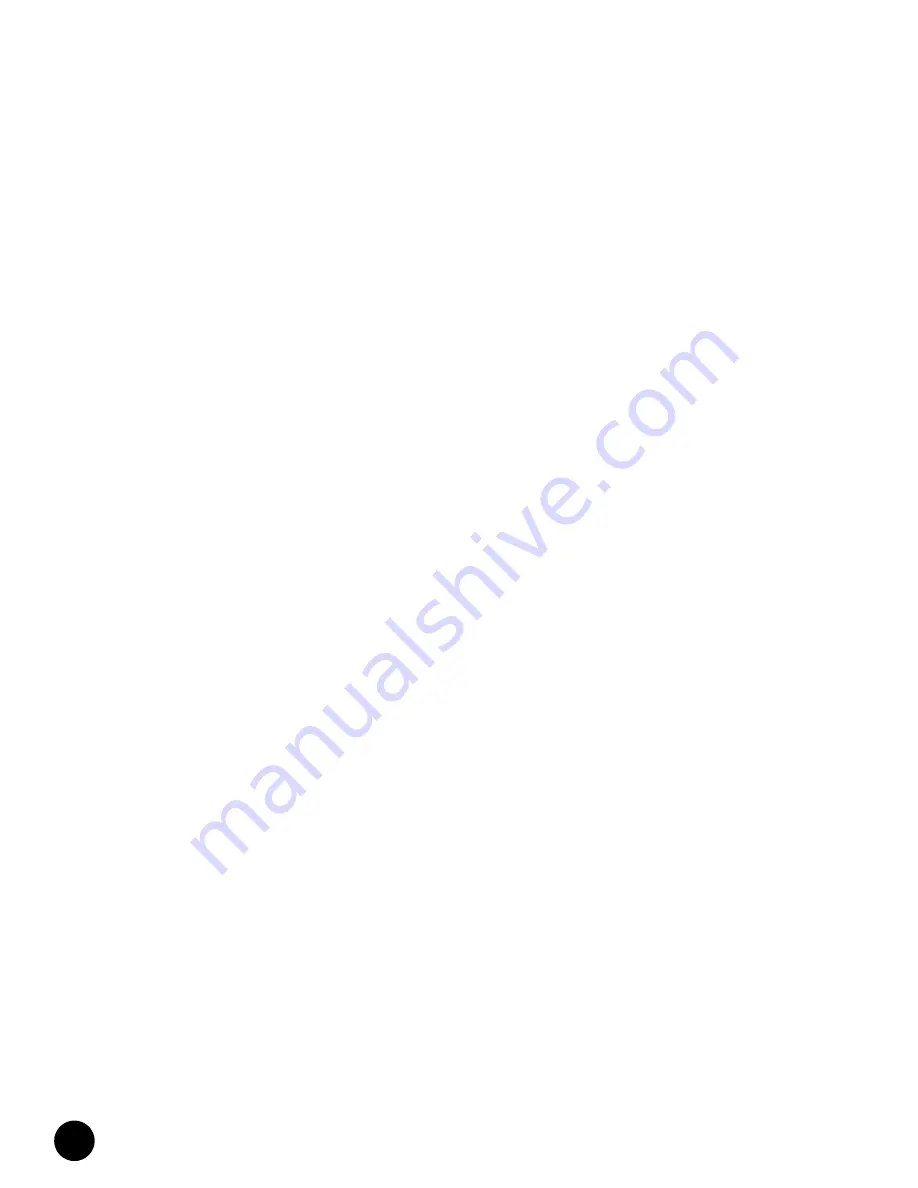
G10 CMTS Hardware Overview
•
•
•
•
•
•
•
•
•
•
•
•
•
•
•
•
•
•
•
•
•
•
•
•
•
•
•
•
•
•
•
•
•
•
•
•
•
•
•
•
•
•
•
•
•
•
•
•
•
•
•
•
•
•
•
•
•
•
JUNOSg 3.0 G10 CMTS Hardware Guide
16
Following is a brief explanation of each feature shown in Figure 4 through Figure 7:
Front Features
!
DOCSIS Module—Module that contains the Broadband Cable Processor ASIC and resides
between the network-side interface (NSI) and the hybrid fiber/coax (HFC) interface.
!
NIC Module—Module that provides the Gigabit Ethernet interface and the Fast Ethernet
switching functions for the network-side interface.
!
Chassis Control Module—Module that performs management and monitoring functions.
!
Module ejector rail—Rail into which a module’s ejector tabs fit when a module is
installed in a slot.
!
ESD strap connector—Location where you can insert an ESD ground strap.
!
Air intake—Slotted openings along the front (removable) and sides of the chassis where
air is drawn into the chassis for cooling the installed modules and power supplies.
!
Air intake faceplate—Slotted removable panel that covers the two front fan trays.
!
Air intake faceplate clip—Retainer clip used to mount the air intake faceplate.
!
Front fan tray—Fan assembly that forces air upward through the front of the chassis.
!
Front fan tray LED—LED that shows the status of the front fan tray.
!
Power supply ejector rail—Rail into which the power supply ejector tabs fit when a
power supply is installed in a bay.
!
Midplane—Passive electrical interconnecting device for all modules in the chassis.
!
Air management module—Module installed in an unused module slot to redirect the air
flow through the chassis and to reduce EMI emissions.
!
Card guide—Used to align a module or power supply while it is being inserted into its
slot or bay.
!
Power supply—Converts AC or DC power supplied through the power transition modules
into the DC voltages required by the modules.
!
Power supply faceplate—Panel along the top of the chassis that covers the power
supplies.
!
Power supply faceplate clip—Retainer clip used to mount the power supply faceplate.
!
Power supply bay—Chassis bay in which a single hot-swappable power supply is
inserted.
!
Power supply filler panel—Panel covering an empty power supply bay.
!
Cable channel—Channel through the top of the chassis that is used to route the network
cables from the rear of the chassis to the front.
!
Cable guide—Guide used to route the network cables between the cable channel and the
lower opening in the power supply faceplate.
Содержание G10 CMTS
Страница 8: ... JUNOSg 3 0 G10 CMTS Hardware Guide viii ...
Страница 18: ... JUNOSg 3 0 G10 CMTS Hardware Guide 2 ...
Страница 34: ...G10 CMTS Hardware Overview JUNOSg 3 0 G10 CMTS Hardware Guide 18 ...
Страница 46: ...DOCSIS Module JUNOSg 3 0 G10 CMTS Hardware Guide 30 Figure 12 DOCSIS Module Front Panel HotSwap ...
Страница 55: ... Hardware Component Overview Chassis Control Module 39 Figure 15 Chassis Control Module Front Panel Eth0 ...
Страница 72: ...Chassis Rear Modules JUNOSg 3 0 G10 CMTS Hardware Guide 56 Figure 21 Hard Disk Module Rear Panel C O M Eth ...
Страница 82: ... JUNOSg 3 0 G10 CMTS Hardware Guide 66 ...
Страница 112: ...Rack Mounting JUNOSg 3 0 G10 CMTS Hardware Guide 96 Figure 25 Air Flow Through Chassis ...
Страница 116: ...Rack Mounting JUNOSg 3 0 G10 CMTS Hardware Guide 100 Figure 29 Rack Fully Populated with Three G10 CMTS Chassis ...
Страница 118: ...Install Power Supplies JUNOSg 3 0 G10 CMTS Hardware Guide 102 Figure 30 Power Supply Installation 1 2 ...
Страница 138: ...Connect to Power Sources JUNOSg 3 0 G10 CMTS Hardware Guide 122 Figure 39 DC Power Transition Module ...
Страница 148: ... JUNOSg 3 0 G10 CMTS Hardware Guide 132 ...
Страница 156: ...Upstream RF Measurement JUNOSg 3 0 G10 CMTS Hardware Guide 140 ...
Страница 188: ... JUNOSg 3 0 G10 CMTS Hardware Guide 172 ...
Страница 196: ...Radio Frequency RF Specifications JUNOSg 3 0 G10 CMTS Hardware Guide 180 ...
Страница 202: ...EIA Channel Plans JUNOSg 3 0 G10 CMTS Hardware Guide 186 ...
Страница 203: ... 187 Part 5 Index Index on page 189 ...
Страница 204: ... JUNOSg 3 0 G10 CMTS Hardware Guide 188 ...
Страница 209: ... Index 193 Index V ventilation 69 89 95 101 124 161 162 167 video servers 7 voltage power supply 27 ...
Страница 210: ... Index JUNOSg 3 0 G10 CMTS Hardware Guide 194 ...