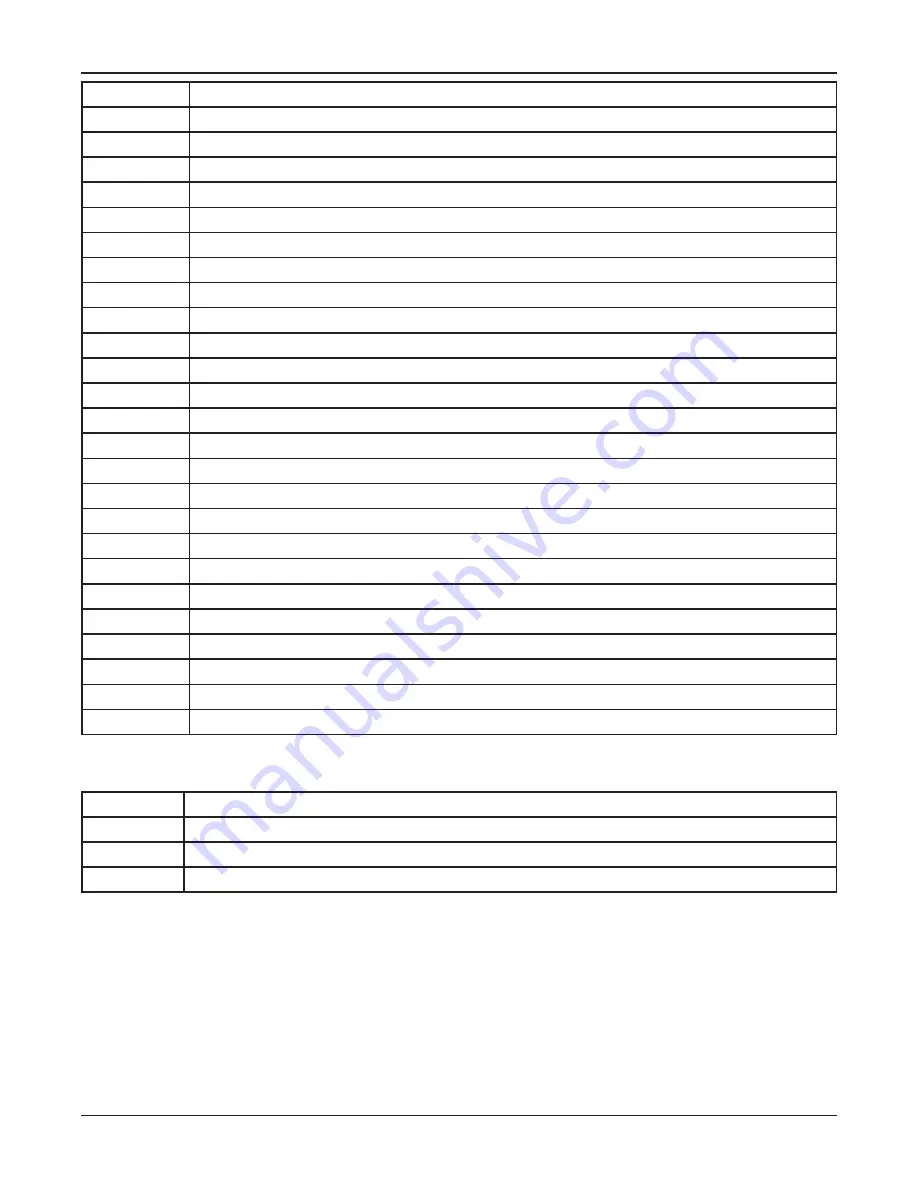
Chapter 2 Diagonostic Codes
2-19
4A
Power clamp
4B
Incremental potentiometer
4C
Rim light
61
Balancing algorithm
62
Balancing calibration
63
Behind the spokes placement
64
<not used>
65
Optimisation
66
Measurement control
81
Command language (Commands coming from the UI)
82
Calculator
83
Message Server (Message service from BK to UI)
84
Message Server (User messages from BK to UI)
85
Sleep command
86
Balancing Kernel : Test state machine (eg self-test during start-up)
A1
Event system
A2
User management
A3
State machine
A4
complex data type
A5
Persistent objects
A6
Pipe device
A7
Power on time counter (-> time stamp for error recording)
A8
Counter for total spins / in service-, in user mode
C1
Self test
C2
User interface
C3
User interface
2.8.3 PRIORITy ID
prior. ID
Description
0
Critical error (will be recorded in user mode)
1
Warning message
2
For information only
Содержание EEWB304B
Страница 1: ...WHEEL BALANCER Service Manual EEWB502B C EEWB503B EEWB304B ...
Страница 56: ......