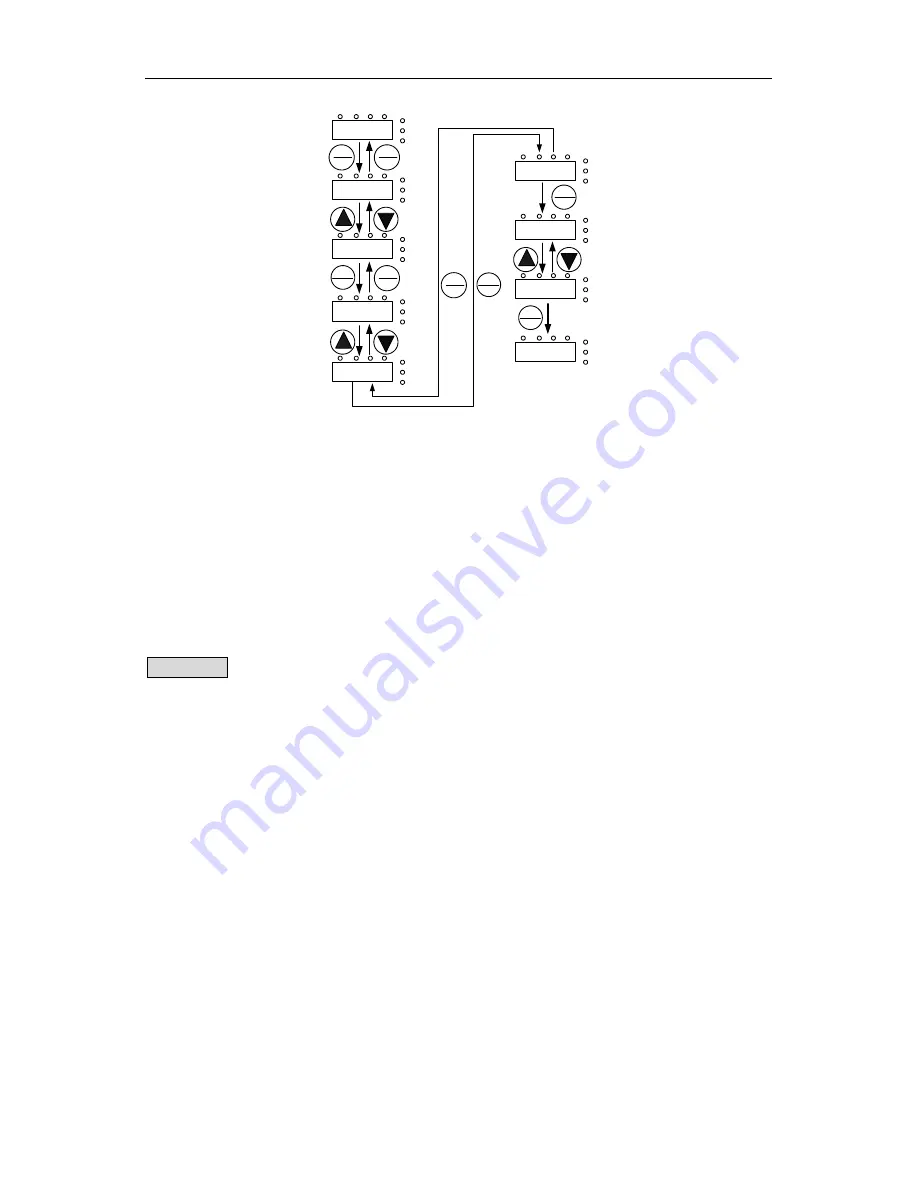
CHV180 series frequency inverter special for elevator Operation
.27.
>>
SHIFT
50.00
P0.
PRG
ESC
PRG
ESC
P1.
P1.00
PRG
ESC
DATA
ENT
P1.01
0.00
0
P1.02
DATA
ENT
DATA
ENT
PRG
ESC
0
.
000
1.000
Stand-by/operation
Figure 5.2 Flow chart of parameter setting.
Under the third-class menu, if the parameter has no flickering bit, it means the function
code cannot be modified. The possible reasons could be:
This function code is not modifiable parameter, such as actual detected parameter,
operation records and so on;
This function code is not modifiable running state, but modifiable in stop state.
5.2.2 Fault reset
If the inverter has fault, it will prompt the related fault information. User can use
STOP/RST or according terminals determined by P5 Group to reset the fault. After fault
reset, the inverter is at stand-by state. If user does not reset the inverter when it is at fault
state, the inverter will be at operation protection state, and can not run.
5.2.3 Parameter copy
For details, please refer to the instructions of LCD keypad functions
5.2.4 Motor parameter autotune
If “Sensorless Vector Control” or “Vector Control with PG” mode is chosen, motor
nameplate parameters must be input correctly as the autotuning is based on it. The
performance of vector control depends on the parameters of motor strongly, so to
achieve excellent performance, firstly must obtain the parameter of motor exactly.
This function is not the same between synchronous motor and asynchronous motor, for
details please refer to the description of function code P0.08.
The procedure of motor parameter autotuning is as follows:
Firstly, choose keypad command as the run command source (P0.01).
Set P0.08 to be 1, and for the detail process of motor parameter autotuning, please refer