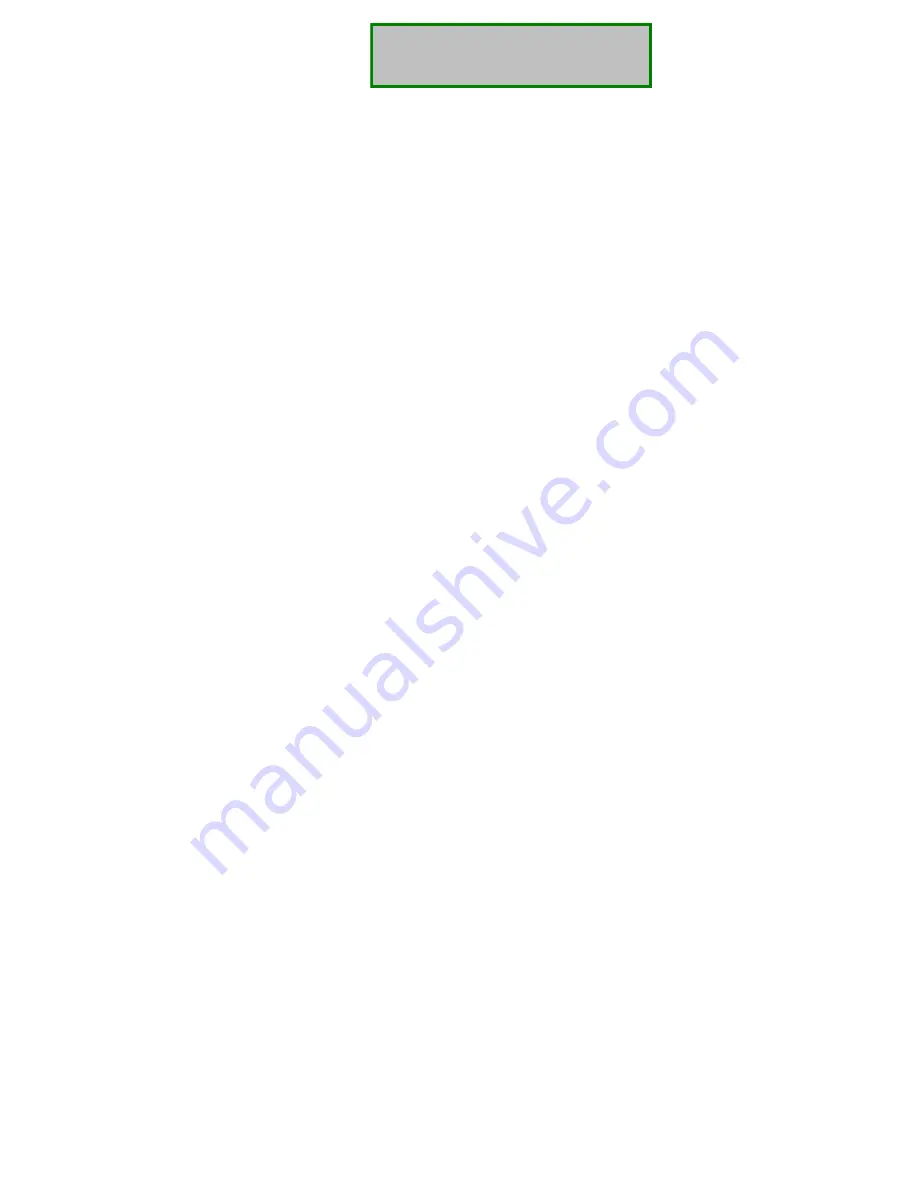
Plug holes to compressor manufacturer's
specifications.
Remove suction and discharge rotolocks.
Remove mounting bolts.
When moving the compressor, use a come-along,
hoist or hydraulic lift to carry the weight.
Do not
use the rack piping or panel to support a
hoist or come-along.
Do not
use ceiling trusses to support a hoist or
come-along.
If a compressor removal table is used, slide the
compressor fully on to the table, then roll table to
overhead hoist or hydraulic lift area.
Install the new compressor in reverse order of
removal. Do not open the new compressor to the
system until after it has been leak tested and triple
evacuated.
Check rotation of new compressor (see Page 8-4).
Note:
Oil level regulator sight glasses are designed to pro-
vide a hermetic seal when internally pressurized. Some
leaking may occur when a deep vacuum is pulled.
Cleaning the Turba-shed™
Should the Turba-shed require cleaning, first shut
down the system. Isolate the Turba-shed and
bleed off pressure into an
approved recovery
vessel.
Remove the top and bottom sight glasses
and the oil supply line. With a clean, dry, regulat-
ed pressure source like nitrogen, blow out any
sludge or dirt. Install the sight glasses using new
O-rings.
Parker Number 2-23,
Compound557
Precision Rubber, Number 023,
Compound 2337
Leak test, evacuate, and charge with fresh oil
(only Suniso 3G or Texaco Capella WF32). Open
valves closed to isolate the oil system and bring
the rack back on line.
Replacing Drier and Filter Cores
Shut down the system. Isolate the core to be
replaced and bleed off pressure into an
approved
recovery vessel.
Open housing, replace core and
close up. Pressurize, leak test and bring back into
line.
START-UP AND MAINTENANCE
September 1, 1997
8 - 6
HUSSM ANN CORPORATION • BRIDGETON, M O 63044-2483 • Printed in USA
Return to Contents