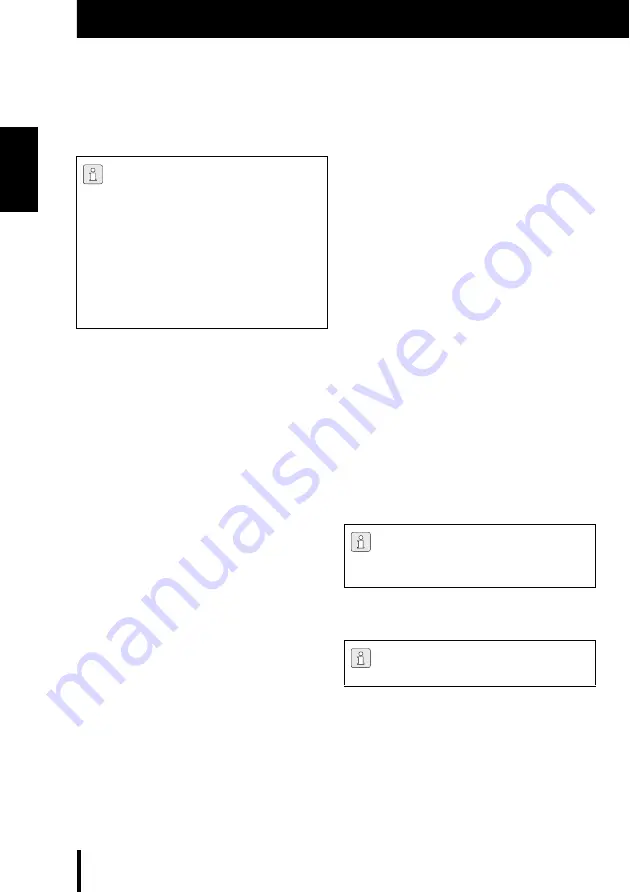
44
H A N D L I N G T H E C O O L A N T / L U B R I C A N T ( C / L )
E N
7.4
Filling in C/L
▷
Fill 20 litres of water and 1 litre of coolant/lubri-
cant concentrate into a separate container and
mix well.
▷
Insert the filter bag into the C/L container.
▷
Fill the mixed C/L into the C/L container.
▷
Reattach the cover with the drain pipe and
secure it with the four star-knob nuts.
7.5
Cleaning the C/L system
▷
Remove and clean the swarf sieve.
▷
Clean the milling chamber.
▷
Reinsert the swarf sieve.
▷
Mount the splash guard.
▷
Empty the C/L container (see page 43).
▷
Clean the C/L container (see page 43).
▷
Fill 5 litres of water and 250 ml of coolant/lubri-
cant concentrate into a separate container and
mix well.
▷
Insert the filter bag.
▷
Fill the mixed C/L into the C/L container.
▷
Fully connect the supply unit again.
▷
Activate
“
Clean coolant/lubricant circuit
”
in the
control service functions.
▷
Start the cleaning in the software.
-or-
▷
briefly press operation button [A] on the milling
machine.
C/L is circulated for 15 minutes to clean the sys-
tem.
When the cleaning is completed:
▷
Empty the C/L container (see page 43).
▷
Refill the C/L container (see page 44).
The water for the coolant/lubricant must
have drinking-water quality. The optimal
hardness range is between 10 - 20
°
dH
(corresponds to 1.8 - 3.6 mmol total hard-
ness per litre). If the hardness is far
beyond this range, we recommend the
addition of distilled water. For grinding
glass-ceramic materials, it is generally rec-
ommended to use distilled water.
The cleaning can be interrupted and
restarted by briefly pressing operation
button [A].
After the cleaning, the C/L used for the
cleaning must be disposed of.