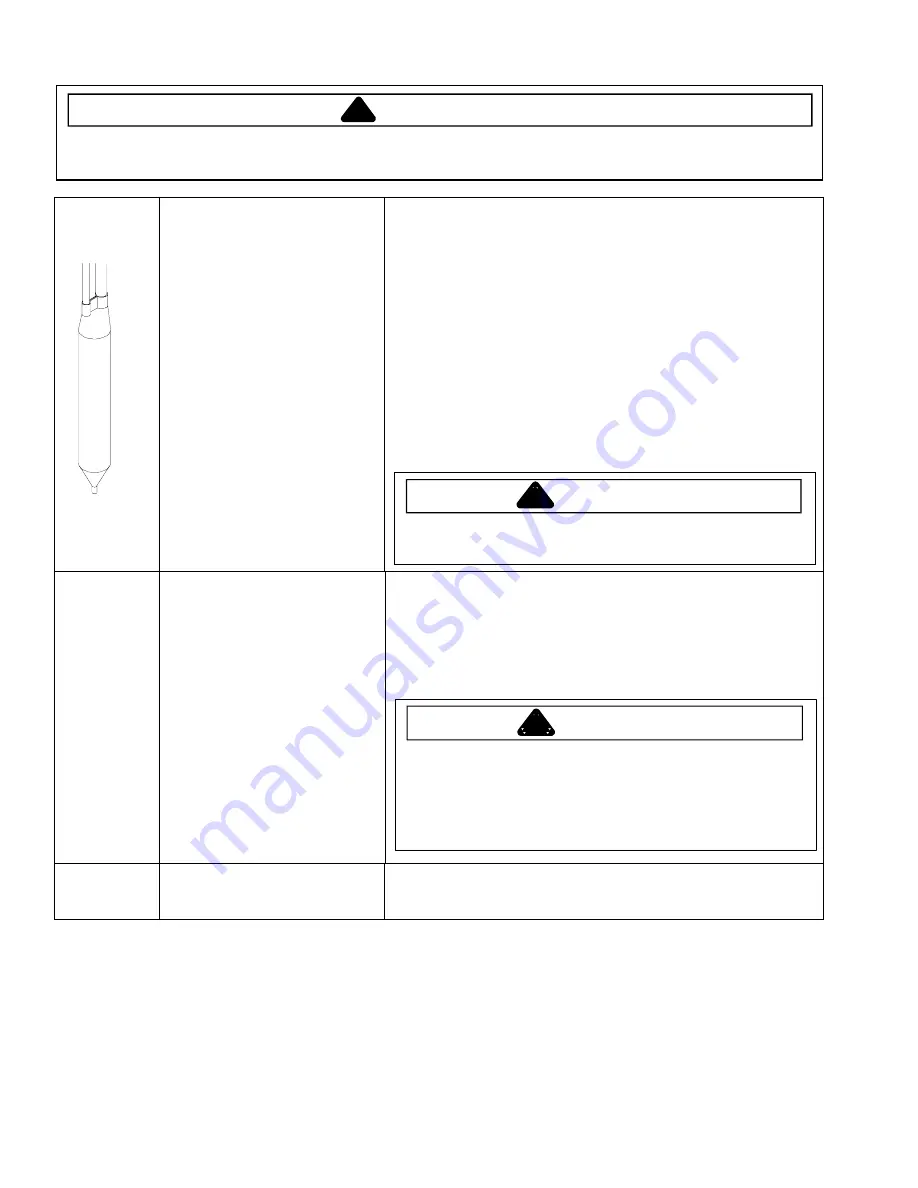
Component Testing
!
WARNING
To avoid risk of electrical shock, personal injury, or death, disconnect electrical power source to unit, unless test
procedures require power to be connected. Discharge capacitor through a resistor before attempting to service.
Ensure all ground wires are connected before certifying unit as repaired and/or operational.
16021730 Rev. 0
6
Drier
Drier is placed at post condenser loop
outlet and passes liquefied refrigerant to
capillary.
Desiccant (20) 8 x 12 4AXH - 7 M>S> -
Grams
Drier must be changed every time the system is opened for testing or
compressor replacement.
NOTE:
Drier used in R12 sealed system is not interchangeable with
drier used in R134a sealed system. Always replace drier in R134a
system.
Before opening refrigeration system, recover HFC134a refrigerant for safe
disposal.
1. Cut drier out of system using the following procedure. Do not unbraze drier.
2. Applying heat to remove drier will drive moisture into the system.
3. Score capillary tube close to drier and break.
4. Reform inlet tube to drier allowing enough space for large tube cutter.
5. Cut circumference of drier 1 ¼" below condenser inlet tube joint to drier.
6. Remove drier.
7. Apply heat trap paste on post condenser tubes to protect grommets from high
heat.
8. Unbraze remaining part of drier. Remove drier from system.
9. Discard drier in safe place. Do not leave drier with customer. If refrigerator is
under warranty, old drier must accompany warranty claim.
Evaporator
Inner volume of evaporator allows liquid
refrigerant discharged from capillary to
expand into refrigerant gas.
Expansion cools evaporator tube and fin
temperature to approximately -20
°
F
transferring heat from freezer section to
refrigerant.
Passing through suction line to
compressor, the refrigerant picks up
superheat (a relationship between
pressure and temperature that assures
complete vaporization of liquid
refrigerant) as the result of capillary tube
soldered to suction line.
Refrigerant gas is pulled through suction
line by compressor, completing
refrigeration cycle.
Test for leaks in evaporator with electronic leak detector or with soap solution.
Compressor oil is circulated with refrigerant; check for oil when checking for
leaks.
For minute leaks
1. Separate evaporator from rest of refrigeration system and pressurize
evaporator up to a maximum of 140 PSI with a refrigerant and dry nitrogen
combination.
2. Recheck for leaks.
Evaporator defrost
heater
Activated when Main control board
activates defrost mode or when forced in
Diagnostic mode.
Check resistance across heaters.
If resistance heater is open and should be replaced.
In diagnostic mode test # 11 Energize heater (the defrost system should draw
about 3 amps).
WARNING
!
To avoid death or severe personal injury, cut drier at correct location.
Cutting drier at incorrect location will allow desiccant beads to scatter. If
spilled, completely clean area of beads.
WARNING
!
To avoid severe personal injury or death from sudden erruption of
high pressurres gases, observe the following:
•
Protect against a sudden eruption if high pressures are required
for leak checking.
•
Do not use high pressure compressed gases in refrigeration
systems without a reliable pressure regulator and pressure relief
valve in the lines.
Содержание Luxury Series
Страница 13: ...13 16021730 Rev 0 Refrigerant Flow Side by Side Refrigerant Flow Diagram ...
Страница 14: ...16021730 Rev 0 14 Cabinet Air Flow Side by Side Cabinet Air Flow Diagram ...
Страница 16: ...16021730 Rev 0 16 Water Valves Diagram Bottom View Back View Primary Valve Secondary Valve Filter Head Bypass ...
Страница 46: ...A 1 ...
Страница 72: ...B 1 Appendix B ...