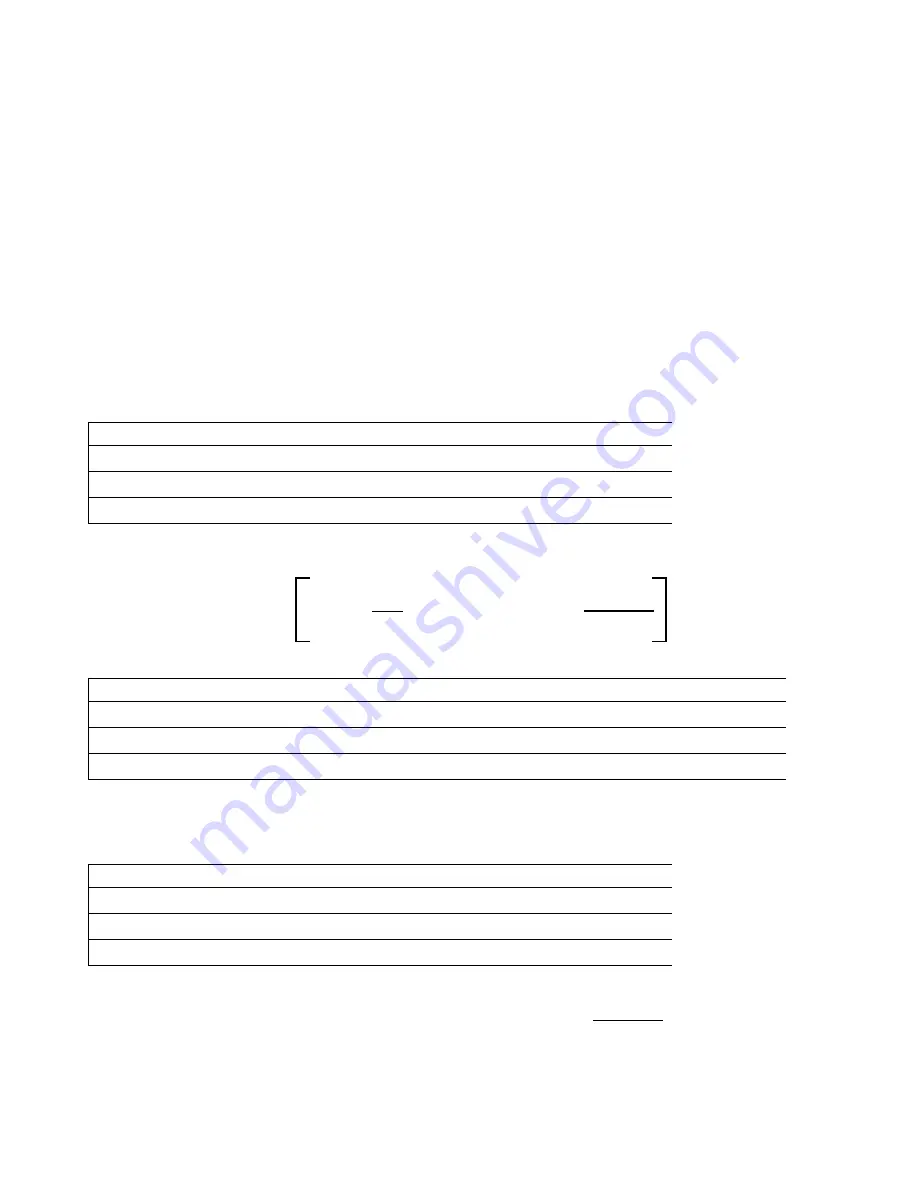
84
the error), integral (the time that the error has been present), and derivative (the rate of change for the error) param-
eters. With proper tuning, the PID control algorithm can hold the process value close the set point while minimiz-
ing overshoot and undershoot.
Normalized Error
The error value versus set point that is calculated by the controller is normalized and represented as percent of full
scale. As a result, tuning parameters entered by the user are not dependent upon the scale of the process variable
and the PID response with similar settings will be more consistent even when using different types of sensor
inputs.
The scale used to normalize the error is dependent upon the type of sensor selected. By default, the full nominal
range of the sensor is used. This range is editable by the user if tighter control is desired.
PID Equation Formats
The controller supports two different forms of the PID equation as specified by the Gain Form setting. The two
forms require different units for entry of the PID tuning parameters.
Standard
The standard form is more commonly used in industry because its time-based settings for the integral and deriva-
tive coefficients are more meaningful. This form is selected by default.
Parameter
Description
Units
K
p
Gain
unitless
T
i
Integral Time
seconds or seconds/repeat
T
d
Derivative Gain
seconds
Output (%) = K
p
e(t) +
f
e(t)dt + T
d
de(t)
dt
1
T
i
Parameter
Description
Units
e(t)
Current Error
% of full scale
dt
Delta Time Between Readings
seconds
de(t)
Difference Between Current Error & Previous Error
% of full scale
Parallel
The parallel form allows the user to enter all parameters as Gains. In all cases, larger gain values result in faster
output response. This form is used in the WebMaster controller and is used internally by the Control Module.
Parameter
Description
Units
K
p
Proportional Gain
unitless
K
i
Integral Gain
1/ seconds
K
d
Derivative Gain
seconds
Output (%) = K
p
e(t) + K
i
f
e(t)dt + K
d
de(t)
dt
Integral Value Management
To determine the integral component of the PID calculation, the controller software must maintain a running total
of the accumulated area under the error curve (Current Integral). The sign of the value added to the accumulated