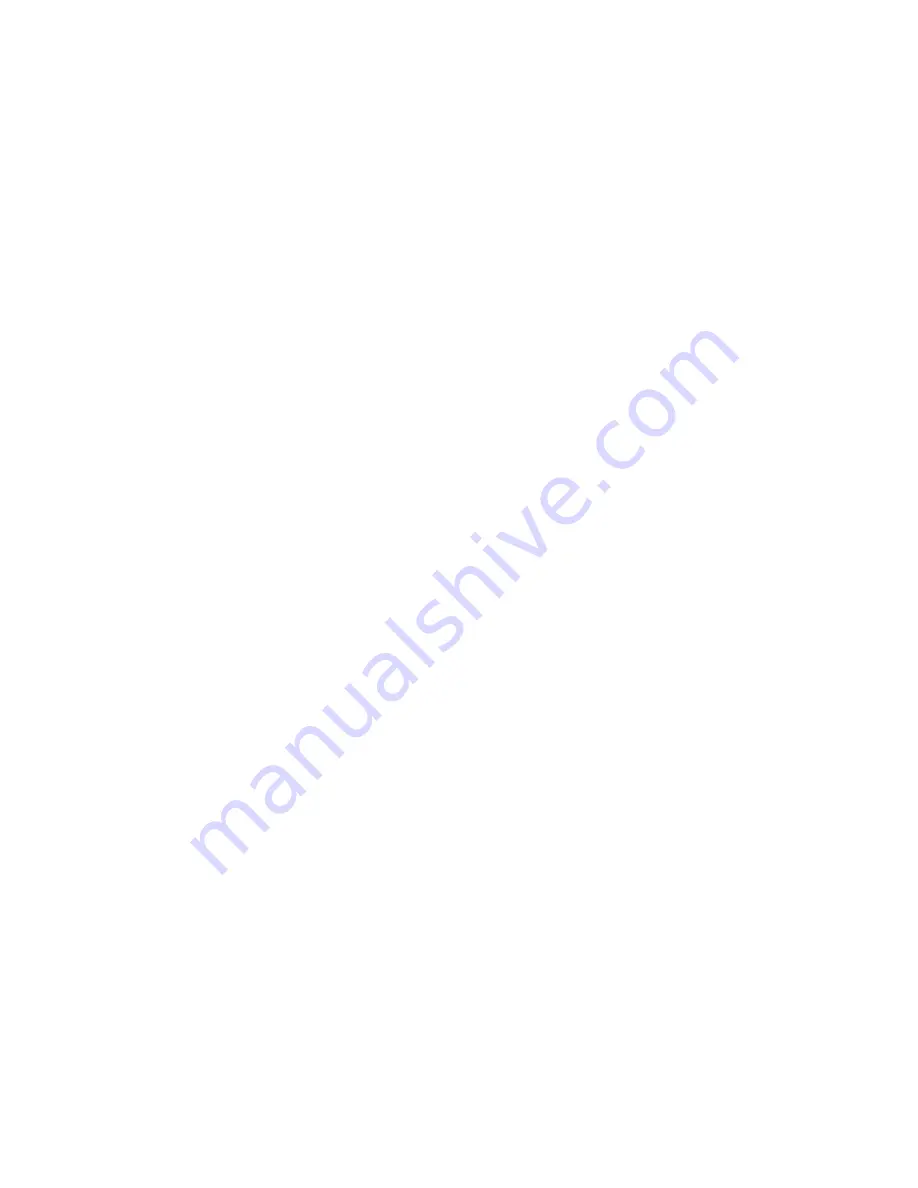
0
708
.GB
F 18
6.2
During decommissioning:
Every 2 months:
– Charge the battery (see Chapter D).
M
Battery powered trucks:
The battery must be charged at regular intervals to avoid depletion of the battery
through self-discharge. The sulfatisation would destroy the battery.
6.3
Restoring the truck to operation after decommissioning
– Thoroughly clean the truck.
– Lubricate the truck in accordance with the lubrication schedule (see Chapter F).
– Clean the battery, grease the terminals and connect the battery.
– Charge the battery (see Chapter D).
– Check transmission oil for condensed water and replace if necessary.
– Check hydraulic oil for condensed water and replace if necessary.
– Start up the truck (see Chapter E).
Z
Battery powered trucks:
If there are switching problems in the electrical system, apply contact spray to the
exposed contacts and remove any oxide layers on the contacts of the operating
controls by applying them repeatedly.
F
Perform several brake tests immediately after re-commissioning the truck.
0
708
.GB
F 18
6.2
During decommissioning:
Every 2 months:
– Charge the battery (see Chapter D).
M
Battery powered trucks:
The battery must be charged at regular intervals to avoid depletion of the battery
through self-discharge. The sulfatisation would destroy the battery.
6.3
Restoring the truck to operation after decommissioning
– Thoroughly clean the truck.
– Lubricate the truck in accordance with the lubrication schedule (see Chapter F).
– Clean the battery, grease the terminals and connect the battery.
– Charge the battery (see Chapter D).
– Check transmission oil for condensed water and replace if necessary.
– Check hydraulic oil for condensed water and replace if necessary.
– Start up the truck (see Chapter E).
Z
Battery powered trucks:
If there are switching problems in the electrical system, apply contact spray to the
exposed contacts and remove any oxide layers on the contacts of the operating
controls by applying them repeatedly.
F
Perform several brake tests immediately after re-commissioning the truck.
Содержание EKS 410
Страница 1: ...EKS 513 515 EKS 410 Operating instructions 52025221 EKS 410 513 515k 515 G 12 03 07 08...
Страница 3: ...0108 GB...
Страница 7: ...0708 GB I 4...
Страница 9: ...0506 GB 2...
Страница 11: ...1004 GB A 2...
Страница 16: ...B 5 0708 GB Ast Wa h15 h10 h3 h9 h7 h6 h1 h4 b2 l1 l2 m2 R b5 l...
Страница 23: ...0708 GB B 12...
Страница 35: ...1004 GB D 6 21 23 22 25 24 19 18 20 20 24 22...
Страница 37: ...1004 GB D 8...
Страница 67: ...0206 GB E 30...
Страница 87: ...0708 GB F 20...