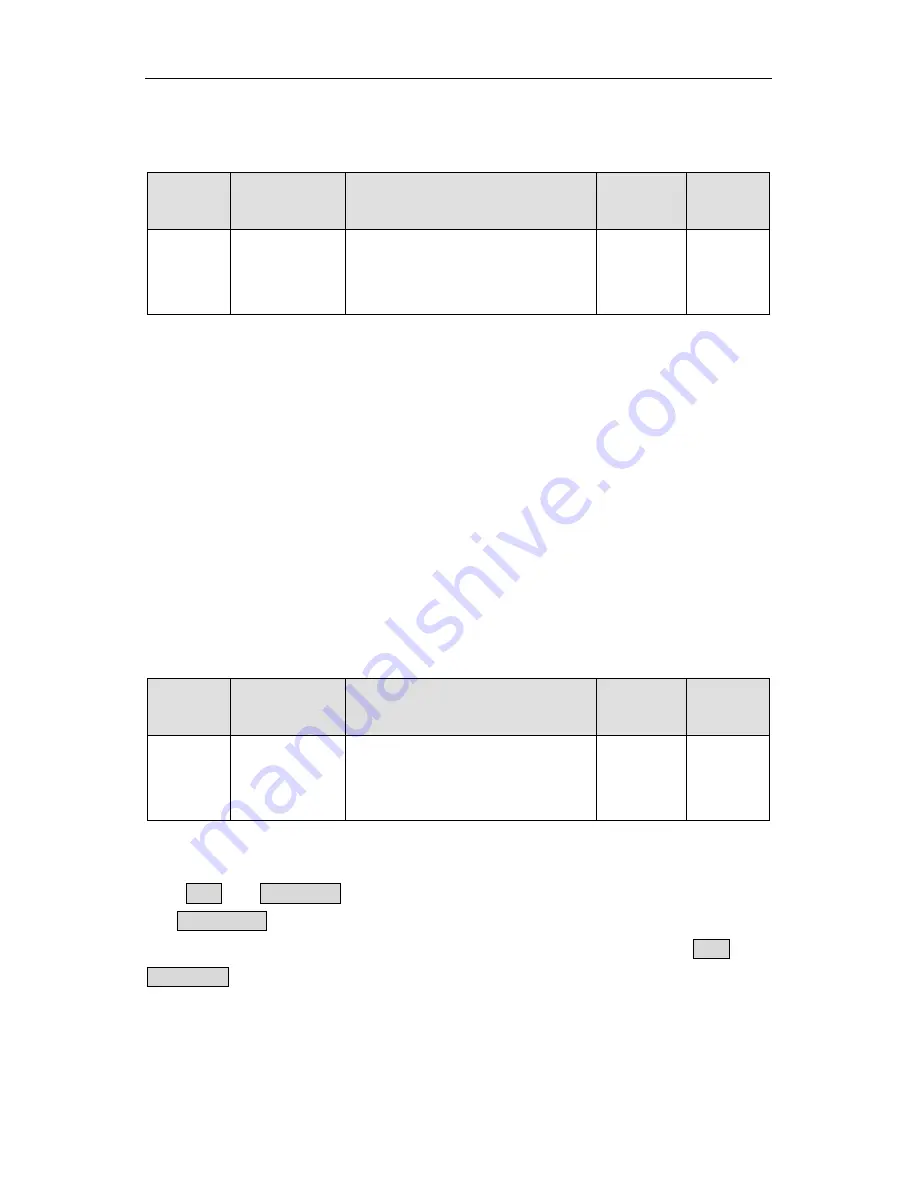
CHV180 series frequency inverter special for elevator Detailed function description
.30.
6. Detailed function description
6.1 P0 Group--Basic function
Function
Code
Name
Description
Setting
Range
Factory
Setting
P0.00
Speed control
mode
0: Sensorless vector control
1: Vector control With PG
2: V/F control
0~2
1
0: Sensorless vector control: It is widely used in the application such as low-grade
elevator which requires lower accuracy or used for debugging.
1: Vector control with PG: Close-loop vector control requires the client to install the
speed feedback equipment. Therefore it is suitable for the high-grade elevator requiring
high speed control accuracy and speedy dynamic response.
2: V/F control: It is suitable for the low-end elevator which requires lower accuracy or is
used for debugging.
Note:
When selecting the vector control, it is necessary to set the nameplate parameters and
encoder parameters correctly and complete the autotuning before running to get right
motor parameters (for synchronous motor, it is the pole position angle). Right
parameters are the assurance for high performance of vector control.
P3 group can optimize the performance of vector control.
Function
Code
Name
Description
Setting
Range
Factory
Setting
P0.01
Run command
source
0: Keypad (LED extinguished)
1: Terminal (LED flickering)
2: Communication (LED lights on)
0~2
1
The control commands of inverter include: start, stop, up, down, fault reset and so on.
0: Keypad (
“LOCAL/REMOT”
LED extinguished);
Both RUN and STOP/RST key are used for running command control. If Multifunction
key QUICK/JOG is set as FWD/REV switching function (P7.03 is set to be 1), it will be
used to change the rotating orientation.
In running state, pressing RUN and
STOP/RST in the same time will cause the inverter coast to stop.
1: Terminal (
“LOCAL/REMOT”
LED flickering)
The operation, including up, down etc. can be controlled by multifunctional input
terminals.