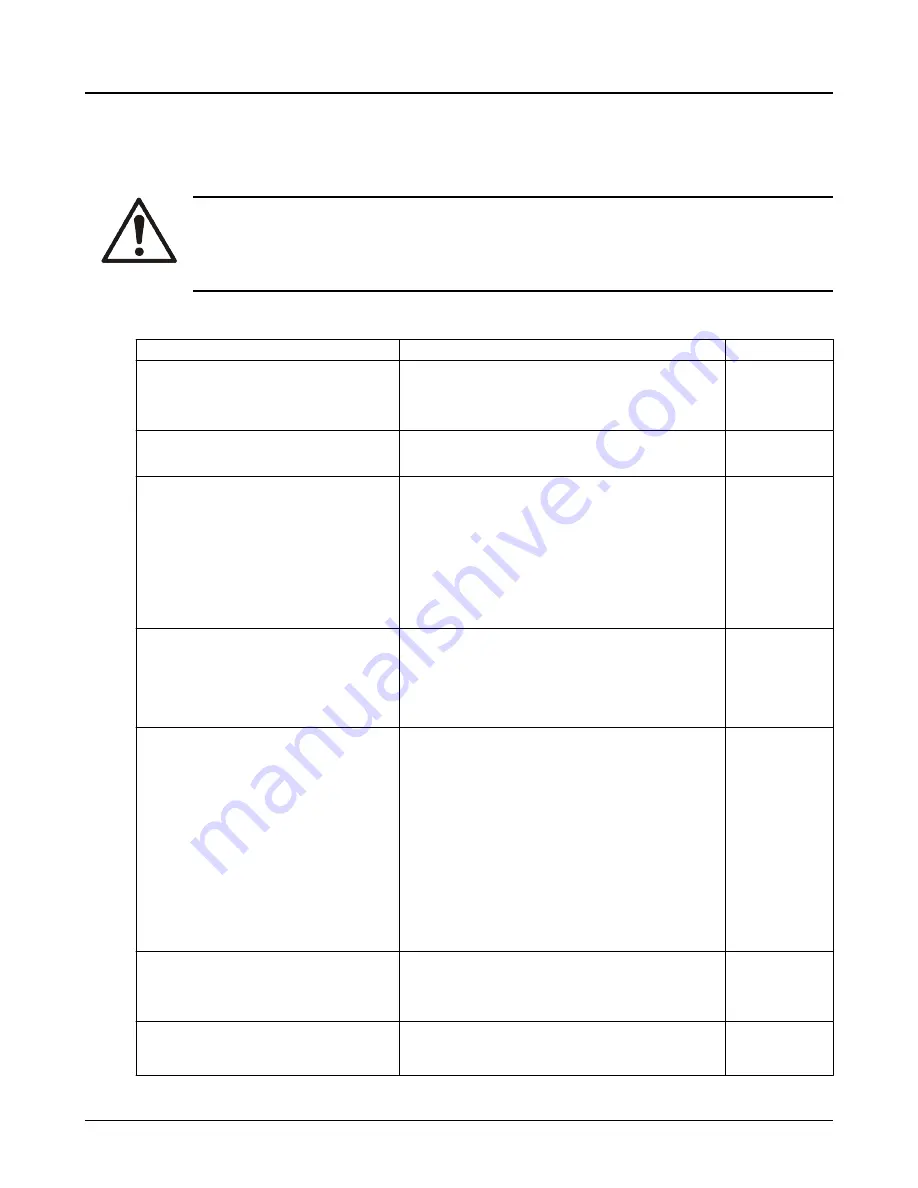
4.7.3 Suction-piping checklist
Performance curve reference
CAUTION:
Vary the capacity with the regulating valve in the discharge line. Never throttle the flow from the
suction side. This action can result in decreased performance, unexpected heat generation,
and equipment damage.
Suction-piping checks
Check
Explanation/comment
Checked
Check that the distance between the inlet
flange of the pump and closest flow disrup-
tion (elbow, valve, strainer, or expansion
joint) is at least five pipe diameters.
This minimizes the risk of cavitation in the suction in-
let of the pump due to turbulence.
See the Example sections for illustrations.
Check that elbows in general do not have
sharp bends.
See the Example sections for illustrations.
—
Check that the suction piping is one or two
sizes larger than the suction inlet of the
pump.
Install an eccentric reducer between the
pump inlet and the suction piping.
Suction pipe reducers should have no
more than two pipe diameter changes per
reducer.
The suction piping must never have a smaller diame-
ter than the suction inlet of the pump.
See the Example sections for illustrations.
Check that the eccentric reducer at the
suction flange of the pump has the follow-
ing properties:
•
Sloping side down
•
Horizontal side at the top
See the example illustrations.
Suggested suction strainers are used.
Check that they are at least three times the
area of the suction piping.
Monitor the pressure drop across the suc-
tion strainer.
An increased pressure drop across the
strainer of 5 psi (34.5 kPa) indicates that
the strainer should be removed and
cleaned.
After a period of time (24 hours minimum)
system flushing should be complete and
the suction strainer can be removed.
Suction strainers help to prevent debris from entering
the pump.
Mesh holes with a minimum diameter of 1/16 in. (1.6
mm) are recommended.
Liquids with specific gravity less than 0.60 a pressure
drop across the suction strainer may be due to ice
buildup. Ice buildup can cause turbulence, low pres-
sure areas and pumpage vaporization.
If more than one pump operates from the
same liquid source, check that separate
suction-piping lines are used for each
pump.
This recommendation helps you to achieve a higher
pump performance and prevent vapor locking espe-
cially with specific gravity of liquid less than 0.60.
If necessary, make sure that the suction
piping includes a drain valve and that it is
correctly installed.
—
4.7 Piping checklists
Models 3180, 3181, 3185, and 3186 Installation, Operation, and Maintenance Manual
43
Содержание GOULDS PUMPS 3180
Страница 1: ...Installation Operation and Maintenance Manual Models 3180 3181 3185 and 3186 ...
Страница 2: ......
Страница 153: ...9 1 Certificates of conformance Models 3180 3181 3185 and 3186 Installation Operation and Maintenance Manual 151 ...
Страница 155: ...9 1 Certificates of conformance Models 3180 3181 3185 and 3186 Installation Operation and Maintenance Manual 153 ...