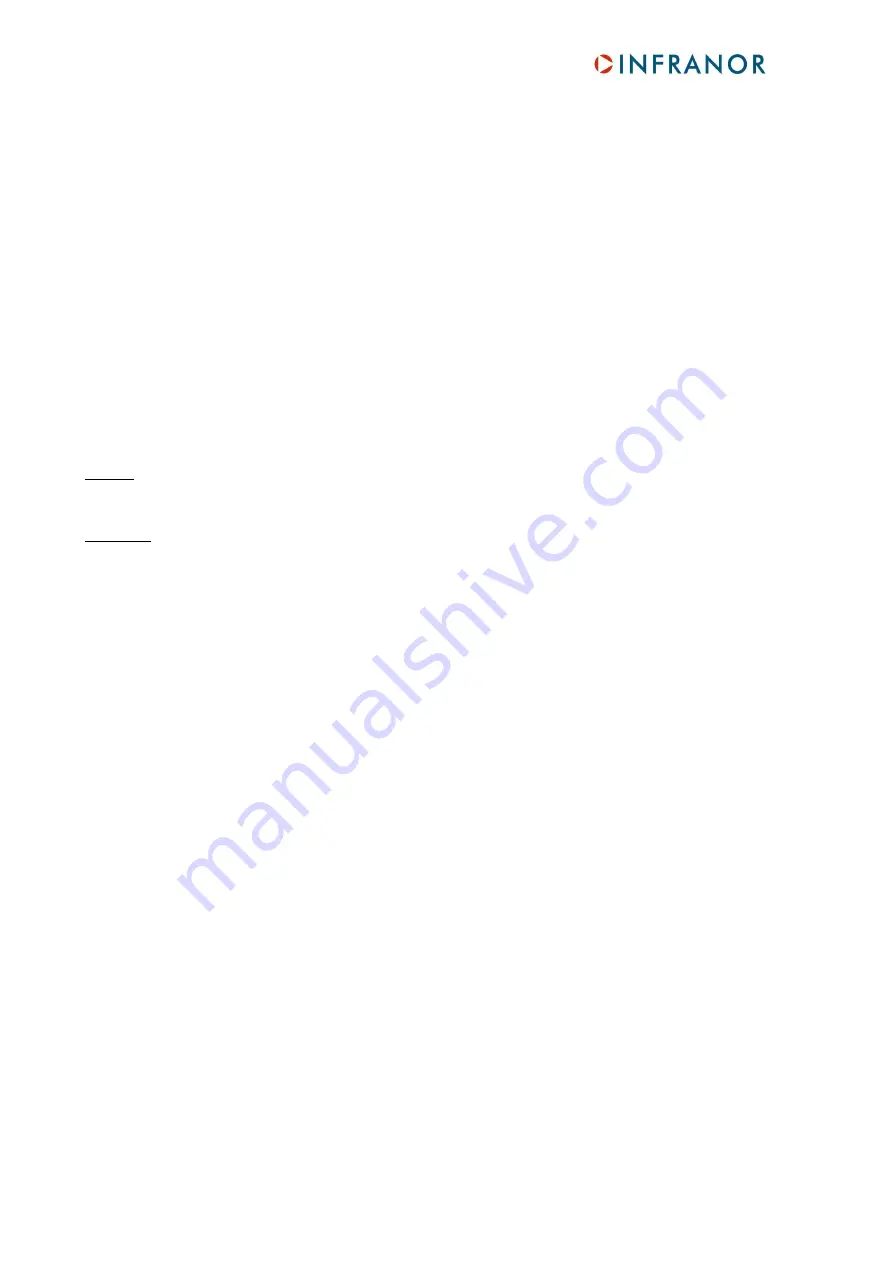
Chapter 2 - Commissioning
16
XtrapulsCD1-pm - User manual
For a complete adjustment, the
Autotuning
procedure must
always
be executed in
Position
mode (at power on,
the amplifier is automatically in
Position
mode).
But the amplifier position loop stability can also be tested in
Speed
mode. In this case, after the execution of the
Autotuning
procedure in
PI²
mode:
•
check that the motor is correctly running in both directions,
•
check the
response at a small displacement without I
dc
saturation
(oscilloscope function).
In case of loud noise in the motor at standstill or when running, check the rigidity of the mechanical transmission
between motor and load (backlashes and elasticities in motor and couplings).
If required, start a new
Autotuning
procedure by selecting a lower bandwidth.
If the instability remains, start a new
Autotuning
procedure by activating the
Antiresonance
filter. If necessary,
adjust more accurately the loop response stability by adjusting the stability gain.
If the
Autotuning
procedure was executed in
PI²
mode, when the
Position
mode was selected, the
Feedforward
gains of the position regulator must be adjusted manually. Set the
Feedforward speed 1
gain value at 1, in order
to avoid a high following error value.
8.2 - LOOP ADJUSTMENT WITH A VERTICAL LOAD
In the case of an axis with vertical load, proceed as follows:
Select the
Limiting
current limitation mode.
Initialize the speed loop gains corresponding to the unloaded motor (execute therefore the
Autotuning
procedure with the motor uncoupled from its mechanical load).
Couple the motor with its load. If possible, make a control in speed mode; otherwise, close the position loop with a
stable gain.
Select the
PI²
speed mode and move the axis by means of the speed input command until a stall position where
one motor revolution is not dangerous for operator and machine (far enough from the mechanical stops).
Execute then the
Autotuning
procedure with the motor at standstill. If the axis is moving, the
Autotunig
procedure is not accepted by the amplifier.
Select the
Position
mode and set the
Feedforward speed 1
gain value at 1, in order to avoid a high following
error value.
9 - ROTATION / COUNTING DIRECTION
The counting direction can be reversed by selecting the
Reverse movement
in the
Visual Drive Setup
parameterization software.
10 - PARAMETER SAVING
When all adjustments have been made, the parameters may have to be
stored
in a non volatile EEPROM (the
amplifier must be disabled).