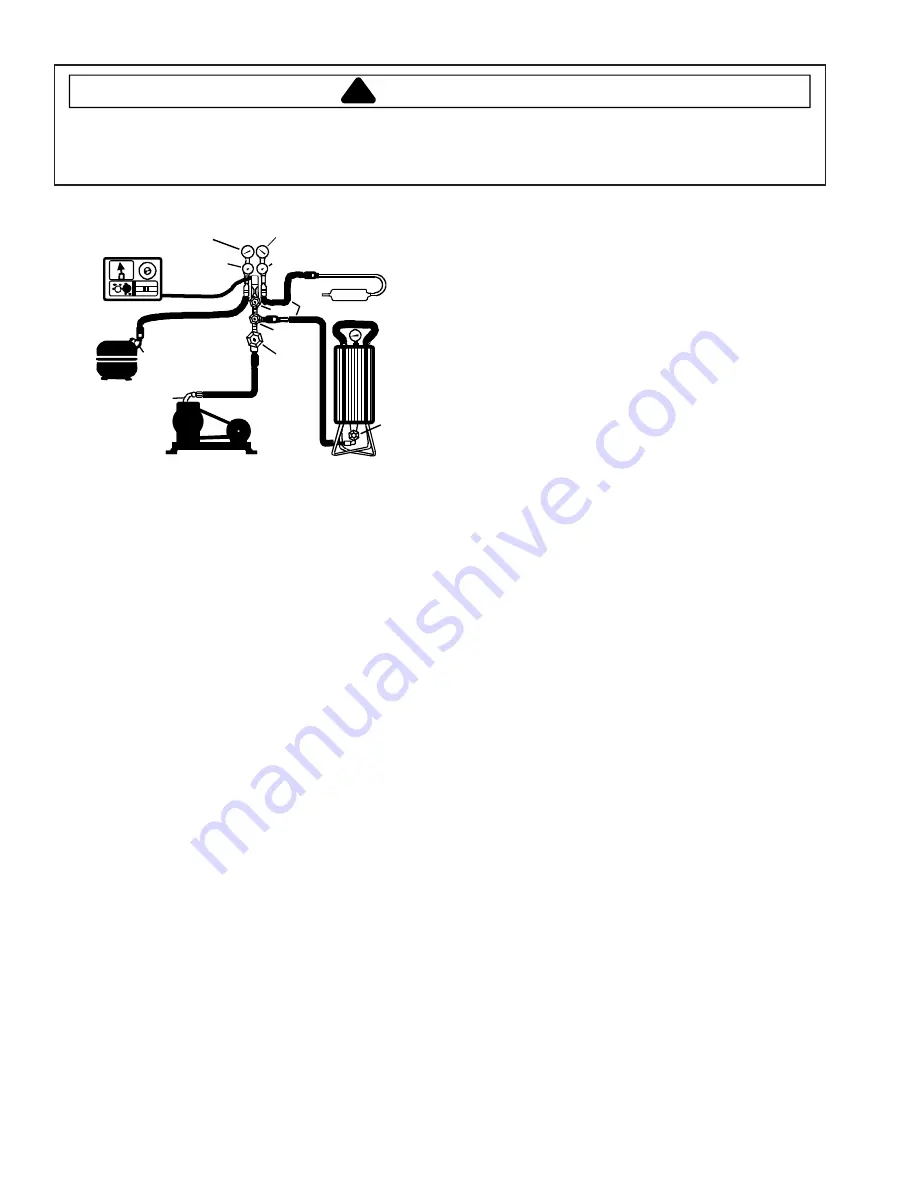
16021730 Rev. 0
10
Service Procedures
!
WARNING
To avoid risk of electrical shock, personal injury, or death, disconnect electrical power source to unit, unless test
procedures require power to be connected. Discharge capacitor through a 10,000 ohm resistor before attempting
to service. Ensure all ground wires are connected before certifying unit as repaired and/or operational.
Vacuum Pump
.6 cm Copper
Tubing
Compressor
Compressor
Process
Tube
Charging Hose
Thermistor
Vacuum Gauge
Low Side Gauge
E
Valve
B
D
Valve
High Side Gauge
Charging Hose
Drier/Process Tube
F
Valve
Charging
Cylinder
C
A
Equipment Setup For Evacuation And Charging
5. After compound gauge (low side) drops to
approximately 29 inches gauge, open valve C to
vacuum thermocouple gauge and take micron reading.
NOTE
: A high vacuum pump can only produce a good
vacuum if oil in pump is not contaminated.
6. Continue evacuating system until vacuum gauge
registers 600 microns.
7. At 600 microns, close valve A to vacuum pump and
allow micron reading in system to balance. Micron
level will rise.
If in 2 minutes, micron level stabilizes at 1000
microns or below, system is ready to be charged.
If micron level rises above 1000 microns and
stabilizes, open valve A and continue evacuating.
If micron reading rises rapidly and does not stabilize,
a leak still exists in system.
Close valve A to vacuum pump and valve C to
vacuum gauge. Invert charging cylinder and open
charging cylinder valve F to add partial charge for
leak checking. With leak detector, check manifold
connections and system for leaks. After locating
leak, capture refrigerant, repair leak, and begin at
step 1.
Charging
NOTE
: Do not use captured or recycled refrigerant in
Maytag units. Captured or recycled refrigerant
voids any warranty.
NOTE
: Charge system with exact amount of refrigerant.
Refer to unit serial plate for correct refrigerant
charge. Inaccurately charged system will cause
future problems.
To charge system:
1. Close valves A to vacuum pump and C to vacuum
gauge and E to low side manifold gauge.
2. Set scale on dial-a-charge cylinder for corresponding
HFC134a pressure reading.
3. Open valve F to charging cylinder and let exact
amount of refrigerant flow from cylinder into system.
Close valve.
Low side gauge pressure should rise shortly after
opening charging cylinder valve as system pressure
equalizes through capillary tube.
If pressure does not equalize, a restriction typically
exists at capillary/drier braze joint.
4. If pressure equalizes, open valve E to low side
manifold gauge and pinch off high side drier process
tube.
5. Start compressor and draw remaining refrigerant from
charging hoses and manifold into compressor through
compressor process tube.
6. To check high side pinch-off drier process tube. Close
valve D to high side gauge. If high side pressure
rises, repeat high side pinch-off and open valve D.
Repeat until high side pinch-off does not leak.
7. Pinch-off compressor process tube and remove
charging hose. Braze stub closed while compressor is
operating.
8. Disconnect power. Remove charging hose and braze
high side drier process tube closed.
9. Recheck for refrigerant leaks.
Refrigerant Charge
Refrigerant charge in all capillary tube systems is
critical and exact amount is required for proper
performance. Factory charges are shown on serial
plate.
NOTE:
Do not use refrigerant other than shown on serial
plate.
Содержание Luxury Series
Страница 13: ...13 16021730 Rev 0 Refrigerant Flow Side by Side Refrigerant Flow Diagram ...
Страница 14: ...16021730 Rev 0 14 Cabinet Air Flow Side by Side Cabinet Air Flow Diagram ...
Страница 16: ...16021730 Rev 0 16 Water Valves Diagram Bottom View Back View Primary Valve Secondary Valve Filter Head Bypass ...
Страница 46: ...A 1 ...
Страница 72: ...B 1 Appendix B ...