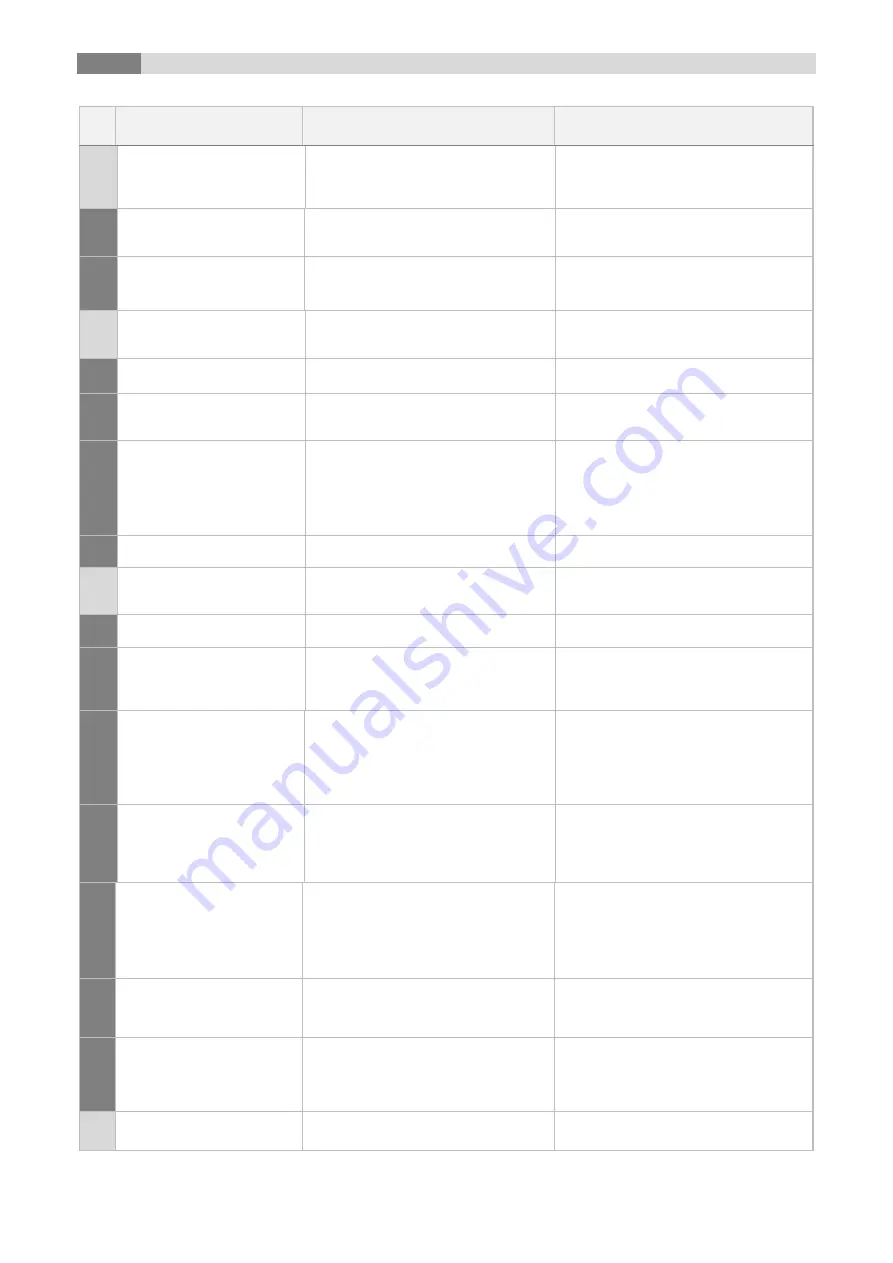
10
Fault reports and their Fault reports and their corrections
72
No. Fault report
Cause of fault
Fault correction
067
FIRE OUT
no successful ignition detected after the
ignition time has elapsed
Check fuel level
Check burning parameters, adjust as
adapt
Clean intermediate hopper level sensor
068
TEMP. CONTROL
Fuel storage room temperature sensor
has exceeded the maximum
permissible temperature
▪
Check fuel storage room
▪
Alarm fire brigade in case of fire
069
STL
Boiler temperature has exceeded the
maximum permissible boiler
temperature
▪
Cool down boiler (< 75 °C)
▪
Quit STL
070
LAMBDA FUEL
Material correction of the lambda
control has been at the upper or lower
limit for 30 minutes
Adjust fuel values
✆
- contracting party
071
LAMBDA PROBE
Lambda probe value does not change
clean lambda probe
✆
- contracting party
073
LAMBDA CALIBRATION
Lambda probe calibration outside the
limit range or error during lambda
calibration
clean lambda probe
✆
- contracting party
076
Fuel
** Priming / plug-in ignition cannot be
carried out because there is no fuel.
Notification FIRE OUT occurs for the
second time within 2 hours
*during operation intermediate hopper
is not full despite power reduction
Check fuel level
Check burning parameters, adjust as
adapt
Clean intermediate hopper level sensor
077
Additional input
Digital input responds to additional
input
check the unit connected to the input
078
NIVEAU LEVEL
Active intermediate hopper level
sensor; low fuel level at intermediate
hopper
Check fuel level
Check discharge system (motor, screw,
springs)
079
SUCTION SENSOR
sensor always reports fully during
suction (no sensor changes)
Check fuel level
Check discharge system (motor, )
080
MP ROOM DISCHARGE
Digital input motor protection room
discharge has responded
motor protection acknowledges
Check discharge system (motor, screw,
springs)
Remove debris
081
SPEED ID-FAN
Speed outside the limits for more than
10 seconds
▪
Check connection rotation speed
sensor
▪
Check ID-fan
▪
✆
▪
✆
- contracting party
082
GRATE CLEANING 1
Grate cleaning failure; motor damaged;
grate linkage damaged or loosened;
misaligned grate sensor
▪
Check grate cleaning motor
▪
Check grate linkage
▪
Check grate cleaning end switch
▪
✆
- contracting party
083
GRATE CLEANING 2
Failure grate cleaning; impossible to
close grate; grate got stuck; grate
linkage damaged or loosened
▪
Remove debris
▪
Check grate cleaning motor
▪
Check grate linkage
▪
Check grate cleaning end switch
▪
✆
- contracting party
084
GRATE CLEANING 3
Grate was opened during the
combustion
▪
Check grate cleaning motor
▪
Check grate linkage
▪
Check grate cleaning end switch
085
SUCTION MODE
maximum suction cycles exceeded (with
suction discharge)
maximum suction time exceeded
(at internal suction hopper)
▪
Adjust suction cycles
▪
Check discharge system (motor,
screw)
▪
Check fuel quality
087
ASH CONTAINER
Ash container door is opened
▪
Connect ash container
▪
Close ash container door
Содержание pelletstar CONDENSATION 10
Страница 1: ...OPERATING INSTRUCTIONS Pellet boiler pelletstar CONDENSATION 10 60 ...
Страница 20: ...8 Temperature manager 20 Fig 8 6 Example temperature manager when time mode without difference ...
Страница 85: ...Annex 15 85 15 ANNEX 15 1 Additional boiler schematic visualization Hydraulic recommendation 1 ...
Страница 86: ...15 Annex 86 Hydraulic recommendation 2 ...
Страница 87: ...Annex 15 87 15 2 Solar module schematic representation Program 1 ...
Страница 88: ...15 Annex 88 Program 2 ...
Страница 89: ...Annex 15 89 Program 3 ...
Страница 90: ...15 Annex 90 Program 4 ...
Страница 91: ...Annex 15 91 Program 5 ...
Страница 92: ...15 Annex 92 Program 6 ...
Страница 93: ...Notes 16 93 16 NOTES ...