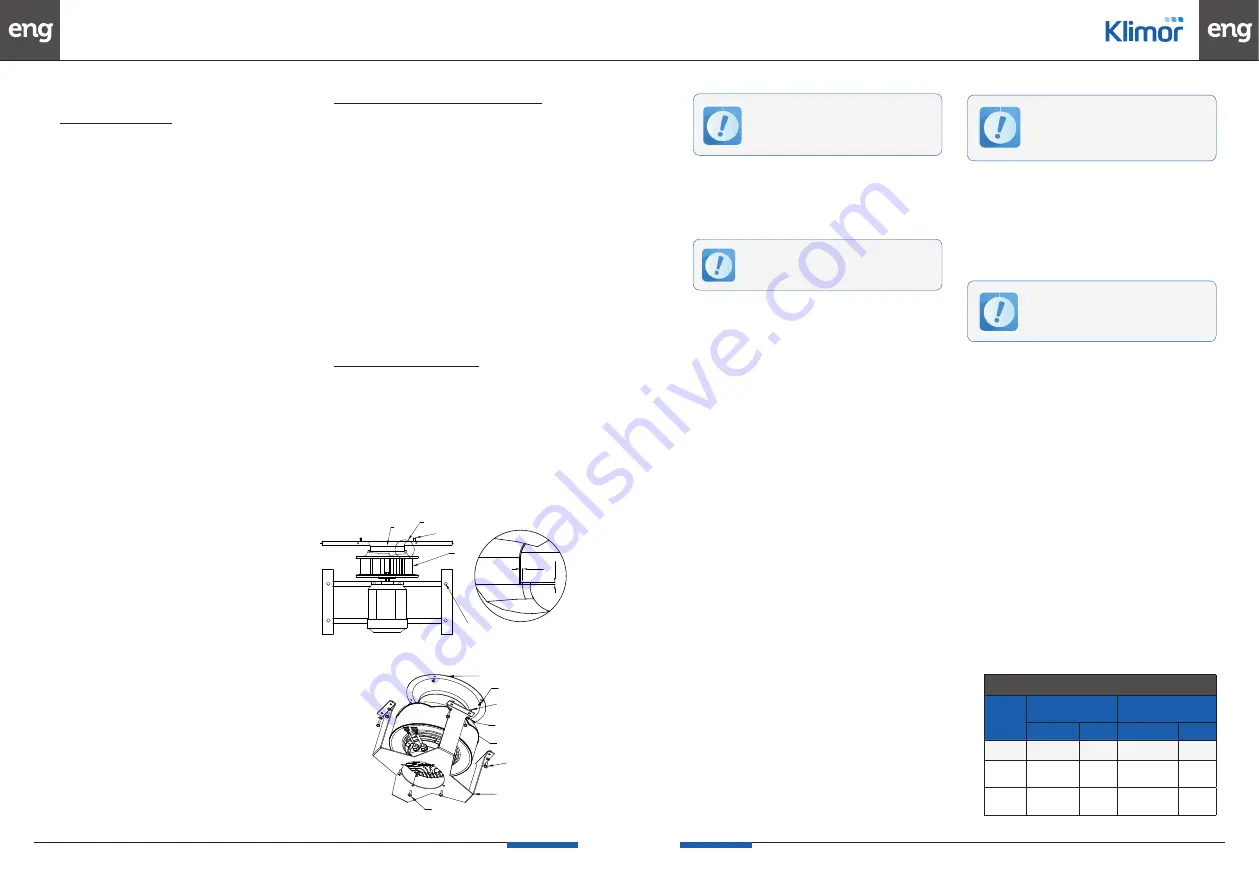
34
35
www.klimor.com
www.klimor.com
MCKT - SUSPENDED MODULAR AIR CONDITIONING AND VENTILATION UNITS
OPERATION AND MAINTENANCE MANUAL
7.7 Heat Pump Module
First start-up of the system:
• Carry out wiring of the unit according to attached dia-
grams,
• Put the unit together and connect it to the system of air
ducts,
• Properly set the actuators on bypass damper and heat
exchanger damper
• Set the value in cross-flow h.e. pressure guage.
• Programme the variable frequency drives for the fans,
• Programme the variable frequency drive for the cooler
compressor,
• Select application depending on the type of heater,
• Adjust the unit’s airflow rate for the unit’s nominal per-
formance. The airflow rate both for intake and outlet has
to be within a range acceptable for a given unit. Stand-
ard airflow rate should be set with the counter-current
exchanger bypass damper closed. When adjusting the
unit’s airflow rate, the circuit breaker responsible for the
compressor’s operation should be disconnected.
• In case of reheater configuration, reduced airflow rate
should be set appropriate for the defrost mode. For
MCKT1-HPM it is 600 m
3
/h, while for MCKT2-HPM it is
1000 m
3
/h. Adjustment must be done with the coun-
ter-current exchanger bypass damper open. When
adjusting the unit’s airflow rate, the circuit breaker
responsible for the compressor’s operation should be
disconnected.
• Prior to first start-up of the cooling system one should
wait 3 h with switchgear power supply switched on and
fans switched off. This will allow the heating element of
the compressor casing to heat up the cooling oil appro-
priately.
• Switch on the compressor circuit breaker and start the
system. Move on to the screen displaying the pressure in
the cooling system. If after starting the compressor the
pumping pressure does not rise and the suction pres-
sure does not drop considerably, this may evidence that
the compressor’s power supply has not been connected
properly. Incorrectly connected phases cause the motor
to rotate in the wrong direction. After any two phases
have been swapped the compressor will work properly.
• The ratio of the amount of air at the intake to the amount
of air at the outlet must be within the range from 0.5 to 1.4.
• Following a correct test start, the assumed operation pa-
rameters may be set. The unit is fully ready for operation.
Detailed information concerning the above activities is
available in OMM re. control system.
7.8 Fan Section
Prior to start, it is necessary to make a thorough inspec-
tion of the fan section module. Make sure there are no
objects in the vicinity of the fan that could enter the
inside of the fan rotor.
Check if the rotor turns without resistance (e.g. adja-
cent elements scraping against one another).
Prior to starting the motor it is necessary to check:
• the motor’s power connection (the voltage of the power
supply network has to be the same as the voltage on the
motor’s nameplate,
• the condition of the earth wire between elements of the
fan section and the unit’s casing,
• the power cables inside the module must be firmly fixed
to the elements of the construction so as to prevent
them from getting close to movable elements (rotor),
• the direction of the rotor’s revolutions (to be checked by
impulse start of the motor) has to comply with the label-
ling on its casing. In case of non-compliance the direc-
tion of rotating supply power phases should be shifted
by swapping any two phases in the terminal box,
• setting of the inverters for fan start-up/warm-up time
(should be a minimum of 30 sec.).
In order for the rotor to be able to rotate freely, make
sure the slot between the rotor and the outlet nozzle
is appropriate.
The slot can be adjusted as follows:
• loosen 6 bolts and move the outlet nozzle vertically,
• move the rotor horizontally together with the motor,
tray, load-bearing channel bars, vibration isolators, by
loosening 4 bolts.
The slot size should be about 2.5mm. The distance
the rotor is pulled onto the outlet nozzle should be
2.5mm.
The slot should always be checked following transport
of the device and its installation in the appropriate op-
erating position.
2,5
2,5
A
A
NOZZLE
ROTOR
NOZZLE POSITION
ADJUSTMENT BOLT
UNIT
POSITION
ADJUSTMENT
BOLT
DRAWING 19:
Adjustment of the slot between the rotor and outlet nozzle.
RIVET 4
BOLT M6x16
NOZZLE
FAN R3G
HANDLE
SCREW M6x16
BLINT RIVET NUT M6
SPRING WASHER
DRAWING 20:
Assembly of fan with EC motor
Continuous operation of the device with
the inspection panels off is prohibited.
Having made all the checks, the unit’s inspection panels
should be closed and the unit can be started up.
8. Start-up of the Unit
Only qualified assembly personnel may carry
out start-up operations.
The recommended time setting on the inverters for start-up/
warm-up of the fan is a minimum of 30s.
Start-up of the unit should be commenced with the adjustment
air damper shut at the inlet to the unit. Otherwise, with the air
damper wide open, the motor may be overloaded resulting in
durable damage. After the motor has been switched on, the
adjustment damper should be opened gradually, and the fol-
lowing parameters should be regularly monitored:
• the value of the intensity of the power consumed by the
motor,
• the amount of air pumped in the installation (airflow rate).
If the unit is fitted with an control system, the opening of
the air damper by the servomotor should be controlled. As
a rule, the intensity of the power consumed by the motor
should not be greater than the rated value, given the assumed
available amount of air and pressure.
When the fan is in operation, one should listen out for any wor-
rying, unnatural metallic noises or whether the unit’s vibrations
are not too heavy.
After 30 minutes the unit should be switched off and the follow-
ing fittings should be inspected:
• filters (if they have not been damaged),
• drip trays and traps (appropriate condensate drainage),
• fan section (temperature of motor and fan bearings –
also the slot between the nozzle and the fan rotor).
In units with secondary filters, start-up is recommended
without this filters cartridge installed. After start-up, it is
recommended to clean preliminary filters.
The antifreeze thermostat should be checked for correct op-
eration in temperature of air flowing into the water heater of
not much less than the thermostat setting – e.g. 1-2ºC. Then,
during operation of the unit the thermostat should be checked
for correct operation by shutting the inflow of heating water for
a moment.
Assessment of the correct operation of the MCKT unit and the
air conditioning and ventilation installation (system validation)
may be issued after careful adjustment of the operation param-
eters and after obtaining correct air parameters in the premises,
assumed by the design.
The above-mentioned check operations should be done before
the MCKT unit is commissioned.
When the MCKT unit is started up for the first
time, the Assembly and Start-up Report sho-
uld be filled in. The Report is in the form of an
annex to the Warranty and in p.14 of this OMM
9. Operation and Maintenance
The MCKT unit is designed for continuous operation. Peri-
odic overhauls of the unit are warranty required. Filters are
to be renewed by the user himself.
Operation and maintenance works have been present-
ed below.
Maintenance and servicing operations can
only be carried out when the unit is off and
not working.
9.1 Air Dampers
Air dampers, especially on the side of outside air, must
be kept clean. Excess contamination may cause the
blades to remain ajar or the rotating mechanisms to
seize.
Air dampers may be cleaned with an industrial vacu-
um cleaner with a soft suction nozzle, blown through
with compressed air or washed with water under
pressure and cleaning agents that do not cause alu-
minium corrosion.
9.2 Filters
MCKT units make use of G4 or M5 sectional filters
50mm in thickness as preliminary filters and M5÷F9
bag filters as secondary filters.
Filters should be renewed when the admissible pres-
sure drop on the filters has been exceeded (Table No.
6) or according to visual inspection. The unit must be
switched off during filter renewal. The class of new fil-
ters has to correspond to the class of the used filters.
During filter renewal also the filtration section has to
be cleaned.
Operation of the units is allowed only with the filters on.
Table No. 7
Filter Dimensions
MCKT FILTER DIMENSIONS AND SIZES
Unit Size
G4/M5 Preliminary
Cassete Filter
M5÷F9
Secondary Bag Filter
W x H
Amount
W x H
Amount
MCKT01
610x305
1
592x287
1
MCKT02
915x305
1
592x287
287x287
1
MCKT03
915x425
1
592x407
287x407
1