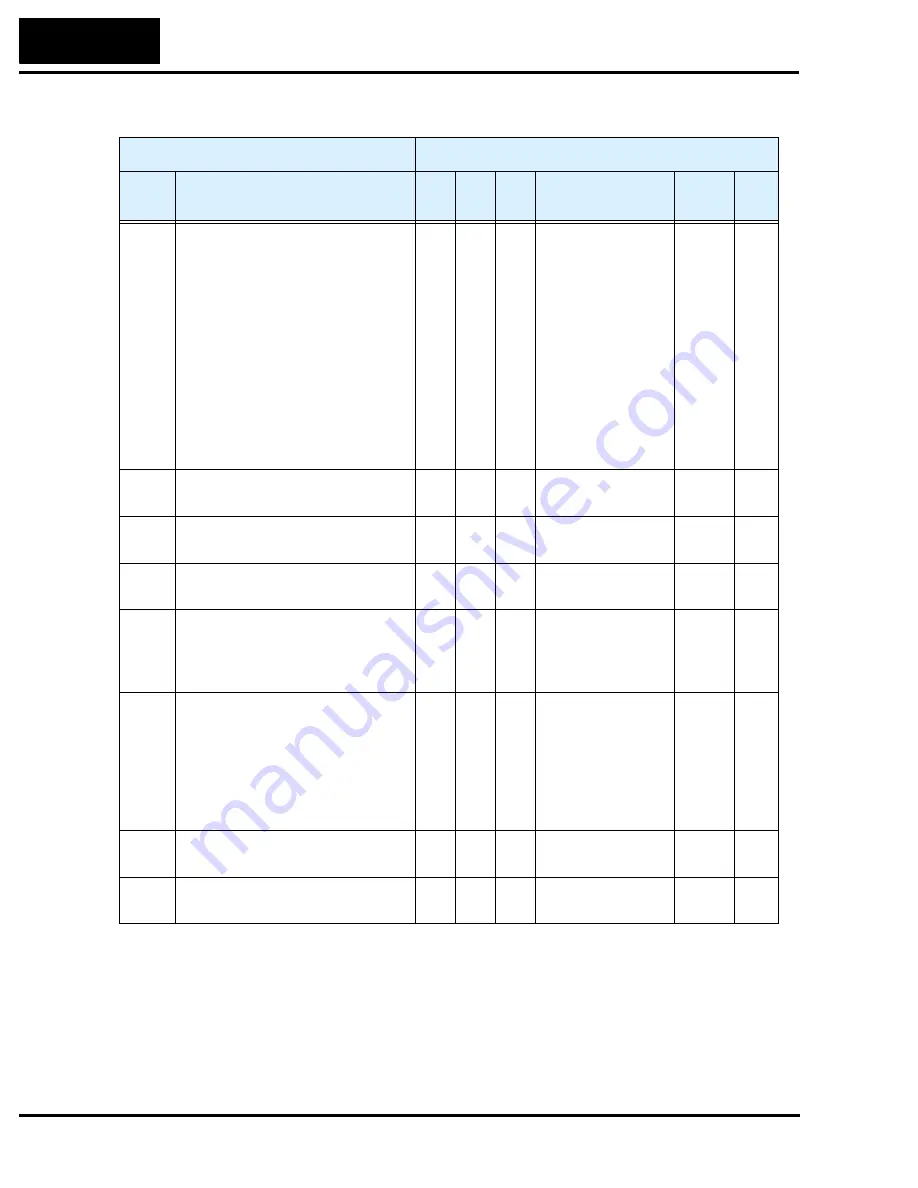
Network Register Map
84
Fine Tuning Functions
“B” Group Parameters
DeviceNet Class ID = 103
Func.
Code
Name
Inst Attr Size
Range
Scaling
Get/
Set
B_01 Selection of automatic restart
mode
1
101
1
0 Alarm output
after trip, no
automatic restart
1 Restart at 0Hz
2 Resume opera-
tion after freq.
matching
3 Resume
previous freq. after
freq. matching,
then decelerate to
stop and display
trip info.
—
G/S
B_02 Allowable under-voltage power
failure time
1
102
2
0.3 – 25.0 sec.
10
G/S
B_03 Retry wait time before motor
restart
1
103
2
0.3 – 100.0 sec.
10
G/S
B_12 Level of electronic thermal
setting
1
112
2
5% to 120% rated
current, in A
10
G/S
B_13 Electronic thermal characteristic
1
113
1
0 Reduced torque
1 Constant torque
2 Reduced
torque2
—
G/S
B_21 Overload restriction operation
mode
1
121
1
0 Disabled
1 Enabled for
acceleration and
constant speed
2 Enabled for
constant speed
only
—
G/S
B_22 Overload restriction setting
1
122
2
50% to 150%
rated current, in A
100
G/S
B_23 Deceleration rate at overload
restriction
1
123
2
0.3 – 30.0
10
G/S
Содержание L100DN DeviceNet Series Addendum
Страница 96: ......