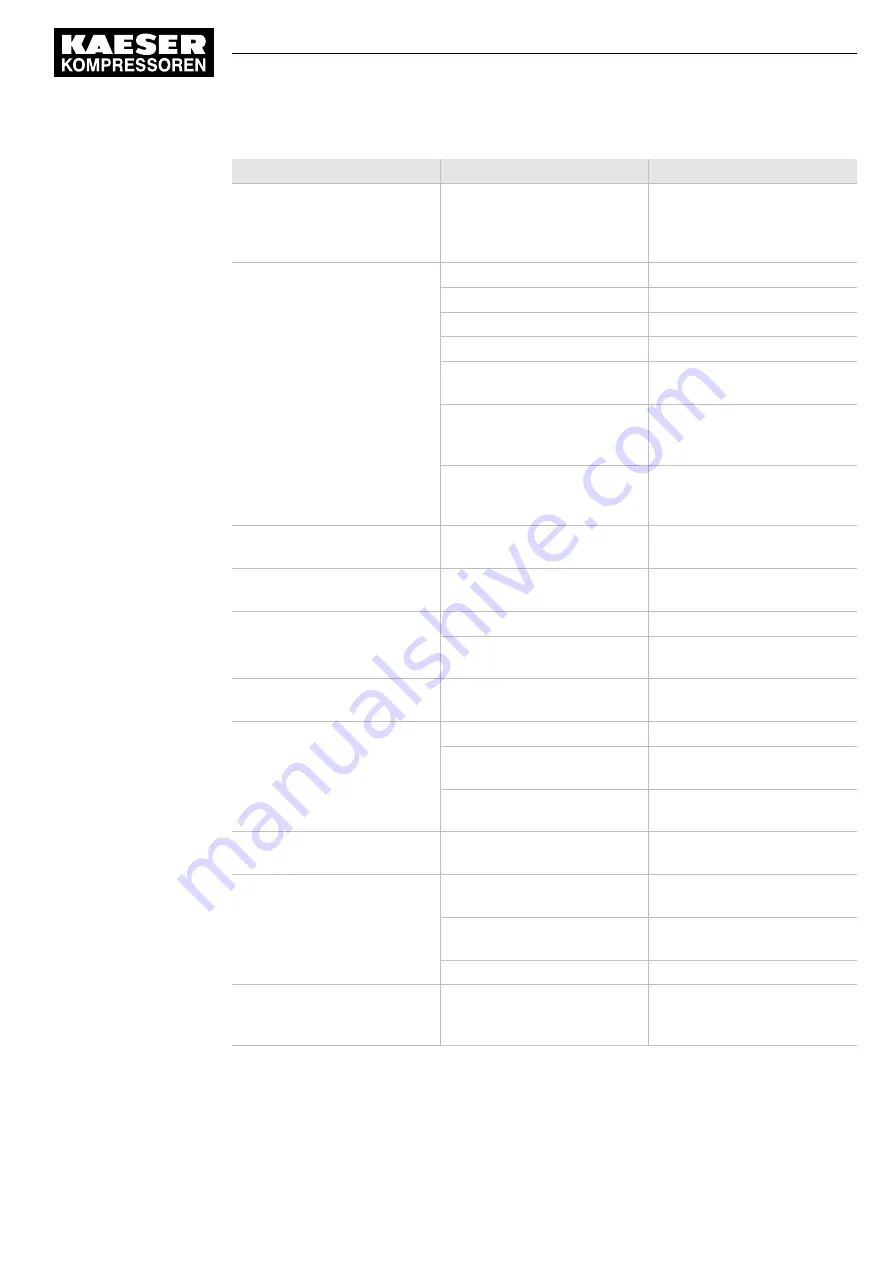
Fault
Possible cause
Action
Motor overload protection trips
out after a long time.
Current too high because of low
supply voltage.
Check power supply cable con‐
ductor cross-sections. Check
and tighten connection termi‐
nals.
The machine runs continuously
but maximum pressure is not
reached.
Air filter clogged.
Clean or change the air filter.
Valve plate leaking air or coked. Check or clean the valve plate.
Outlet valve reed broken.
Replace valve plate.
Machine leaks air.
Seal leak or replace leaking part.
Leakage from an air consumer
connected to the air system.
Check possible leakage points.
The air demand is greater than
the machine's air delivery ca‐
pacity.
Use a larger machine.
Solenoid valve blows off contin‐
uously. Solenoid coil is defec‐
tive.
Change the solenoid valve.
Machine cuts in and out too of‐
ten.
External air receiver filled with
condensate.
Tapp ut kondensat.
Machine switches off.
The oil level monitor (option C5)
has triggered.
Top up the oil.
Air leaks from the user's pres‐
sure switch while the machine is
running.
Defective switch diaphragm.
Replace the pressure switch.
The venting valve is not closing. Clean or replace the venting
valve.
Whistling sound from the cylin‐
der head.
Remove the screws. Gasket de‐
fective.
Tighten screws Replace gasket.
The pressure relief valve blows
off before the cut-out pressure is
reached.
Pressure switch incorrectly set. Check pressure switch setting.
Valve spring defective.
Replace the pressure relief
valve.
Dirt or foreign bodies on the
valve seat.
Let the pressure relief valve blow
off briefly.
Pressure relief valve on the air
cooler blows off prematurely.
Cooler clogged. Cooler pipe
blocked with scale.
Clean the radiator.
Machine uses too much oil.
Viscosity too low.
Fill with oil specified in the ser‐
vice manual.
Crankcase venting defective.
Clean or renew the crankcase
vent.
Piston rings worn or broken.
Contact KAESERservice.
Piston rings already worn or
damaged after only a short op‐
erating period.
Dirty oil.
Fit finer air inlet filter.
Tab. 35 Faults and remedies
9
Fault Recognition and Rectification
9.2
Alarms
No.: 9_5753_04 E
Assembly and operating manual 2-stage piston compressor
EPC-2-G
49
Содержание EPC-2-G Series
Страница 2: ...Original instructions KKW PEPC 1 04 en SBA KOLBEN AGGREGAT 2 STUFIG ...
Страница 6: ...Contents iv Assembly and operating manual 2 stage piston compressor EPC 2 G No 9_5753_04 E ...
Страница 10: ...List of Tables viii Assembly and operating manual 2 stage piston compressor EPC 2 G No 9_5753_04 E ...