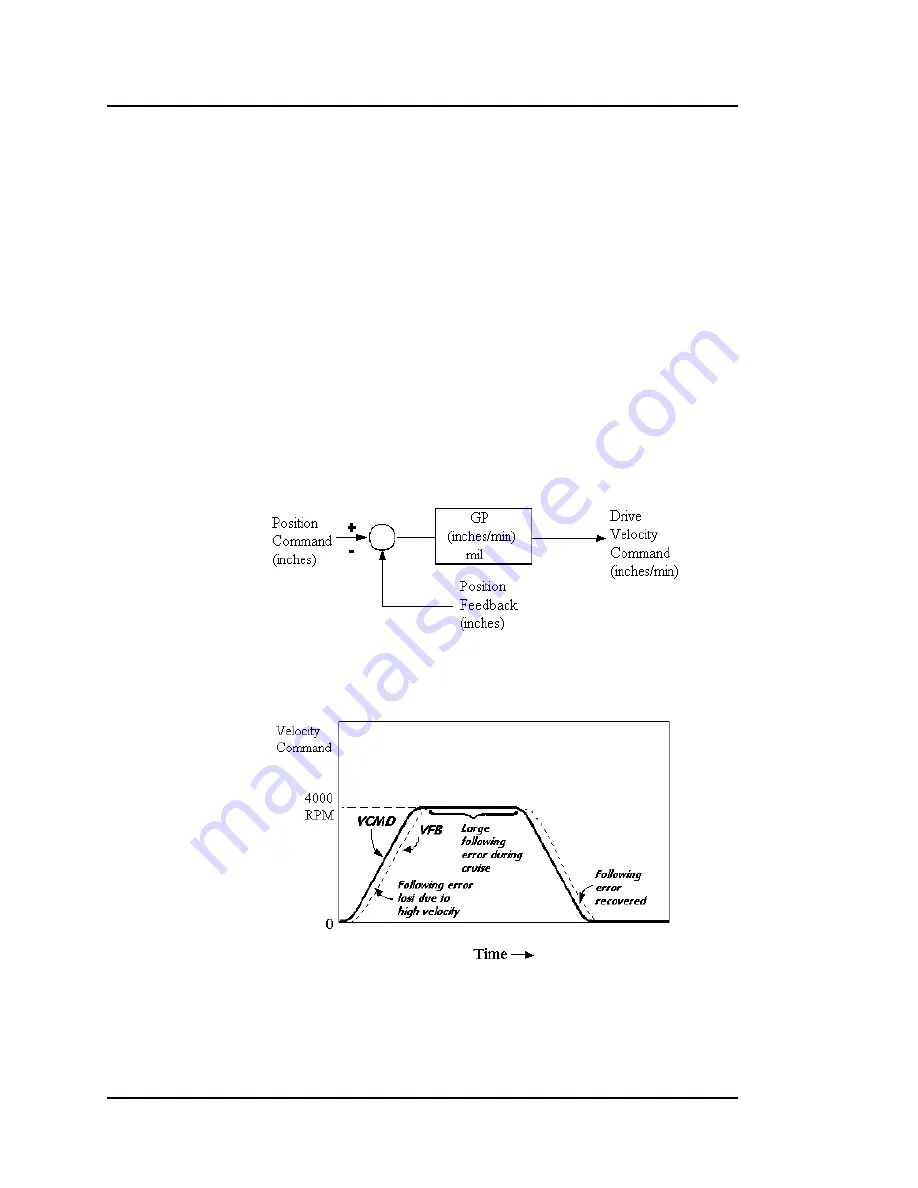
Danaher Motion
06/2005
Project
Care should be taken to set
PEMAX
to a value that matches the needs of
the application. When the actual position following error (
PE
) exceeds
PEMAX
, motion stops. If the motion is stopped when this condition is
detected, the axis is disabled.
During normal operation, occasional occurrences of position error overflow
usually indicates a malfunction of the machine, such as a worn or broken
part, or a need for lubrication. You should set the maximum position error
well outside the boundaries of normal machine operation or nuisance errors
occur when the machine is running.
During installation, position error overflow frequently occurs because the
system is unstable. In this case, the motor runs away even though zero
velocity is commanded. Set
POSITIONERRORMAX
to a reasonably small
value before powering the system up. For example, you might set it to a few
revolutions of the motor (or a few inches or centimeters for linear systems).
This way, if the tuning is unstable, the system is less likely to cause a
problem. Setting
PEMAX
to a very large number prevents the Position Error
Overflow error from detecting an unstable system, and consequently, the
motor is able to run away.
The proportional position loop is the simplest position loop. The next figure
shows a block diagram of a proportional position loop:
As you can see, the velocity command is proportional to the following error.
Large velocity commands need large following error limits. At first, the units
of inches/min/mil may seem confusing. The following error for an
acceleration with a typical proportional loop is shown in the next figure.
The good news about 100% feed-forward is that it eliminates steady-state
following error. The bad news is that the system overshoots when subjected
to acceleration or deceleration. In some cases, this is not an issue because
the system may always transition smoothly, or some overshoot is
acceptable.
M-SS-005-03 Rev
E
71