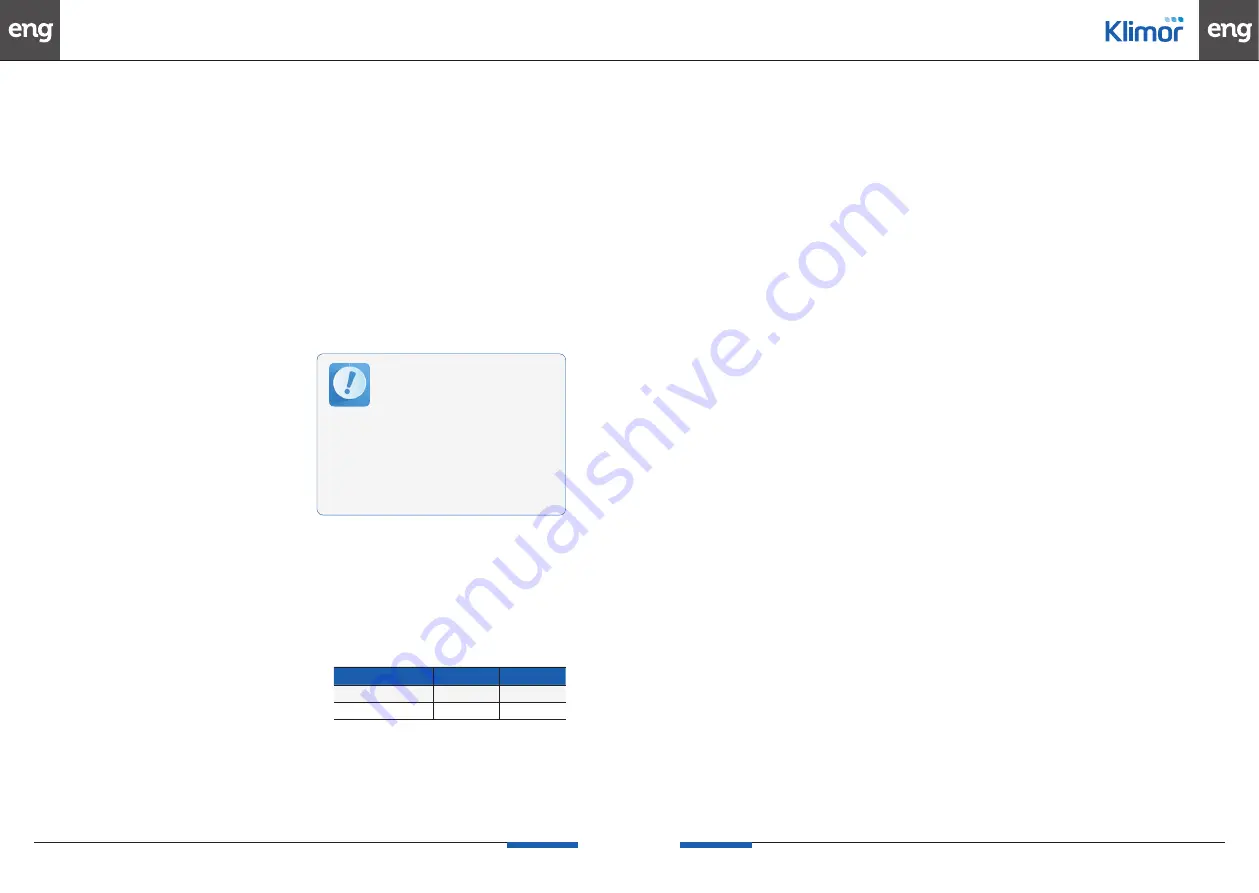
36
37
www.klimor.com
www.klimor.com
MCKT - SUSPENDED MODULAR AIR CONDITIONING AND VENTILATION UNITS
OPERATION AND MAINTENANCE MANUAL
9.3 Heat Exchangers
Water Heater
Heater lamellas should be checked for contamina-
tion at least every four months. When the exchanger
is contaminated, it should be cleaned with a vacuum
cleaner with a soft suction nozzle on the side of air inlet
or blown through with compressed air on the side of
air outlet. It is also possible to wash it with warm wa-
ter and cleaning agent that does not cause aluminium
corrosion.
When filling the installation, it should be remembered
to bleed the exchanger at all times.
Electric Heater
The electric heater should be kept appropriately
clean. Dust settling on the heating elements hampers
heat output, and as a result may cause burnout of the
heating elements and a fire hazard. The condition of
the heating elements should be checked every four
months. They should be cleaned with a vacuum clean-
er with a soft suction nozzle on the side of air inlet or
blown through with compressed air. Wet cleaning is
unacceptable.
Water and Glycol Cooler
Apart from operations similar to those done for the
water heater, the following should be checked: clean
condition of the drop separator, drip tray and perme-
ability of condensate drain and condition of the trap.
If the drop separator is soiled, wash it with warm water
with washing agents.
Before the winter period water should be drained from
the cooler if chilled water is the medium, if the ex-
changer is exposed to direct flow of cold air.
DX Cooling Coil
Maintenance similar to water cooler, allowing for the
following constraint: washing a DX cooling coil with
warm water requires the Freon to be sucked out be-
forehand. Otherwise, Freon pressure may increase,
which may damage the cooling instalation.
Cross-flow Exchanger
The cross-flow exchanger is subject to technical inspec-
tion every four months. Aluminium lamellas get soiled,
and excess soil may accumulate on the plate edges
(down to a depth of 50mm). Before cleaning cross-flow
exchanger sections, the neighbouring sections should
be secured.
Clean with a vacuum cleaner with a soft suction nozzle
on the side of air inlets or blow through with air in the
direction opposite to the airflow in the exchanger. It is
acceptable to wash the lamellas with water and clean-
ing agent that does not cause aluminium corrosion or
to rinse them with a water jet under heavy pressure (for
considerable dirt).
When performing all the operations, care should be
taken so as not to deform the aluminium plates.
If maintenance and cleaning of the exchanger is done
in outdoor temperature below 0ºC, the unit should be
completely dried before restart.
Moreover, the following should be checked during in-
spection:
• operation and cleanness of air dampers,
• condition of the drip tray,
• permeability of condensate drainage (fill the trap with
water).
9.4 MCKT-HPM Heat Pump Module
The cooling unit is an autonomous system fully con-
trolled and supervised by external control system. For
that reason it does not require outside interference. All
works should be done by personnel having appropri-
ate certificated qualifications. All the same, staff can
reduce potential failures by following the unit’s oper-
ation carefully.
Operating the compressor requires ap-
propriate operating parameters of the
cooling oil. For that reason, before first
start-up and following each longer stand-
still of the whole unit (when the switchgear
is not supplied with power), the switchge-
ar should be switched on without allowing
the cooling system to start up. This will
cause the heating element of the com-
pressor casing to switch on and the oil to
warm up. The time necessary for ensuring
appropriate oil parameters is 3h.
The basic parameter that should be taken into account
is the amount and parameters of air flowing through
the cooling system exchangers. Flow adjustment
should ensure minimum amounts of air given in the ta-
bles. The condition of air filters should be looked after.
Their soiling may cause considerable drops in airflow
rate. Monitoring the cooling system may be limited to
checking pressure ranges when the system is in oper-
ation (Table No. 7).
Table No. 7
Test Pressure Ranges for MCKT-HPM
PARAMETER
MIN. [MPa]
MAX.[MPA]
Low Pressure
0.25
0.65
High Pressure
1.1
2.5
9.5 Silencer
The silencer section is fitted with slotted levers filled
with non-flammable mineral wool and they should be
checked for cleanness. The slotted levers are remova-
ble, but they may be cleaned when they are in the unit.
Clean with a vacuum cleaner with a soft suction nozzle.
9.6 Fan
Prior to commencing any works on the unit and when
removing the inspection panels, one should make sure
that the unit has been disconnected from power sup-
ply, the rotor is not turning, the fan motor has cooled
down and that the system has been secured against
accidental start-up.
In case of a fan with a skeleton rotor the following
should be checked:
• whether the rotor is clean (clean with a vacuum cleaner
and clean wet with a mild cleaning agent),
• whether the rotor turns easily,
• whether the rotor is balanced and does not run out,
• whether it has not moved in relation to the nozzle
(dimensions of appropriate slots retained),
• condition of vibration isolators,
• all mounting bolts (if necessary they should be tight-
ened).
In case of an electric motor the following should be
checked:
• correct fixing of all mechanical and power connec-
tions,
• the quality of wires and insulations – if there is no dis-
colouring,
• insulation resistance of motor winding,
• whether there are no grease leaks,
• casing soiling (clean dry with a soft brush or blow
through with compressed air).
10. Test Measurements
Subsequent to maintenance operations, the unit’s following
operating parameters should be measured:
• temperature and humidity
of the air before and
after the unit’s devices responsible for processing air
temperature and humidity,
• temperature
of heating and cooling mediums,
• total
performance and pressure
of fans,
• power
consumed by power receivers.
Maintenance and test measurements have to be re-
ported in relevant documents belonging to the unit.
11. Occupational Safety and Health
(OSH) Manual
1. Installation and first start-up of the units shall be done
in conditions provided for in applicable regulations,
and in particular in regulations concerning operation
of electric appliances.
2. Connecting the unit to a protective installation shall be
a condition for switching on the power supply.
3. Power supply shall be switched off prior to repair and
maintenance operations.
4. Operation of the unit without any of the inspection
panels shall be unacceptable.
5. Servicing, repair and maintenance of the units may be
done only by personnel having appropriate qualifica-
tions confirmed by a relevant certificate provided for
by a competent ministry in a regulation concerning
qualifications of personnel employed to maintain pow-
er appliances.
6. Protective equipment ensuring safe maintenance
should be available at the maintenance post.
12. Information regarding Units in MCKHT
hygienic version
Units in MCKHT hygienic version have been built on the
basis of MCKT units and allowing for the recommendations
included in the DIN 1946-4 standard.
12.1 Lighting in Section
Hygienic units are fitted with LED (12V) type of lighting
in the secondary filters and fan section. Lighting comes
from a LED strip. A wire runs from the lighting to the
terminal box mounted on the celling. If the system in-
cludes two lighting blocks, the wires run to a joint ter-
minal box. The contractor responsible for automation
has to allow for connecting the lighting in the control
system.
12.2 Inspection Openings (Portholes)
Inspection openings – portholes 200mm in diameter –
have been mounted in section covers in which there
is lighting.
They allow, without switching off the unit – assessing
the contamination degree of the interior and its fittings
as well as observation of the work of the unit’s particu-
lar elements.
12.3 Filtration Materials
1st and 2nd degree filtration materials are non-hygro-
scopic with attestations applicable to the health service.
12.4 Trays
Trays in hygienic version units – under the cooler and
drop separator of the cross-flow exchanger – are made
of stainless steel.
12.5 Casing
The unit’s casing (inside and outside) is made of RAL
9010 white-coated galvanised steel.
All connective elements (rivets, bolts etc.) are made of
stainless steel.
The contact edges of metal sheet plates are sealed with
colourless sanitary silicone.
All the materials used to make the unit and the insert ele-
ments are resistant to commonly used disinfecting agents.