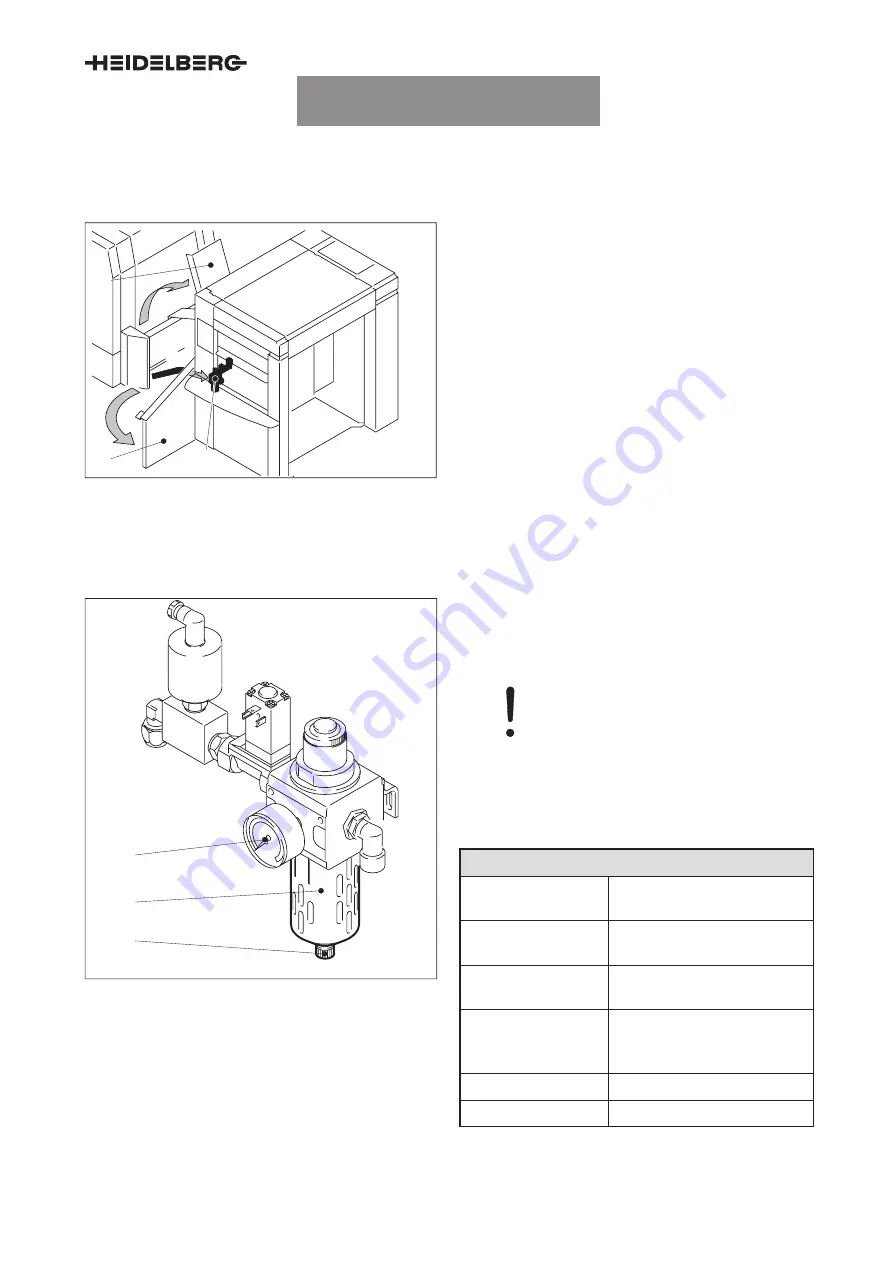
GR FS9040026000000000
GR FS9040025000000000
Maintenance
confidential
D.3.9
4
Service activities on the compressed-air control unit
4.1
Compressed-air control unit
3
1
2
Fig. 8
Location of the compressed-air control
unit
Place of installation
1
Feeder table
2
”Feeder” guard
3
Compressed-air control unit
The compressed-air control unit is installed on O.S.
underneath the feed table.
4.1.1
Compressed-air control unit – checking and, if necessary, the condensate
1
3
2
Fig. 9
Compressed-air control unit
1
Manometer
2
Glass cylinder
3
Drain plug
Caution –
The glass cylinder of the compressed-
air control unit (Fig. 9/1) must never be
filled completely with condensation wa-
ter. The condensation water may enter
in the pneumatic system and destroy
the pneumatic valves and pneumatic
cylinders.
Maintenance point description
Maintenance inter-
val
750 000 prints, or every
week
Maintenance loca-
tion
O.S.
Accessibility of lubri-
cating points
Open the ”feeder” guard.
Fold up the feed table.
Number/type/main-
tenance work
Check the compressed-air
control unit for condensation
water. Drain it if necessary.
Tool
–
Lubricant
–
Tab. 6
UTKFS9040003000000000
UTKFS9040003000000000003
Содержание Speedmaster CD 102
Страница 6: ...Main chapter overview A 2...
Страница 20: ...Main chapter overview B 2...
Страница 114: ...Preset Plus Feeder confidential C 1 76...
Страница 118: ...Main chapter overview D 4...
Страница 120: ...Chapter overview D 1 2...
Страница 134: ...General information confidential D 1 16...
Страница 136: ...Chapter overview D 2 2...
Страница 146: ...Chapter overview D 3 2...
Страница 166: ...Maintenance confidential D 3 22...
Страница 170: ...Index E 4 V VISCOGEN KL 300 Lubricant of the central grease lubrication D 1 10 W Washing fluid D 1 14...