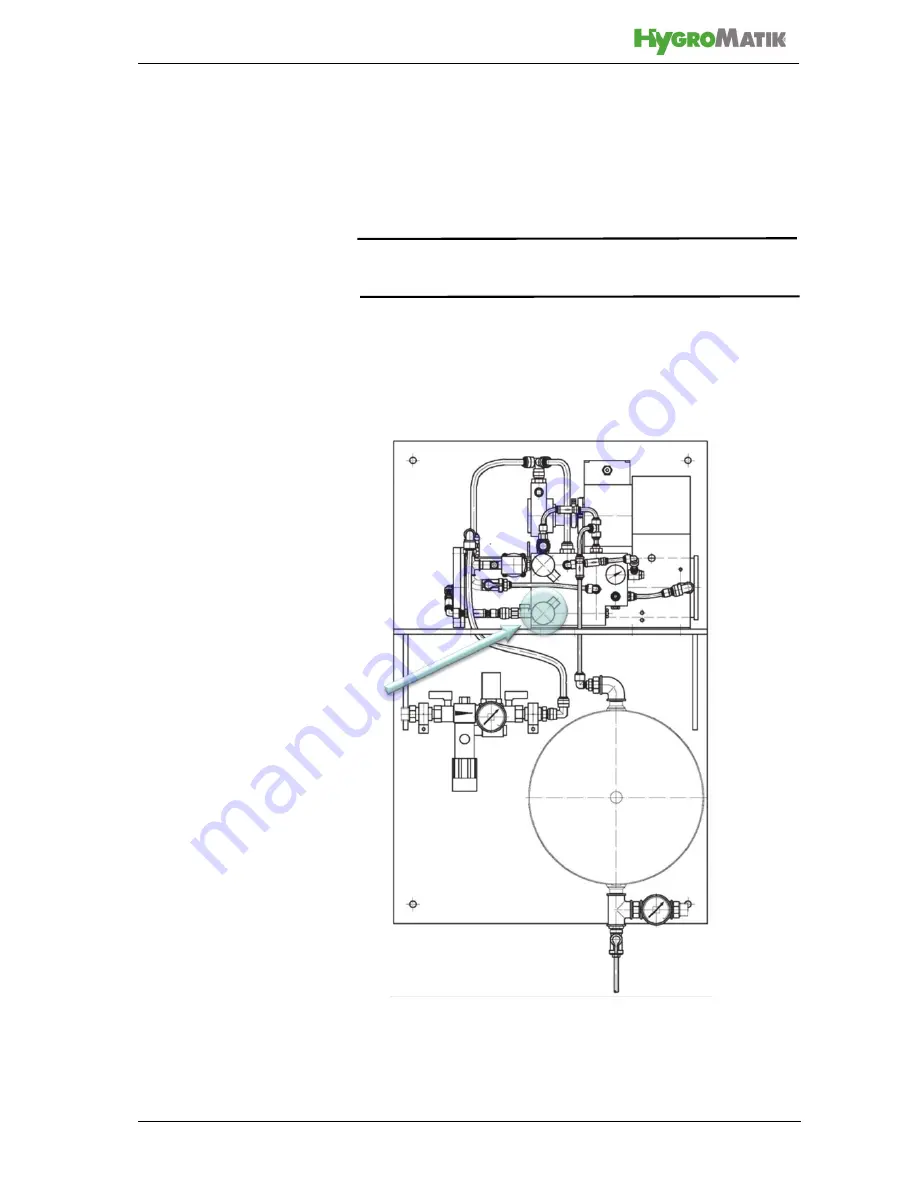
Page 29
8. Settings
8.1
Setting the switch-off pressure
When the required operating pressure is achieved in the system
to be filled, the system switches off automatically via the pres-
sure switch (permeate). This pressure must be adjusted on the
pressure switch (permeate). Factory setting is approx. 3 bar.
Please note
Before changing this setting pls. contact HygroMatik GmbH.
The system switches back on again automatically when the
pressure in the system to be filled has dropped by approx. 0.5
bar.
Fig. 8: Pressure switch (Permeate)
Содержание WL-RO-170
Страница 1: ...Reverse osmosis plants WL ROB 170 WL RO 170 WLROB170 ENx WLROB170 EN Manual...
Страница 21: ...Page 21 5 5 Dimension sheet Fig 3 Front Top view Permeate Connection R3 4...
Страница 22: ...Page 22 Fig 4 Lateral view Fig 5 Front view of securing and fixing plate Concentrate Hose 8 Wastewater drain...
Страница 46: ...Seite 46 This page intentionally left blank...