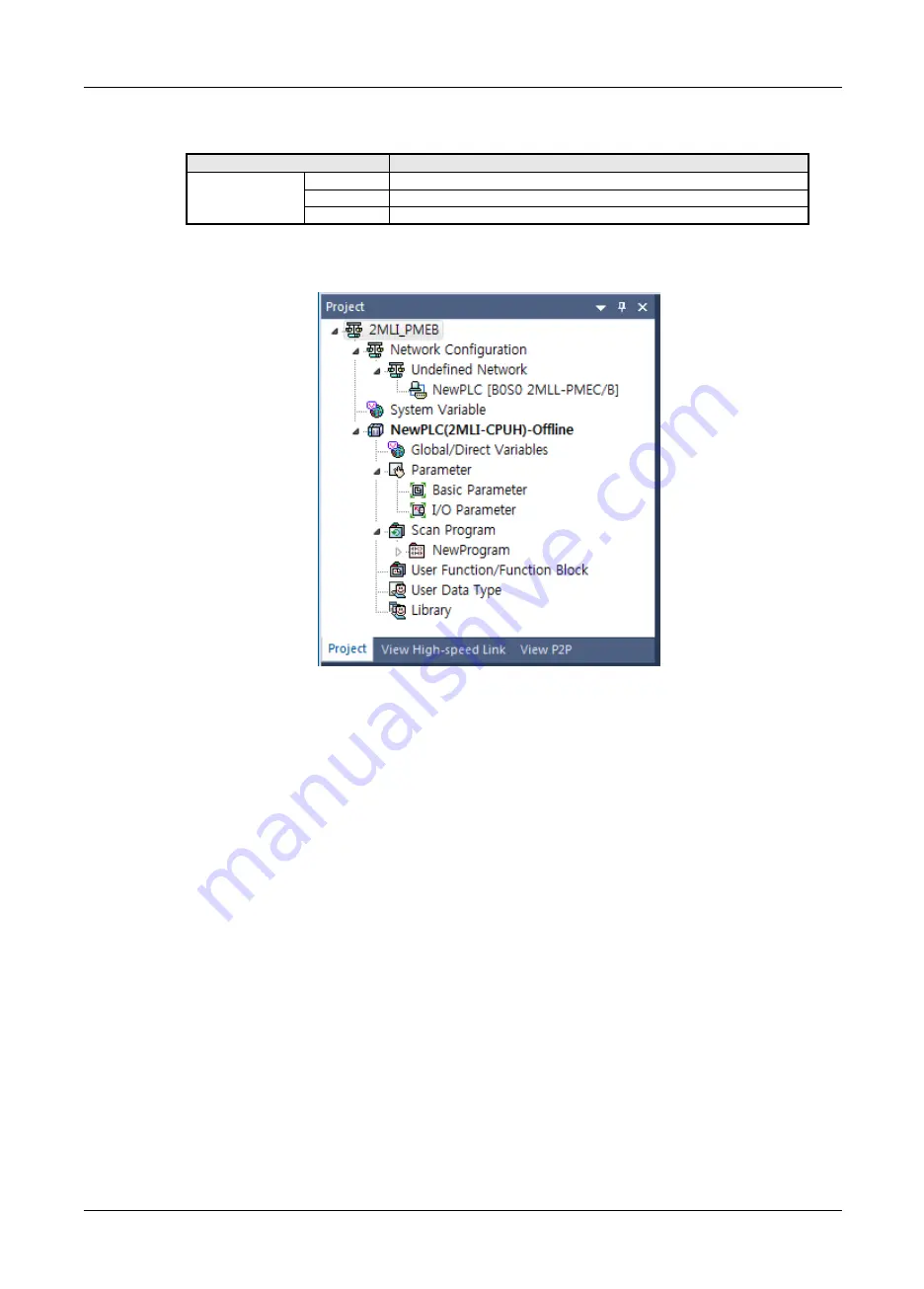
Chapter 5 Communication Program
6
Pnet I/F Module 2MLL-PSRA, 2MLL-PMEA, 2MLL-PMEB User
’s Guide
R240
Honeywell
January 2019
Pnet I/F module Off-line registration on base 0, slot 2 is as follow
Classification
Description
Communication
module setting
Type
Pnet I/F module
Base
Base no. of mounted module
Slot
Slot no. of mounted module
[Table 5.2.1] Communication module setting contents
Registration PMEB module on base 0, slot 2
[Figure 5.2.7] Registration screen