and damage to property!
▷
Use suitable transport devices, lifting equipment and lifting tackle to move
heavy assemblies or components.
WARNING
Excess pressure inside the pump set
Risk of injury when opening the pump set!
▷
Take care when opening the inner chambers. Equalise the pressure.
WARNING
Components with sharp edges
Risk of cutting or shearing injuries!
▷
Always use appropriate caution for installation and dismantling work.
▷
Wear work gloves.
Содержание Amacan K
Страница 124: ......
Страница 125: ......
Страница 126: ...KSB SE Co KGaA Johann Klein Stra e 9 67227 Frankenthal Germany Tel 49 6233 86 0 www ksb com 1579 807 07 EN 01117570...