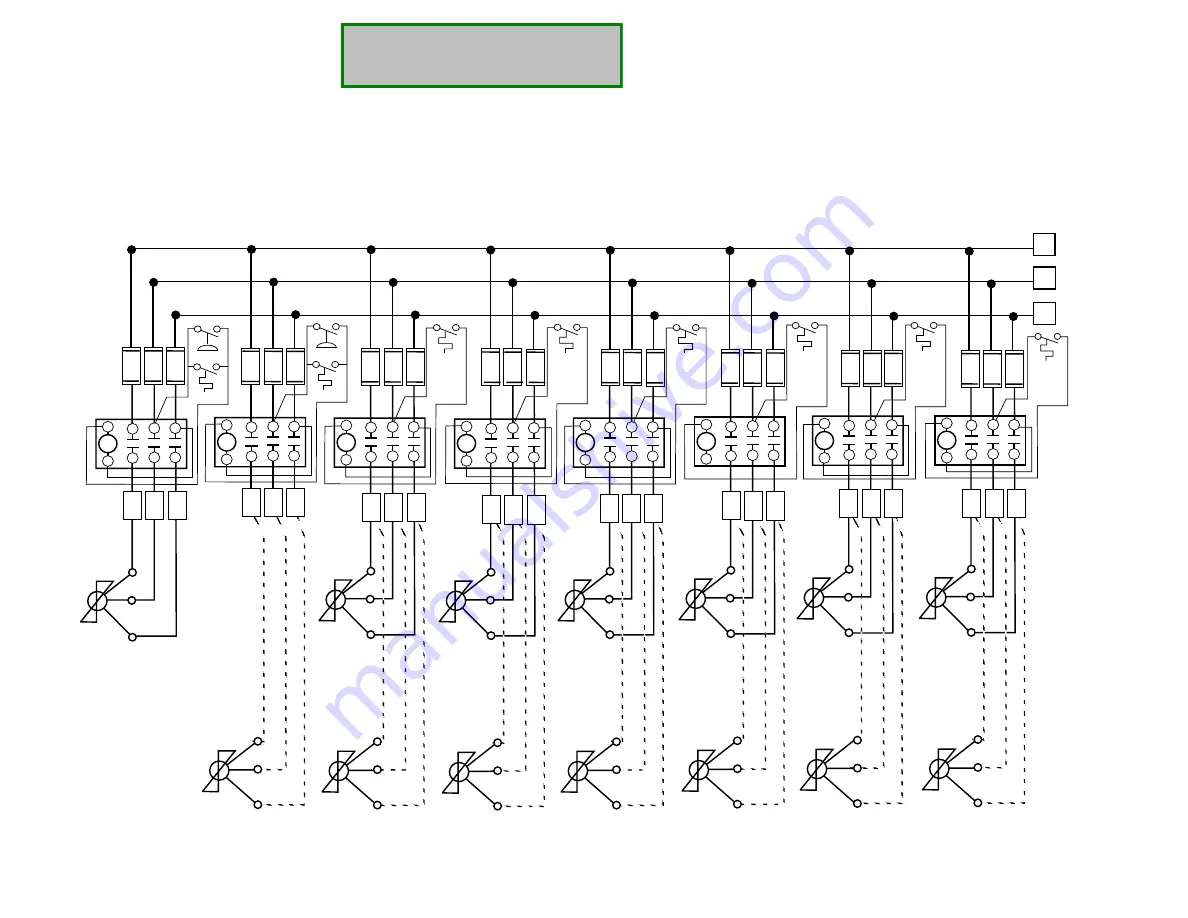
September 1,
1997
P/N 401789
5 - 7
H
U
S
S
M
A
N
N
C
O
R
P
O
R
A
T
IO
N
•
B
R
ID
G
E
T
O
N
, M
O
6
3
0
4
4
-2
4
8
3
•
P
rin
te
d
in
U
S
A
L1
L2
L3
C
37
38 39
40 41
42
37
38
39
40
41
42
37
38
39
40
41
42
C
31
32 33
34
35 36
31
32
33
34
35
36
31
32
33
34
35
36
C
C
C
C
C
C
1
2
3
4
5
6
7
8
10
11
12
9
19
20
21
22
23
24
25 26
27
28
29 30
16
17
18
13
14
15
25 26
27
28
29
30
25
26
27
28
29
30
19
20
21
22
23 24
19
20
21
22
23
24
16
17
18
13
14
15
16
17
18
13
14
15
7
8
10
11 12
9
7
8
10
11
12
9
4
5
6
4
5
6
1
2
3
2
3
Ambient Temperature Control of All Banks With Pressure Override of the First Fan Bank
208/3/60 230/3/60 460/3/60
1
Figure 5-3 — Ambient Control of All Banks With Pressure Override of the First Fan Bank
208/3/60 230/3/60 460/3/60
Return to Contents